Matrix Diamond Blades from professional factory supplier
Best Matrix Diamond Blades can be supplied by Eonyx, which is the leading manufacturer of diamond saw blades. Our sophisticated factory can supply 20,000 pieces of saw blades per month. As a professional supplier, we can guarantee competitive wholesale price and stable quality.
Sizes of Matrix Diamond Blades
The regular diameters of diamond saw blades range from 100mm to 3500mm. Among them, the popular sizes are: 2 inch, 3 inch, 3 3/8 inch, 4 inch, 4 3/8 inch, 4 1/2 inch, 5 inch, 5 3/8 inch, 5 1/2 inch, 6 inch, 6 1/2 inch, 7 inch, 7 1/4 inch, 7 1/2 inch, 8 inch, 8 1/4 inch, 9 inch, 10 inch, 12 inch, 14 inch, 16 inch, 18 inch, 20 inch, 24 inch, 26 inch, 30 inch, 36 inch, etc. (110mm, 160mm, 165mm, 255mm, 300mm, 350mm, 400mm, 3m, etc.)
Saw Blades Processing Process
We have been focusing on the technical development and production of diamond tools for more than 28 years.
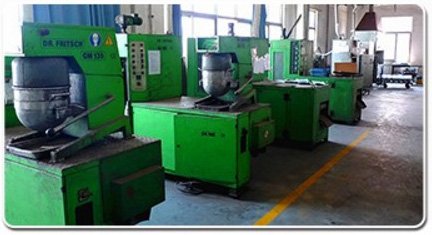
1. Powder Milling
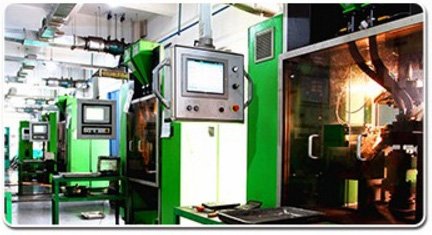
2. Segment Pressing

3. Segment Sintering
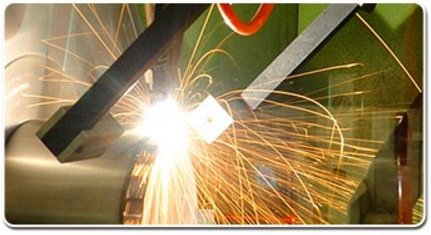
4. Segment Welding
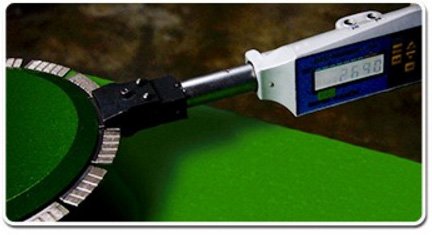
5. Welding Strength Inspection
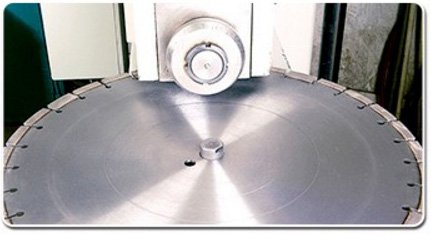
6. Stress Release Rolling
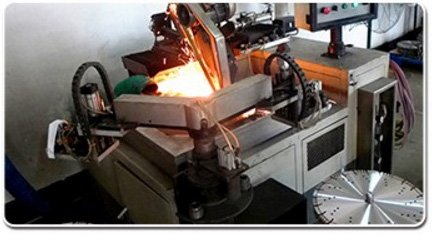
7. Blade Polishing
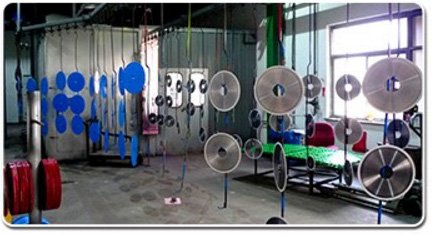
8. Blade Painting
Quality Inspection
Excellent product quality is our commitment to customers as always.
