Characteristics of Eonyx Marble Diamond Segments
1. The diamond segments possess good sharpness and high efficiency during the process of cutting, as well as long lifespan.
2. Good cutting result: smooth cutting, flat surface and even size.
3. Stable cutting and narrow cutting gap to ensure minimum stone waste.
4. Various segment shapes available: M shape, K shape, Taper shape, Flat shape, T shape, U shape, etc.
5. As a professional supplier, we can guarantee competitive wholesale price and stable quality.
6. Production capacity: our professional factory can supply 90000 sets/month.
7. Matured formula designing and testing system.
The structure of marble stone diamond segment
The design of the structure and size of the diamond segment should be considered in combination with diamond, matrix formulation, matrix, manufacturing process, material to be cut, cutting equipment, cutting method, and cutting parameters. It can be said that under the given cutting conditions, a reasonable structure and size of the diamond segment will help the diamond in the diamond segment and the matrix to achieve adaptive wear. The diamond has always maintained a good state of high exposure, the matrix firmly holds the diamond, the diamond segment does not drop, the sawing power is minimized, the sawing state is stabilized, and the sawing gap is minimized.
For ordinary diamond segments (with a rectangular cross section and uniform performance), the edges will be worn and rounded soon after cutting, and the working layer of the diamond segment has a semi-arc shape, which increases the contact area between the diamond segment and the stone. , the cutting resistance will increase significantly, or when the output power of the saw machine is constant, the cutting force of each diamond will decrease, and the depth of the diamond cutting into the rock will decrease, resulting in a decrease in cutting efficiency. It is easy to be blunted by the action. If you want to maintain efficiency, you can only increase the sawing rate and cutting pressure, which in turn makes the diamond head subject to a great lateral extrusion, which is easy to cause the saw blade to vibrate, heat, deform and deviate, so that the processed The thickness of the plate is uneven or uneven, and the substrate is difficult to reuse or cannot be used at the time due to deformation, wear, and cracks. However, the large extrusion of the diamond segment may lead to local fracture or chipping. The greater the thickness of the diamond segment, the more serious the above situation will be.
In the cutting process, the ideal working surface of the diamond segment is that the front is undulating in a peak and valley shape (the edges on both sides are raised), and the side is inclined. The front of such a diamond segment is equivalent to having multiple guide edges, which improves the extrusion condition of the working layer and reduces the lateral pressure, thereby achieving the purpose of improving cutting efficiency and cutting quality. However, this working surface adds more side wear surfaces, so it is easy to cause the diamond to break and fall off. Therefore, it is necessary to choose high-quality, fine-grained, and preferably surface-coated diamonds. At the same time, it is required that the matrix has a high binding ability to diamond and its coating layer, and the matrix should be dense. The sloping profile of the diamond segment reduces contact with the rock, which reduces wear and cutting resistance for improved sharpness and longevity.
In production, the frontal peaks and valleys of the diamond segment are realized by making a “sandwich” layered structure. The “sandwich” structure must be alternately arranged according to the hard layer and the soft layer. The edge layer must be a hard layer and a soft layer. Iron flakes or powder can be used. The side inclined surface of the diamond segment is mainly realized by making it into a stepped shape. Sometimes there are grooves on the side surface, which is beneficial to further reduce the side wear and cutting resistance, and also can play the role of chip containment, chip removal, and enhanced cooling.
