Vacuum Brazed Diamond Saw Blades Factory Supplier
Vacuum Brazed Diamond Saw Blades can be supplied by Eonyx, which is the leading manufacturer of diamond saw blades. Our sophisticated factory can supply 20,000 pieces of saw blades per month. As a professional supplier, we can guarantee competitive wholesale price and stable quality.
Sizes of Vacuum Brazed Diamond Saw Blades
The regular diameters of diamond saw blades range from 100mm to 3500mm. Among them, the popular sizes are: 2 inch, 3 inch, 3 3/8 inch, 4 inch, 4 3/8 inch, 4 1/2 inch, 5 inch, 5 3/8 inch, 5 1/2 inch, 6 inch, 6 1/2 inch, 7 inch, 7 1/4 inch, 7 1/2 inch, 8 inch, 8 1/4 inch, 9 inch, 10 inch, 12 inch, 14 inch, 16 inch, 18 inch, 20 inch, 24 inch, 26 inch, 30 inch, 36 inch, etc. (110mm, 160mm, 165mm, 255mm, 300mm, 350mm, 400mm, 3m, etc.)
Saw Blades Processing Process
We have been focusing on the technical development and production of diamond tools for more than 28 years.
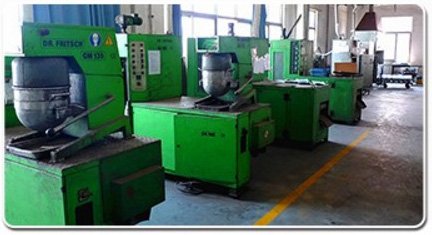
1. Powder Milling
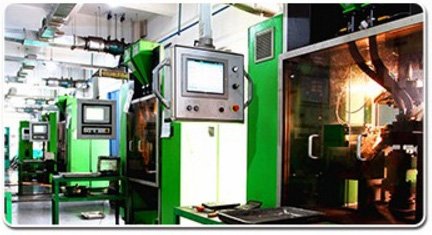
2. Segment Pressing

3. Segment Sintering
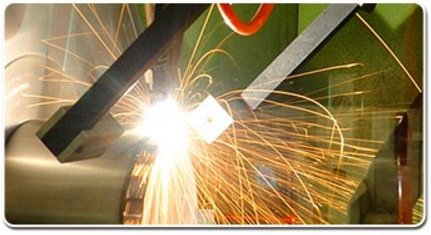
4. Segment Welding
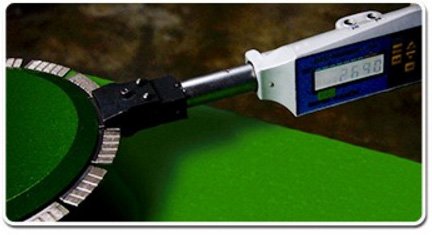
5. Welding Strength Inspection
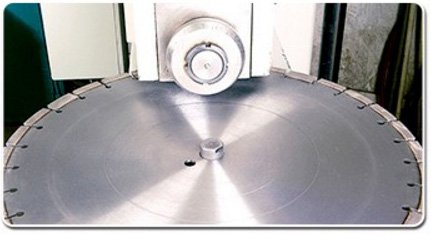
6. Stress Release Rolling
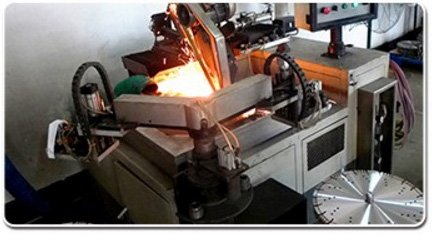
7. Blade Polishing
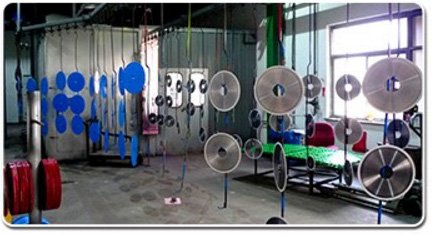
8. Blade Painting
Quality Inspection
Excellent product quality is our commitment to customers as always.