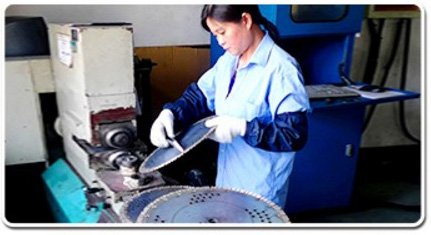
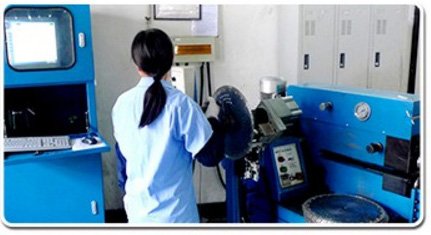
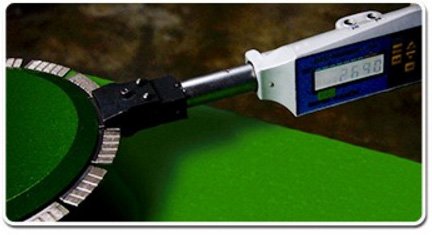
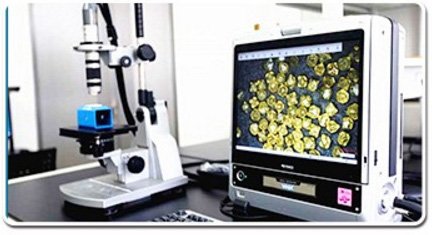
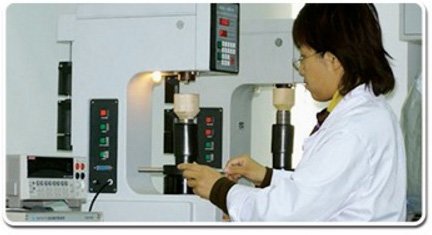
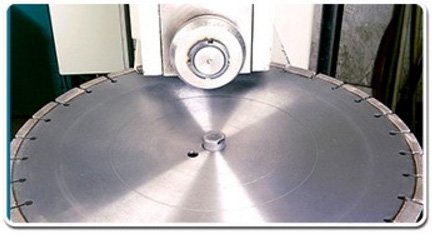
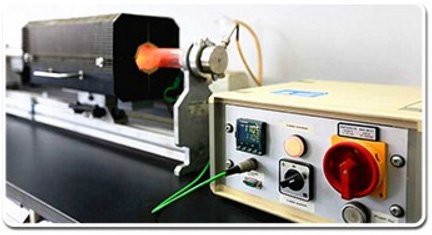
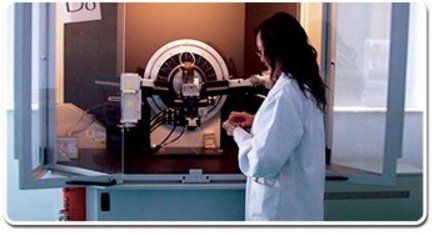
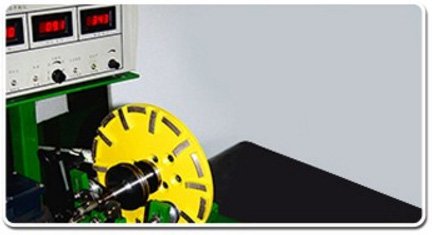
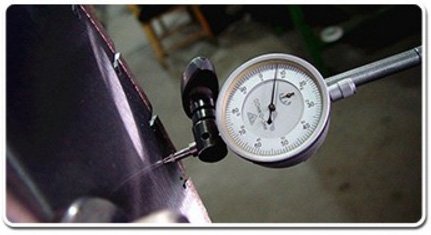
Advantages of orderly arrangement of diamonds
In conventional diamond saw blades, diamonds are randomly and disorderly arranged in the metal matrix, so diamonds are prone to segregation and aggregation in the diamond segments. In the diamond-enriched area, the diamond concentration is high, the single diamond sawing force is small, and it is easy to be polished and worn, and it is easy to block and hinder the removal of cuttings, resulting in a decrease in sawing efficiency. In the diamond sparse area, due to the excessive workload and high impact force of a single diamond, the diamond is easy to break and fall off. Therefore, the saw blade with disordered arrangement of diamonds has the problems of low sawing efficiency, short tool life and contradictory sawing efficiency and life.