Diameter (mm) |
Diameter (inch) |
Steel Core Thickness(mm) |
Segment Dimension (mm) |
Segment Number |
---|---|---|---|---|
300 | 12″ | 2.2 | 40×3.2×10(15,20) | 21 |
350 | 14″ | 2.2 | 40×3.2×10(15,20) | 24 |
400 | 16″ | 2.6 | 40×3.6×10(15,20) | 28 |
450 | 18″ | 3.0 | 40×4.0x10(15,20) | 32 |
500 | 20″ | 3.0 | 40×4.0x10(15,20) | 36 |
600 | 24″ | 3.6 | 40×4.6×10(15,20) | 42 |
700 | 28″ | 4.0 | 40×5.0x10(15,20) | 50 |
800 | 32″ | 4.5 | 40×5.5×10(15,20) | 57 |
900 | 36″ | 5.0 | 24×7.0/6.2×13(15,20) | 64 |
1000 | 40″ | 5.0 | 24×7.0/6.2×13(15,20) | 70 |
1200 | 48″ | 5.5 | 24×7.4/6.6×13(15,20) | 80 |
1400 | 56″ | 6.5 | 24×8.4/7.6×13(15,20) | 92 |
1600 | 64″ | 7.2 | 24×9.2/8.4×13(15,20) | 108 |
1800 | 72″ | 7.5 | 24×10/9.2×13(15,20) | 120 |
2000 | 80″ | 8.0 | 24×11/10×15(20) | 128 |
2200 | 88″ | 9.0 | 24×11/10×15(20) | 132 |
2500 | 110″ | 9.0 | 24×12/11×20(30) | 140 |
3000 | 120″ | 9.3 | 24×13/12×20(30) | 160 |
3500 | 140″ | 9.5 | 24×13.5/12.5×20(30) | 180 |
Other specifications are available upon request. | ||||
Silent and non-silent blades are available for choice. |
Application of Diamond Segments
For 300mm-3500mm saw blades, diamond frame gang saw blades, diamond core drill bits, diamond grinding cup wheels and different machines (multi blade cutter, gang saw blade, bridge cutting machine, single arm cutting machine, manual handing machine, able cutting machine, etc.) Diamond segment types include sandwich segment, multi-layer segment and orderly arrayed segment and carbide tips, every type is designed for various hardness stone (soft, medium hard and very hard stones) cutting: granite, marble, sandstone, onyx, limestone, travertine, quartz stone, artificial stone, andesite, volcanic, lava stone, basalt, microcrystal stone, blue stone, dolomite and construction materials (concrete, tile, ceramic, asphalt, floor) to reduce segment cost and increase cutting efficiency.
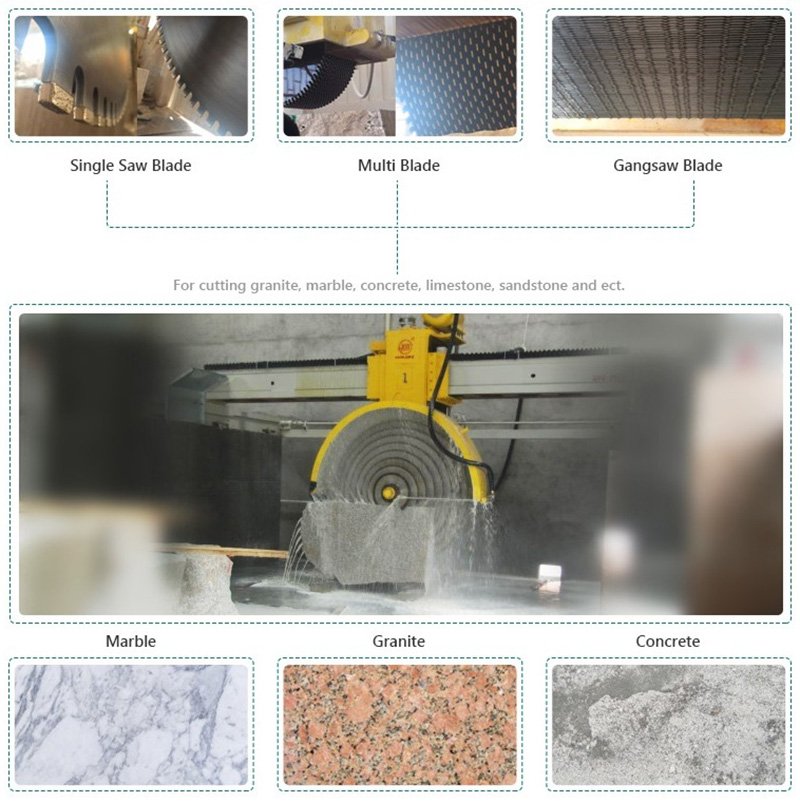
Packaging and Shipping for Marble Cutting Diamond Segments
One set of diamond segments packed in 1 box, 10 boxes in a carton and then cartons packed in crate. Besides the diamond segments could also be packed according to your specific request.
Rust proofed before packing – Water proofed – Impact protection.
Urgent order with less weight or samples, courier service is recommended;
Normal (regular) order which weight over 45kgs, delivering by air is recommended;
Big diameter saw blades or heavy weight products, shipping by sea is recommended.
