Laser Welded Diamond Blades Supplier
Laser Welded Diamond Blades can be supplied by Eonyx, which is the leading manufacturer of diamond saw blades. Our sophisticated factory can supply 20,000 pieces of saw blades per month. As a professional supplier, we can guarantee competitive wholesale price and stable quality.
Sizes of Laser Welded Diamond Blades
The regular diameters of diamond saw blades range from 100mm to 3500mm. Among them, the popular sizes are: 2 inch, 3 inch, 3 3/8 inch, 4 inch, 4 3/8 inch, 4 1/2 inch, 5 inch, 5 3/8 inch, 5 1/2 inch, 6 inch, 6 1/2 inch, 7 inch, 7 1/4 inch, 7 1/2 inch, 8 inch, 8 1/4 inch, 9 inch, 10 inch, 12 inch, 14 inch, 16 inch, 18 inch, 20 inch, 24 inch, 26 inch, 30 inch, 36 inch, etc. (110mm, 160mm, 165mm, 255mm, 300mm, 350mm, 400mm, 3m, etc.)
Saw Blades Processing Process
We have been focusing on the technical development and production of diamond tools for more than 28 years.
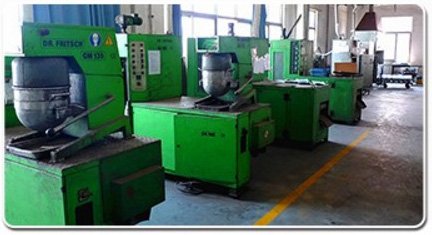
1. Powder Milling
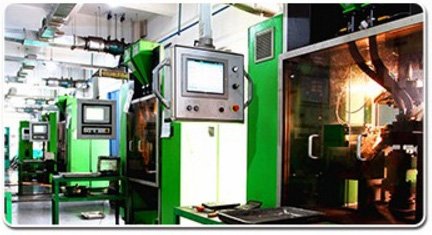
2. Segment Pressing

3. Segment Sintering
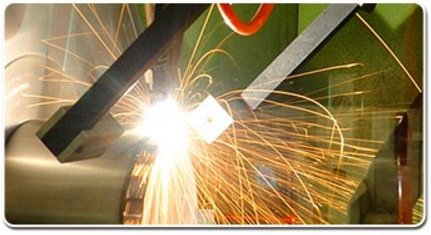
4. Segment Welding
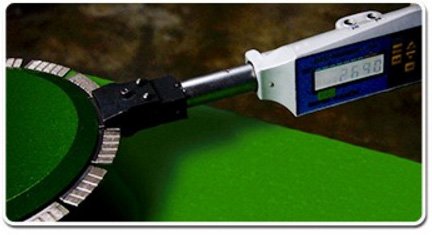
5. Welding Strength Inspection
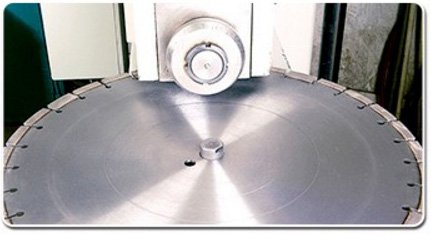
6. Stress Release Rolling
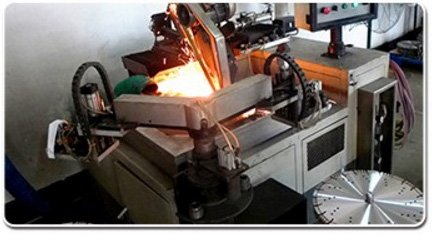
7. Blade Polishing
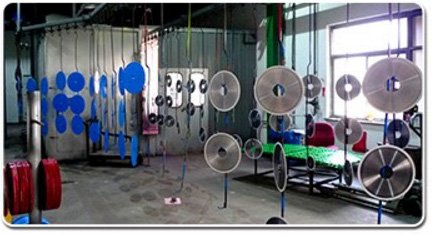
8. Blade Painting
Quality Inspection
Excellent product quality is our commitment to customers as always.