In recent years, in the diamond tool industry, the design and process of the orderly arrangement of the diamond segments diamonds have been introduced, which can evenly arrange the diamonds with the optimal spacing in the production of the diamond segments. The experimental data show that the orderly arrangement can improve the sharpness and life of the diamond saw blade at the same time, and reduce the diamond concentration and save the cost.
The performance of a diamond tool depends on a number of factors, the characteristics of the diamond being used i.e. the size, strength and structure of the diamond is one of the most critical factors. The life, power consumption and sawing efficiency of diamond tools ultimately depend on the combined action of all diamonds on the tool surface (in the diamond segments), including the particle size, concentration of diamonds in the diamond segments, diamond protrusion height, distance between diamonds and its arrangement, etc. The relationship between diamond uniform distribution and ordered arrangement and other parameters and its influence on the performance of diamond tools.
When the diamonds are randomly distributed and disordered, the diamonds are too dense at a, and the diamond spacing is too small. The diamond is mainly in the grinding and polishing stage, the cutting force of each diamond is small, the sawing life is long, and the sawing efficiency (speed) is low. When the diamond segregates at c, the diamond spacing is too large, each diamond bears a large load, the cutting force is large, the slag discharge gap is smooth, the sawing efficiency is high, and the speed is fast. However, diamond is easy to dry off and chip, the matrix wears quickly, and the service life is short.
When the diamonds are evenly distributed and arranged in an orderly manner, the diamond spacing can be optimized according to the different sawing objects and sawing conditions. At this time, the diamonds can be effectively used, play the role of cutting, and can fully remove chips and flush cooling, which can achieve both The optimization purpose of improving sawing efficiency and improving saw blade life.
The cutting efficiency of diamond on the saw blade surface depends on the distribution of diamond spacing and the wear condition of individual diamonds. The research shows that the average diamond spacing of the matrix diamond blades is 4mm, the diamond is 40/50 mesh, and the concentration is 11ct/cm. After sawing, the spacing of 85% diamonds in the matrix diamond blades is 27mm, while the ordinary saw blades are only 60%. At this time, the sawing time and sawing force of the matrix diamond blades are significantly improved. The increase of diamond content has little effect on the cutting load, but the sawing time is significantly prolonged, resulting in a significant improvement in the life and efficiency of the saw blade.
Crafting of Matrix Diamond Blades
There are mainly the following methods to realize the orderly arrangement of diamonds in the diamond segments.
Template method
The first step of the method: Mix the matrix powder evenly, add appropriate organic binders and solvents, etc., and make a thin layer 100 by rolling method. According to the distribution and arrangement of diamonds, a template 110 is made, and its aperture 114 must be large. The size of a single diamond is smaller than the size of two diamonds, ensuring that one diamond enters the die hole, and the thickness of the template is 1/3~2/3 of the average diamond particle size. The second step: the diamond 20 is distributed on the template, and the diamond is pressed into the matrix through the hole 114 of the template 110 with a steel flat plate 120. The third step: remove the excess diamond on the template, remove the template, and press the diamond into the thin layer 100 of the matrix with a steel flat plate. Step 4: Repeat the above steps and methods to press the diamond into the other side. Then, the diamond segments is assembled with multi-layered diamond thin layers, and then sintered in a graphite mold to form the diamond segments. This method can accurately distribute and arrange the diamonds evenly as required, but the efficiency is low and manual operation is required, so mass production and industrialization are difficult.
Dispensing method
The device of the dispensing method consists of a glue reservoir and a micro-metering diamond segments. The micro-metering diamond segments consists of a piezoelectric driver, a thermistor, a heating coil and a power supply, as well as a metering control device. The glue is fed from the glue storage tank to the micrometer through the feeding tube. When a voltage pulse is applied, the piezoelectric actuator will shrink, thereby discharging a glue drop. The maximum discharge frequency is 2000Hz, and the maximum nozzle diameter is 40um. The device can measure and batch the glue with higher viscosity. According to the position of the workpiece and the movement of the glue dispenser, the glue can be evenly arranged on the workpiece, and then the diamonds are spread on the glue droplets to form a uniform arrangement of the diamonds.