Eonyx will offer advices according to the actual order requirements.
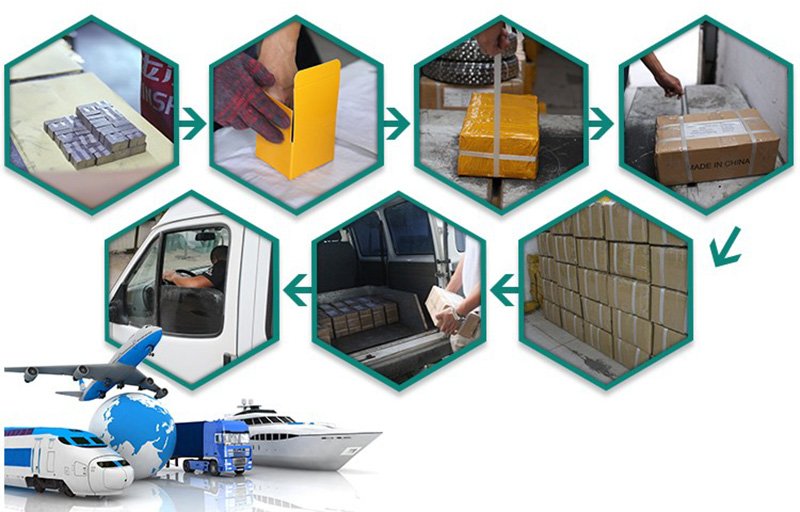
Method of designing the soft and hard layer of “sandwich” diamond segments
(1) The iron sheet for the soft layer, the thickness of the iron sheet used is mostly 0.8~1.0mm, and the length and width should be slightly smaller than that of the diamond segment. Using iron sheet as the soft layer is convenient for operation and low in cost, but requires high purity and clean surface of the iron sheet, and is only suitable for use with the high temperature matrix formula, which limits the adjustment of the wear resistance of the soft layer. In order to enhance the bonding between the iron sheet and the hard layer, some manufacturers use borax aqueous solution to boil the iron sheet or punch the iron sheet.
(2) Diamond-free powder is used for the soft layer. Compared with the iron sheet, the use of the powder soft layer is more conducive to the combination with the hard layer, and it is convenient to adjust the wear resistance of the soft layer, thereby effectively adjusting the cutting performance of the diamond segment. The soft layer can use the same formula powder as the hard layer, or powder with different composition. The latter needs to consider that its hot pressing temperature should be comparable to that of the hard layer, it can be well combined with the hard layer, and the cost is low. Use non-diamond powder as the soft layer, and the layer thickness should not be too large, otherwise it will affect the retention of the hard layer and the cutting life of the saw blade.
(3) The diamond-containing powder for the soft layer can have the following design ideas:
1) The matrix formula, diamond quality and diamond particle size of the hard layer and the soft layer are the same, but the diamond concentration is higher than that of the soft layer;
2) The matrix formula, diamond quality and diamond concentration of the hard layer and the soft layer are the same, but the diamond particle size is finer than that of the soft layer;
3) The matrix formula, diamond particle size and diamond concentration of the hard layer and the soft layer are the same, but the diamond quality is better than that of the soft layer;
4) The formula of the hard layer is the same as that of the soft layer, but at the same time, the diamond quality, particle size and concentration are adjusted so that the wear resistance of the hard layer is higher than that of the soft layer;
5) The hard layer matrix is more wear-resistant than the soft layer, and diamond is used the same;
6) The formula of the hard layer and the soft layer is different. By adjusting the diamond quality, particle size and concentration at the same time, the wear resistance of the hard layer is higher than that of the soft layer.
The soft layer contains diamond, which can participate in cutting and is beneficial to the retention of the hard layer, so the layer thickness can be designed to be larger. When actually designing the “sandwich” diamond segment, it is also necessary to adjust the number of layers and the thickness of the layers according to the specific use conditions.
Cloth, hard layer formula, and the difference in wear resistance of soft and hard layers to achieve a good “peak and valley” shape and the best cutting effect.