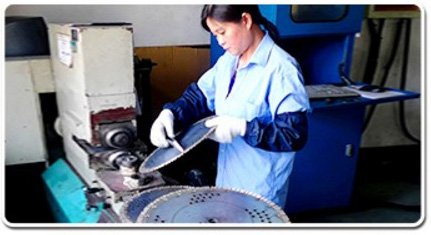
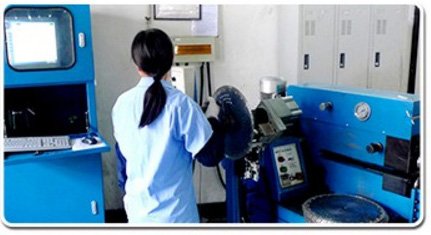
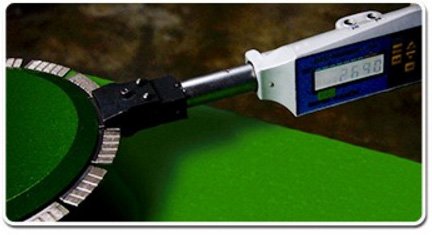
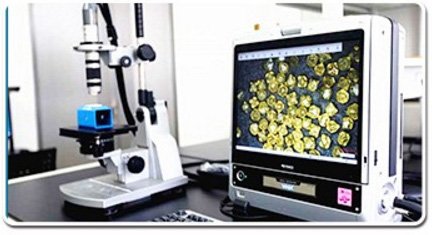
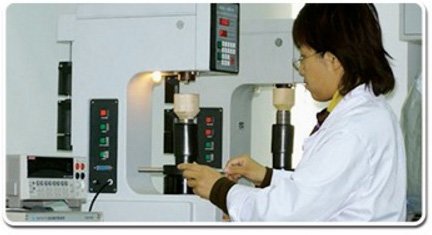
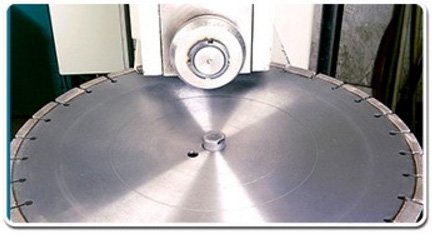
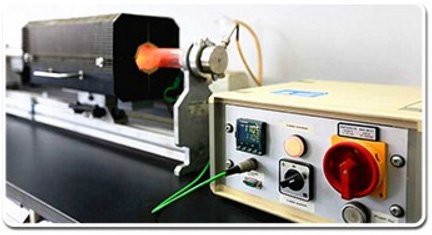
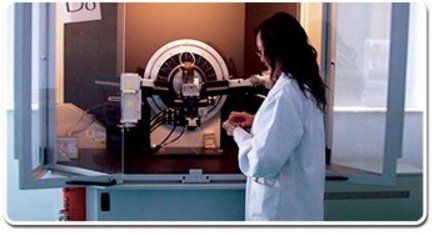
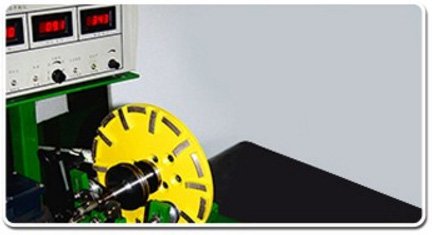
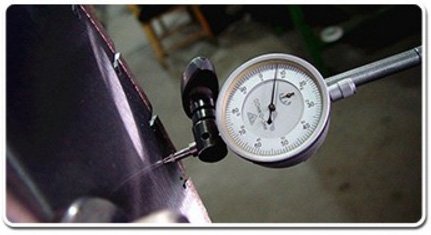
Development of Vacuum Brazed Diamond Saw Blades
In the electrodeposited diamond saw blade, the diamond can only be mechanically inlaid with nickel metal, so it is easy to fall off, and the diamond is arranged in disorder, with low protrusion and small chip space; in the impregnated sintered diamond saw blade, the diamond is arranged disorderly. , the problem of self-sharpening is difficult to solve, and it is difficult to achieve metallurgical combination of diamond and powder. Neither process takes full advantage of the sawing properties of diamond. The vacuum brazed diamond saw blade has the incomparable advantages of the above two diamond saw blades, so the diamond vacuum brazed process has attracted people’s attention in the past 10 years.