ARIX Auto Layout System
The ARIX automatic arrangement system was developed by a Korean company. Since 2001, the company has been able to successfully arrange diamonds in the diamond segments evenly and orderly by June 2003, but the production efficiency cannot meet the requirements. After a year of intensive efforts, in December 2004 announced the completion of the ARIX automatic arrangement system, which can 100% control the spacing of the inner diamonds in the diamond segments, and can automatically produce 50,000 diamond segmentss per month. Now our company has also mastered this technology. With the progress of the diamond tool industry, the advantages of orderly arrangement of diamonds in the diamond segments have been recognized by people, and some process technologies of orderly arrangement have also appeared, but most of them have low production efficiency and are not suitable for mass production. Therefore, how to realize the industrialization of the orderly arrangement of diamonds in the diamond segments is the focus of research.
Inventory and Packaging
Sufficient inventory to ensure delivery and professional packaging to ensure safe transportation. Inner packaging: diamond saw blades are covered by anti-rust paint and plastic, then packed in paper box. Outer packaging is according to the shipping method, if by air, we recommend carton which could reduce weight; if by sea, we recommend crate which is seaworthy. Other packaging is also available upon your request.
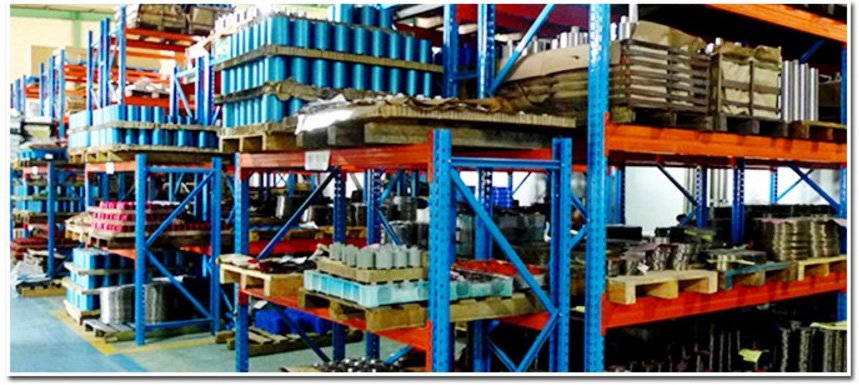
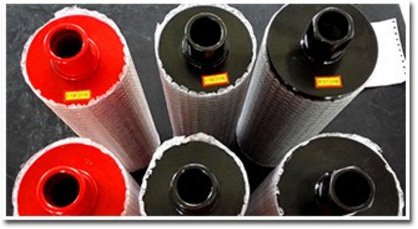
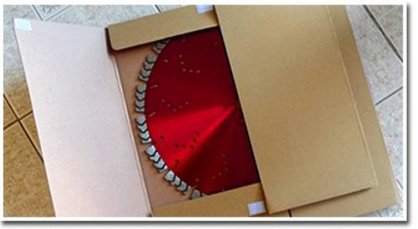
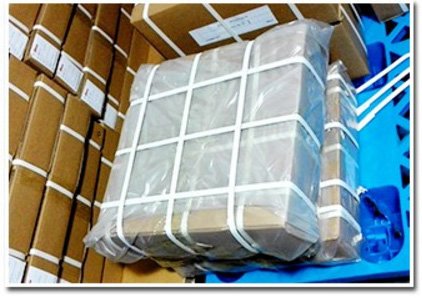
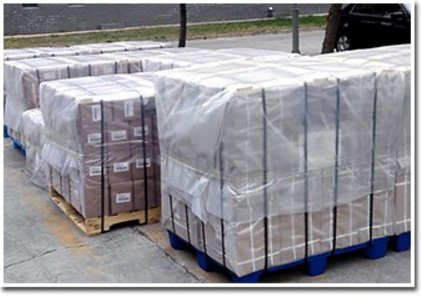
Application of Diamond Cutting Blades
For multi blade cutter, gang saw blade, bridge cutting machine, single arm cutting machine, manual handing machine, able cutting machine, etc. Designed for various hardness stone (soft, medium hard and very hard stones) cutting: granite, marble, sandstone, onyx, limestone, travertine, quartz stone, artificial stone, andesite, volcanic, lava stone, basalt, microcrystal stone, blue stone, dolomite and construction materials (concrete, tile, ceramic, asphalt, floor) to reduce segment cost and increase cutting efficiency.