As mentioned above, the circular arc surface of the traditional cuboid diamond segment is not conducive to dry machining. Therefore, tool manufacturers began to distinguish the hard layer and the soft layer to form a concave layer in the middle of the working surface during the machining process. Commonly there are sandwich structure and sandwich structure (also called line structure) diamond segment. Such a design ensures that the working surface is concave during the processing process, which can make the contact area between the diamond segment and the processing object smaller, and have better diamond edge performance, thereby improving the cutting efficiency. At the same time, the forces on the two sides of the concave shape can cancel each other out, so that the steel matrix is always kept straight during the processing, and finally the thickness of the processed plate is uniform, and the deformation of the steel matrix is small.
The initial shape of the working face of the diamond segment is also constantly changing, from the traditional parallel to the “V” shape, “K” shape, “M” shape, the change of the initial shape is mainly to change the contact area between the working face of the diamond segment and the processing object, so as to Improve the sharpness of the blade at the beginning of use, that is, shorten the cutting time. Relevant tests show that a reasonable design of the initial working face shape can effectively save 50% of the cutting time.
Manufacturing Points of Stone Diamond Segments
Combining cutting conditions, selecting or designing the best material, formula, and process is the key to the manufacture of large saw blades.
Requirements for the saw blade base
The matrix used for the large diamond saw blade must have sufficient rigidity, strength, toughness and hardness, and the shape and position accuracy such as flatness must be high.
Requirements for diamonds
The selection of diamonds for large saw blades should be considered in combination with cutting conditions, matrix, structure size of diamond segment, and matrix. Generally speaking, the harder the material to be cut, the stronger the friction, the faster the cutting speed and the greater the feed, the greater the impact on the diamond, which is mainly consumed in the form of impact wear, breaking and falling off. On the contrary, the material to be cut is soft If the friction is weak, the cutting speed is slow, and the feed is small, the diamond is mainly consumed in the form of mechanical friction and wear. It is hoped that when sawing, the diamond will be subjected to moderate impact wear and mechanical wear under the premise of fully functioning, and then be slightly broken, broken, and fallen off, so that the saw blade can play the best cutting role.
Premature consumption of diamonds or excessive wear resistance are not conducive to the cutting process. The former is that the diamond falls off or breaks in large pieces before it functions normally. Premature falling off indicates that the matrix is not dense, not wear-resistant, or has a weak grip on the diamond, the cutting speed or feed is too fast, and the material being processed is too abrasive. , and the large pieces are broken, indicating that the diamond quality is poor, the concentration is low, or it has been subjected to excessive impact. Premature consumption leads to low cutting efficiency and low life of the saw blade, which can be improved by adjusting the diamond quality and concentration, the wear resistance of the matrix, using high cutting speed, large depth of cut, and small feed. The diamond is too wear-resistant, it is only ground or polished, and it is not easy to be broken, indicating that the matrix is too wear-resistant or the diamond is too strong, the cutting depth of the saw blade is large, the feed is small, the material to be processed is hard and fine, and the diamond is hard and fine. The quality is too good, the concentration is too high, the diamond particles cut into the rock with a small depth, the diamond particles are impacted and the cutting force is small, so that the saw blade has low cutting efficiency and long life. Therefore, it is necessary to adjust the diamond matrix and adopt low cutting speed, small cutting depth and large feed to promote the micro-breakage of the diamond and accelerate the wear of the matrix, so as to improve the cutting efficiency.
Generally, high-quality diamond has high compression and impact resistance, and can maintain integrity for a long time during cutting. The wear is slow, and it is not easy to produce micro-fractures. Micro-fractures can only occur when encountering highly abrasive materials. But on the other hand, the quality of diamond is good, the crystal form tends to be of equal volume, the surface is smooth, and the carcass is difficult to control. In this way, it is easy to fall off directly. Therefore, for high-grade diamond, surface plating or roughening should be adopted. The particle size should be coarser and the concentration should be lower. Strong adhesion, suitable for cutting strong abrasive materials.
For lower-grade diamonds, due to their poor compression and impact resistance, obvious wear and breakage may occur when cutting general materials, while large pieces of diamonds will quickly collapse and lose cutting ability when cutting difficult-to-machine materials. Therefore, for lower grade diamond, the particle size should be fine and the concentration should be high, and the matrix should be soft and not too wear-resistant, the hot pressing temperature should be low to reduce the impact on the diamond, and the material to be processed should be an easy-to-cut material. It can give full play to the role of these diamonds.