Features of Vacuum Brazed Diamond Blades
Vacuum brazed diamond saw blades use diamond surface metallization technology to weld diamond with active solder or nickel-based solder, and form elements or alloys through strong carbides to realize chemical metallurgical bond between diamond and saw blade matrix, which greatly improves the performance of diamond. ‘s holding power. In addition, the diamond can protrude 2/3, and it is not easy to fall off, and it also creates favorable conditions for sharp cutting and good chip removal. In addition, it is easy to combine with the diamond ordered arrangement technology to realize the reasonable and regular distribution of diamonds on the surface of the saw blade, making full use of the cutting effect of diamond, which can not only save the amount of diamond, reduce the cost of the saw blade, but also improve the cutting efficiency. It can be said that this technology is just in line with the requirements of national economic development to vigorously save energy resources and accelerate the construction of a resource-saving and environment-friendly society.
It is an inevitable trend to replace the electrodeposition process with the diamond vacuum brazed process. Experiments show that compared with the electrodeposition process, the diamond vacuum brazed process can increase the matrix strength by 40%, the diamond holding force by about 22%, the diamond protrusion is as high as 2/3, the electrodeposition process is only 1/3, and the amount of diamond is only 1/3. 1/5 of it.
Research status of diamond vacuum brazed materials
(1) The solder alloy has good wettability to diamond and low wetting angle;
(2) Good ductility;
(3) Good climbing ability, so that the diamond has enough protrusion height and good chip-holding ability;
(4) Form an effective metallurgical chemical combination with diamond, and have a good holding force;
(5) has a lower melting point to reduce the vacuum brazed temperature;
(6) The lower cost is conducive to reducing the cost of vacuum brazed saw blades.
At present, Ni-Cr, Ag-Cu and Cu-Sn alloys are mostly used in the solder of vacuum brazed diamond. Among them, Ni-Cr-based solder is the most widely used, but due to its high vacuum brazed temperature (above 900 ℃), it also increases the tendency of diamond to be graphitized and affects the strength and saw blade life of vacuum brazed diamond. Therefore, it has become a research trend of the current vacuum brazed diamond saw blade to seek the brazing material suitable for diamond with low melting point.
Diamond vacuum brazed special equipment
There are two main types of vacuum brazed equipment currently in use: one is a high-frequency induction welding machine; the other is a high-temperature vacuum furnace. Diamond vacuum brazed special equipment should meet the following requirements:
(1) High frequency induction welding must be welded under vacuum or inert gas protection;
(2) Design the corresponding tooling to facilitate the fixing of the workpiece and the rotation, movement and accurate positioning of the workpiece;
(3) Accurate temperature measurement and control system;
(4) The vacuum furnace should ensure sufficient vacuum degree and stable and uniform temperature field;
(5) There are at least two types of furnaces, one for small batch production or trial production of new products, and one for large working space, which is easy for mass production;
(6) There is an observation port, which is convenient to observe the vacuum brazed process of the saw blade in the furnace;
(7) In order to improve production efficiency, the stages of heating, heat preservation and cooling can be carried out continuously in stages, which can shorten the production cycle and increase the output;
(8) Good process control system.
Inventory and Packaging
Sufficient inventory to ensure delivery and professional packaging to ensure safe transportation. Inner packaging: diamond saw blades are covered by anti-rust paint and plastic, then packed in paper box. Outer packaging is according to the shipping method, if by air, we recommend carton which could reduce weight; if by sea, we recommend crate which is seaworthy. Other packaging is also available upon your request.