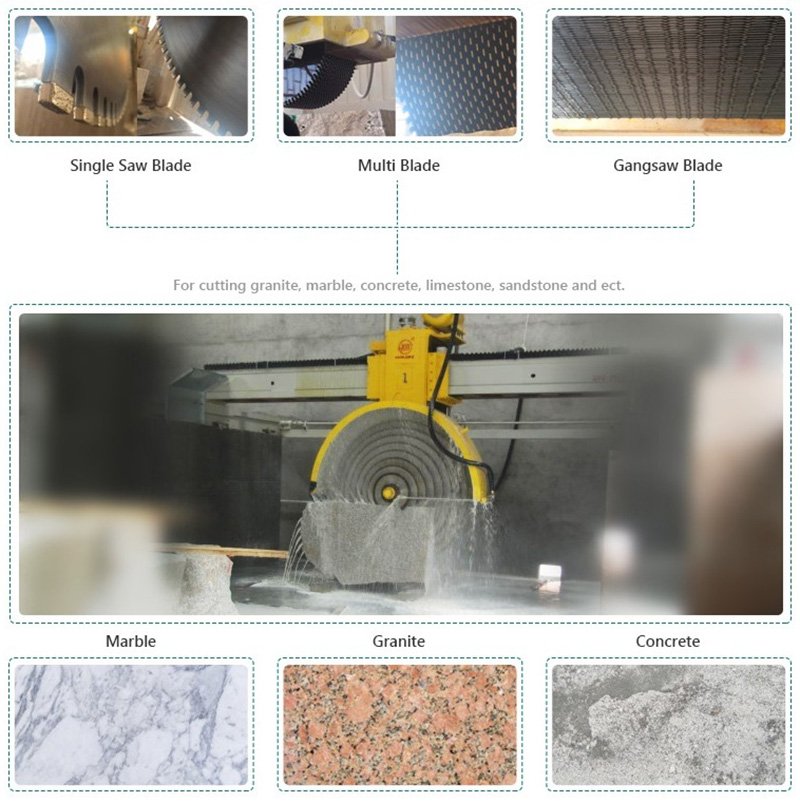
The production process of Matrix Diamond Blades
Our company has successfully researched a production process method for matrix diamond blades. The specific production steps are as follows:
(1) Diamonds cannot be arranged in an orderly manner in the powder, so the matrix powder should be cold-pressed into a sheet-like thin blank, and then the diamonds are arranged on the thin blank. The number of layers of thin blanks in a diamond segments is calculated according to the number of designed diamond layers (the number of thin and bad layers = the number of diamond layers – 1). The amount of powder used in each layer of thin blanks = the total weight of the diamond segments / the number of layers of thin blanks.
(2) According to the designed diamond arrangement, use a medium and small power YAG solid-state laser to punch holes on the copper plate. The thickness of the selected copper plate is slightly larger than the average diameter of the diamond, about 05mm, to ensure that the diamond can completely fall into the hole. The size of the hole should be greater than 1 times the average diameter of the diamond and less than 2 times the average diameter, so as to ensure that each hole can enter a diamond instead of two diamonds.
(3) Spray a thin layer of special pressure-sensitive adhesive on the thin body of the carcass, then cover the punching template on the thin blank, sprinkle the diamond on the copper plate, and sweep the diamond with a special soft brush to make the There is a diamond in each hole. When the punching template is uncovered, the diamonds form an orderly arrangement on the matrix.
(4) Combine the multi-layer diamonds with diamonds and use a four-column hydraulic press to manually cold-press into the shape of the diamond segments. In order to eliminate the sprayed pressure-sensitive adhesive as much as possible, put the cold-pressed diamond segments in the reduction furnace and place it at a temperature of 400 ° C for about half an hour to fully volatilize the glue.
(5) The diamond segments from the reduction furnace is moulded and sintered together with the pressed transition layer. When sintering, a vertical die is used for lateral pressure to ensure that the diamonds are still in an orderly arrangement after sintering.
(6) Demolition, arc grinding, laser welding, cutting edge, trimming.