In the case of using high temperature wear-resistant matrix, high-grade diamond and cutting difficult-to-machine materials, if some low-grade diamonds or high-grade diamonds have high quality dispersion, the efficiency and life of sawing tools will be significantly reduced.
In general, the diamond of the diamond blade for making marble saw blades should be diamonds with MBD6 or above, good impact toughness and thermal stability. MBD6~MBD10 diamonds are suitable for medium-soft and easy-cutting materials such as limestone, marble and bluestone below medium-hard. MBD8~SMD25 diamond is suitable for processing medium-hard or medium-abrasive materials such as medium-hard and above marble, medium-hard and below granite, and the diamond should be surface-coated. MBD10~SMD40 diamond is suitable for cutting hard or strong abrasive materials, such as hard granite, sandstone, etc. It is required that the magnetic content of diamond should be low, the thermal stability and impact resistance should be better, and surface plating should be used.
The diamond particle size is mostly 30/35~60/70 mesh. Coarse-grained diamond is suitable for cutting materials with strong abrasiveness, hard and brittle, and coarse grains, and the corresponding matrix should be hard and wear-resistant; fine-grained diamond is suitable for cutting hard, tough, and fine-grained materials, and the matrix should be soft. . The volume concentration of diamond is generally 25% to 50%. When cutting highly abrasive, hard and dense materials, the diamond concentration should be higher. When cutting brittle and weakly abrasive materials, the concentration of diamond should be low.
Requirements for the carcass
The selection of the carcass for large saw blades should be considered in combination with cutting conditions, saw blade specifications, diamond segment structure size, diamond, etc.
Generally, when cutting soft and abrasive weak materials, the carcass should be soft and low wear resistance; when cutting medium hardness, general abrasiveness, hard and fine materials, the carcass should be hard, wear resistance should be low, and the diamond should be controlled. To be strong; for the cutting of strong abrasive materials, the matrix is required to be wear-resistant, and the diamond control must be strong, and at the same time, pay attention to the reasonable selection of cutting parameters. When cutting strong abrasive materials with high hardness, it is easy to form impact, so the cutting speed and depth of cut should not be too large, and fast feed can be performed; while cutting strong abrasive materials with low hardness is the opposite, high cutting speed, large depth of cut and slow feed should be used. This can effectively maintain the cutting efficiency, and at the same time can reduce the wear of the matrix and the wear and tear of the diamond.
Process requirements
Marble saw blade segments are mostly cold-pressed into blanks, then assembled and hot-pressed, and directly loaded with powder (sheets) and hot-pressed; considering the convenience and the repeated use of the substrate, the subsequent work such as welding is mostly performed by customers or specialized services. agency to complete.
(1) Compounding materials: It is necessary to ensure that the environment is clean, the equipment is clean, the material is calculated correctly, the material is weighed accurately, the material is mixed evenly, sealed and stored, and used up regularly.
(2) Hot pressing: The large diamond segment is mostly hot pressed by a high-power resistance hot press. Clean environment, clean utensils, correct feeding, correct stacking, alignment of profiles, flat mounting, symmetrical indenters, symmetrical pads, parallel presses, central placement, alignment of temperature measurement, natural air cooling, and cooling Through unloading.
(3) Cold pressing + hot pressing: There are many manufacturers who cold-press the hard layer of the large diamond segment and the soft layer of powder into sheets, and then alternate (or stack with iron sheets) for hot pressing. Due to the small unit weight and thin slices of powder flakes, special attention should be paid to the control of weight error and density uniformity. This needs to be considered in terms of powder fluidity, powder conveying, mold structure, pressing principle, pressing parameters, etc.; the density of the powder tablet should not be too high, otherwise it will have an adverse effect on the bonding strength between layers during hot pressing. In the case of falling edges and corners, and easy to take, try to use small pressure to form.
(4) Inspection: The large diamond segment after hot pressing is required to inspect the appearance, size, weight, hardness, and bonding strength of soft and hard layers. The size is in place, the weight loss is small, and the hardness is up to the standard. Finally, the diamond segment needs to be deburred and surface treated.
Contact Us
If you’re interested in Marble Cutting Diamond Segments, please feel free to contact us, (E-mail: [email protected] Phone/WhatsApp: 0086-15805032000 or filling out the form below) we will keep providing quality products and excellent service for you.