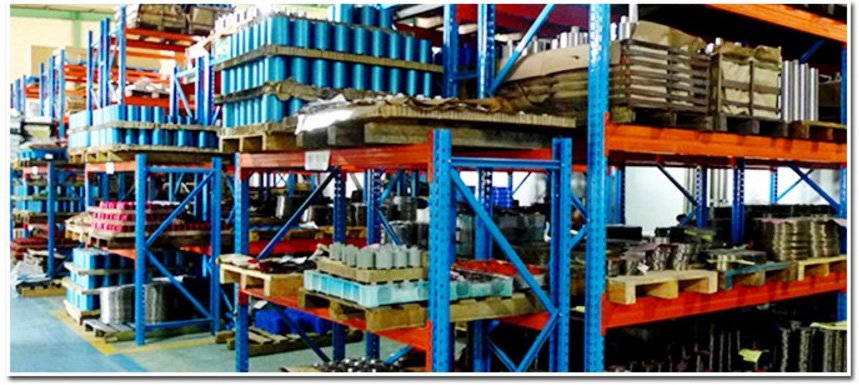
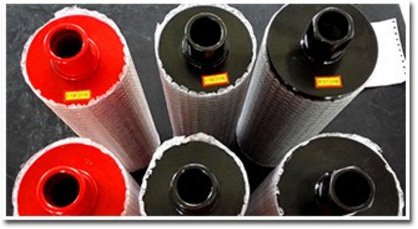
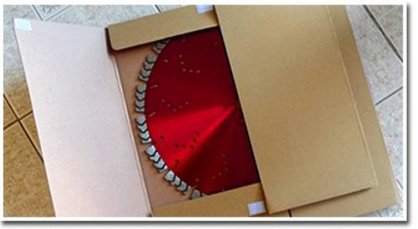
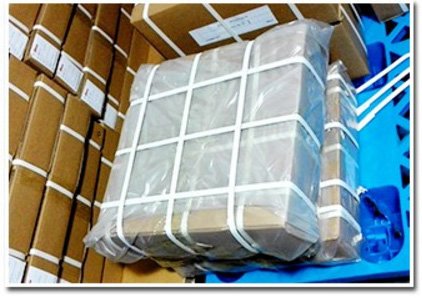
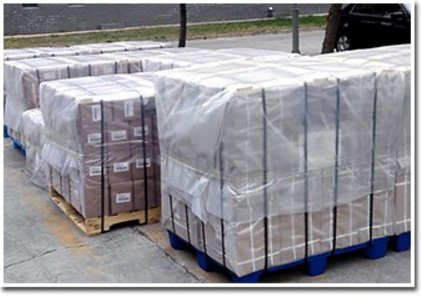
Application of Diamond Cutting Blades
For multi blade cutter, gang saw blade, bridge cutting machine, single arm cutting machine, manual handing machine, able cutting machine, etc. Designed for various hardness stone (soft, medium hard and very hard stones) cutting: granite, marble, sandstone, onyx, limestone, travertine, quartz stone, artificial stone, andesite, volcanic, lava stone, basalt, microcrystal stone, blue stone, dolomite and construction materials (concrete, tile, ceramic, asphalt, floor) to reduce segment cost and increase cutting efficiency.
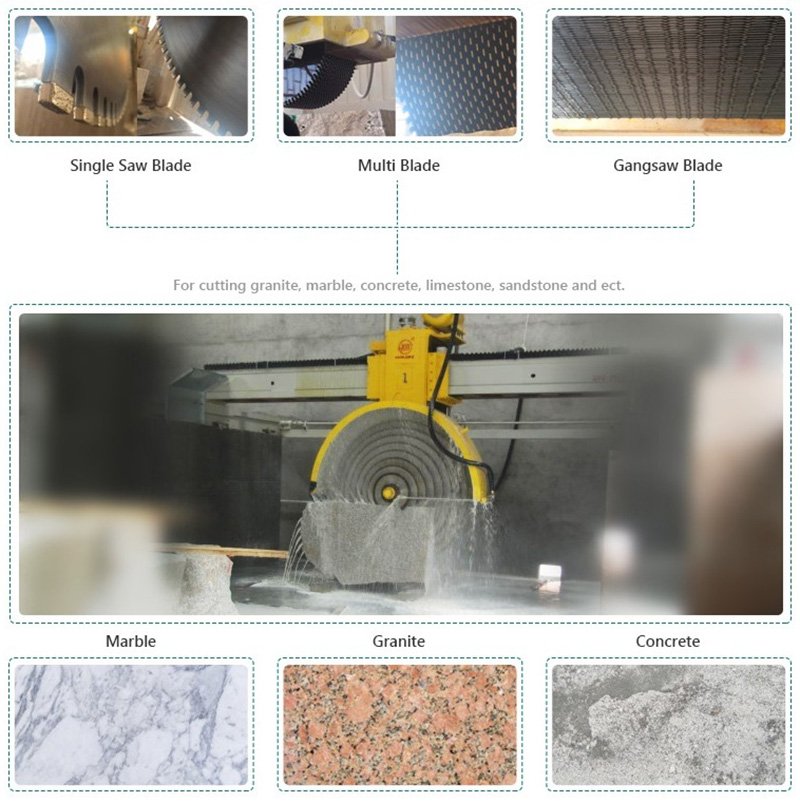
Development of multi-layer abrasive diamond vacuum brazed tools
At present, most vacuum brazed diamond tools are single-layer vacuum brazed products, and the life of single-layer vacuum brazed diamond tools mainly depends on the wear resistance of single-layer diamond. If the diamond wears and destroys one day, the life of the saw blade is about to end. Therefore, to further improve the life of diamond saw blades, multi-layer diamond vacuum brazed tools must be developed.