Difference analysis of diamond wear in saw blades with and without order
The diamonds in the matrix of traditional saw blades are randomly distributed, that is, the diamonds are arranged disorderly on the cutting end face of the diamond segments, and the diamond particles do not maintain their internal spacing according to the average distance. In the process of high-speed rotation of the saw blade, the force of a single diamond is closely related to the number of diamonds in the cutting area. If the diamonds are not evenly distributed, in the diamond-intensive area, the single diamond will not be able to press the rock surface effectively, so that the rock surface will be micro-broken, and the diamond will gradually be carved into the rock. The diamonds in this area are easy to be polished, which not only cannot break the rock, but also protects the matrix from wear, which affects the self-sharpening of the saw blade, resulting in the failure of the next layer of diamonds to emerge in time. According to the above analysis of diamond wear morphology, the greater the percentage of polished diamond particles in the total number of diamond particles, the higher the wear resistance of the tool, but the worse the tool’s sharpness, so that the performance of the tool will gradually passivate. In areas where diamonds are scarce, each diamond is subjected to excessive force. Especially in the diamond sparse area, due to the large distance between the front and rear diamonds, when the diamond enters the working state from the idling state, the impact force on the diamond is very large. A large impact force will destroy the matrix inlaying the diamond, causing the diamond to fall off. If the impact strength of the diamond is not enough, the large impact force will cause the diamond to be broken as a whole. Both of these conditions will affect the performance of the diamond saw blade. If the shedding rate of the diamond is too high, the sharpness of the saw blade will be very poor, and even sparks will occur and the cutting will not work. If a large number of diamonds are broken under the impact, the utilization rate of these diamonds is quite low, resulting in insufficient overall life of the saw blade.
If the gold and stone particles are arranged in an orderly manner in the diamond segments matrix, the distance between the front and rear diamonds is almost the same, and the number of diamonds in the cutting area is the same at any moment when the saw blade is cutting. In this way, during the cutting process, each diamond bears the same cutting force, and at the moment of entering the working state from idling, the impact force it bears is also the same. Then the maximum force that the diamond can withstand can be calculated according to the total cutting force of the matrix diamond blades during cutting, as well as the compressive strength, impact strength, hardness and wear resistance of the diamond. Thus, a reasonable spacing and the number of diamond particles that should be reached in the cutting area are obtained, so that each diamond can exert its maximum effect and improve the sharpness and life of the matrix diamond blades.
Development direction of Matrix Diamond Blades
According to the principle of saw blade cutting, an orderly arrangement of dense front and sparse rear can be designed. The larger the lateral distance between two adjacent diamonds, the larger the chips produced by diamond cutting, which means the heavier the cutting task each diamond undertakes. Then in the presence of a nozzle, the last diamond on the lip surface of the former diamond segments and the first diamond on the lip surface of the latter diamond segments are two adjacent diamonds, and the lateral distance is much greater than The horizontal spacing of the design. Coupled with the impulse generated by the matrix diamond blades during the cutting process, after passing through a nozzle, the moment when the next diamond segments collides with the rock is the largest, that is, the first few diamonds on this diamond segments have the largest impact force. Therefore, it can be inferred that in the diamond saw blade, after passing through a nozzle, the cutting task and impact force of the first few diamonds on the next cutting diamond segments are the largest. This is the reason that one end of the diamond segments often wears faster than the other end in traditional saw blades, and it is also the reason why the first few rows of diamonds after passing through the nozzle fall off or break more after a period of time when saw blades are arranged in an orderly manner. Therefore, an orderly arrangement of dense front and sparse rear can be designed, so that more diamonds can share the larger cutting task and impact force after passing through the nozzle. The production of front dense and rear sparse diamond segmentss is difficult to achieve for ordinary saw blades, but for matrix diamond blades, the production process of small diamond segmentss is not much different from that of general matrix diamond blades. It should be noted that in the process of welding the diamond segments, pay attention to the welding direction of the diamond segments, so that the end with the largest diamond density in the diamond segments points in the same direction, and also pay attention to the direction in the process of cutting edge.
Contact Us
If you’re interested in Matrix Diamond Blades, please feel free to contact us, (E-mail: [email protected] Phone/WhatsApp: 0086-15805032000 or filling out the form below) we will keep providing quality products and excellent service for you.