Process advantages of vacuum brazed diamond saw blades
Diamond is a special elemental carbon whose crystal structure belongs to the equiaxed face-centered cubic system. The bonding bonds between carbon atoms in diamond are sp hybrid covalent bonds, which have high binding force, stability and directionality. The unique crystal structure enables diamond to have the highest hardness, rigidity and excellent wear resistance, corrosion resistance and chemical stability in nature. The excellent physical and mechanical properties of diamond determine that it is an ideal raw material for making saw blades for hard and brittle materials, and is widely used in the processing of hard alloys, engineering ceramics, optical glass, semiconductor materials, granite and other hard and brittle materials.
Vacuum brazed diamond saw blade refers to the vacuum brazed connection of solder that can produce chemical reaction with diamond abrasive and metallurgically bond with steel substrate to make diamond abrasive and saw blade with high efficiency, long life and good processing quality. At present, diamond abrasives and saw blades used in production are generally made by sintering or electroplating processes. The abrasive grains are only mechanically embedded and embedded in the binder layer, and the holding force is small. It is easy to cause the abrasive to fall off prematurely due to insufficient holding force, which reduces the service life of the saw blade. On the other hand, in sintered and electroplated saw blades, the abrasives are randomly distributed, the exposed height of abrasive particles is low, and the chip space is small, which is prone to adhesion and blockage of abrasive chips during grinding, which reduces the processing efficiency of the saw blade.
Due to the above-mentioned defects of sintered and electroplated diamond abrasive saw blades, its application in some fields is greatly restricted. Therefore, in the 1990s, the research work of using vacuum brazed technology and selective cloth technology to make diamond abrasive saw blades was carried out. After more than ten years of unremitting efforts, the problems of low abrasive holding strength and random distribution of abrasives have been fundamentally solved. , The developed series of vacuum brazed gold mesh stone saw blades show excellent performance unmatched by sintered and electroplated diamond saw blades in some application fields.
Why choose vacuum brazed diamond saw blades
(1) High bonding strength, with the help of high temperature vacuum brazed chemical metallurgy at the interface of abrasive, solder and matrix has high bonding strength, the thickness of solder bonding layer only needs to be maintained at 20% to 30% of the abrasive height. It is level enough to hold the grit firmly in heavy-duty, high-efficiency grinding that no other blade can match.
(2) The abrasive exposure is high, usually reaching 70% to 80% of the abrasive height, so the saw blade becomes sharper, and the grinding force and grinding temperature are significantly reduced.
(3) The chip holding space is large, which becomes more abundant due to the high abrasive exposure, and it is not easy to cause the failure of the saw blade due to chip clogging.
(4) The utilization rate is high and the service life is long. The abrasive on the vacuum brazed saw blade can generally be fully utilized to more than 70% to 80% of its own height, except for a very small part of the abrasive.
(5) High structural strength, it is the only high-efficiency grinding wheel that can be safely used in ultra-high-speed grinding from 300 to 500m/s to 1000m/s.
(6) Optimal arrangement, using the optimal arrangement of abrasives technology, realizes the optimal arrangement requirements of single-layer (multi-layer) abrasives including end face, cylindrical surface and arbitrarily complex special-shaped surface saw blade, and can meet the needs of industrial scale production .
(7) It has environmental protection significance. Using high-temperature vacuum brazed instead of electroplating to make diamond abrasive saw blades can completely get rid of electroplating, which is a heavy pollution burden, and meet today’s requirements for green and clean manufacturing.
(8) The performance of production equipment and raw materials is good, and the production technology is advanced, which can produce high-efficiency, large-scale and stable production.
In a word, compared with traditional sintered and electroplated diamond saw blades, vacuum brazed diamond saw blades have the advantages of long service life, high processing efficiency and good processing quality. The vigor and vitality of the company has added a new technological and economic growth point.
Contact Us
If you’re interested in Vacuum Brazed Diamond Saw Blades, please feel free to contact us, (E-mail: [email protected] Phone/WhatsApp: 0086-15805032000 or filling out the form below) we will keep providing quality products and excellent service for you.