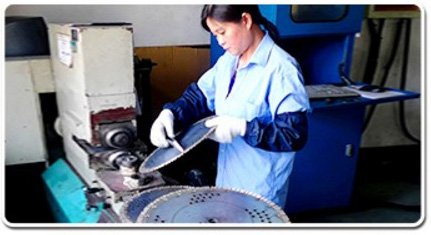
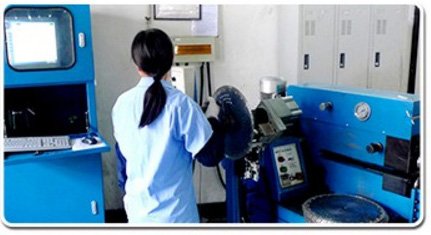
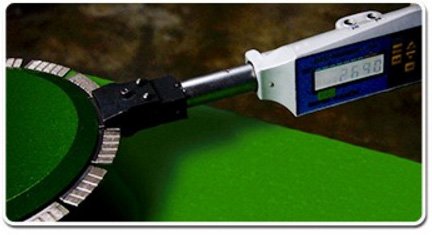
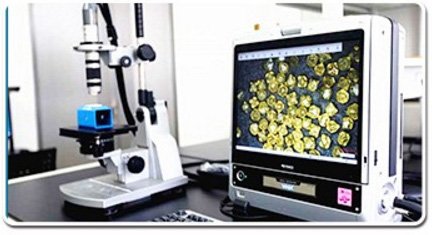
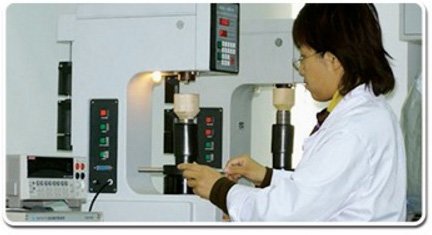
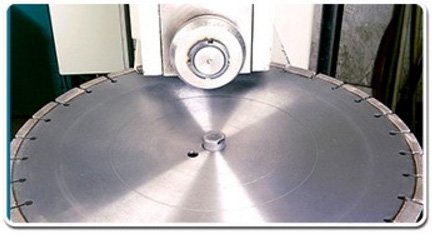
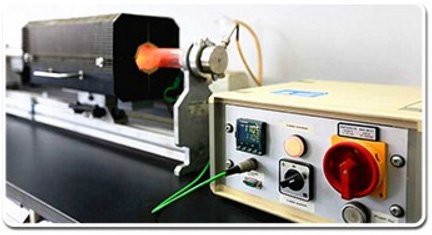
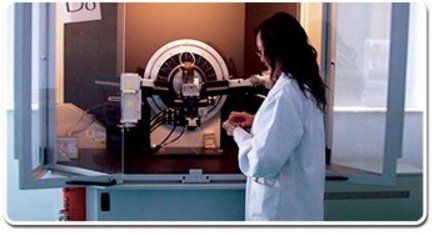
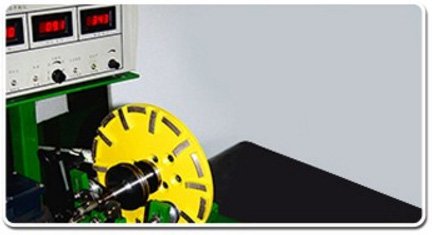
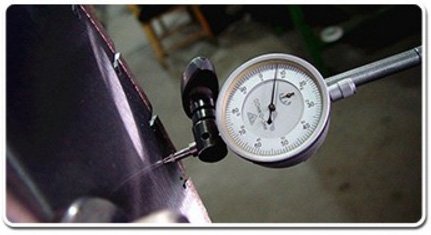
Applications of laser welded diamond saw blades
With the rapid development of highways, airport runways, and construction projects, as well as the increasing maintenance and renovation projects of construction projects, there is an urgent need for safe, reliable and effective dry-cutting diamond saw blades and drill bits for concrete, reinforced concrete, and asphalt pavements. and sawing and dry drilling of concrete walls. The sintered saw blade and high frequency welding saw blade can no longer meet this requirement. Under harsh conditions, under the action of high-speed sawing and impact load, especially when there is no water cooling, dry cutting and dry drilling, the saw blade is easily heated to soften the brazing material, causing the segments to fall off, easily causing safety accidents and casualties.
The laser welding diamond saw blade has the characteristics of large welding penetration, large welding seam aspect ratio, and no welding filler material, so the connection between the segments and the substrate has high bonding strength and reliable welding. The diameter of the laser spot is small, the specific energy is small, the heat affected zone is small, and the welding zone is not easily deformed. When the dry cutting and dry drilling are not cooled enough, the high temperature strength is high, and the saw blade and segments are not easy to produce stress and deformation. Due to the good performance of the laser beam, it can be transmitted over a long distance, and the direction of the laser can be easily changed through the mirror. The laser energy can be transmitted over a long distance, and the energy is highly concentrated, so the welding speed is fast, the thermal action area is small, and the cooling speed is fast. It is easy to realize automation and high efficiency. Production.
In recent years, the application and development of laser-welded diamond saw blades are mainly reflected in the following main aspects: (1) the rapid development of laser-welded diamond saw blades promotes the development of laser welding equipment; (2) the selection of high-quality low-carbon alloy steel to improve The machining accuracy of the matrix ensures the welding quality; (3) The formulation of the laser welding transition layer is developed to ensure the welding strength and quality of the segments; (4) The pre-alloyed powder is actively used and promoted in the matrix; (5) According to the needs of the market and application, improve Structures with developed laser-welded saw blade segments.
Details about laser welded diamond blades
Diamond saw blade welding is to weld some segments sintered together by diamond particles and bonded metal powder on a steel substrate. The welding belongs to the welding of dissimilar metals between different materials and different structures. The key to welding is the level of its bonding strength. The traditional welding methods are sintering welding and brazing. The bonding strength of the welding seam of these two methods (especially at high temperature) is not high enough. During the sawing process, accidents such as segments flying and hurting people are prone to occur, and the safety and reliability of the saw blade are not high. it is good. The laser-welded diamond saw blade uses a focused laser beam as an energy source, and uses the mechanism of penetration welding to melt the transition layer of the segments and the matrix to form a firm weld, even when the saw blade and drill are not cooled by cooling water. , can also ensure high welding strength and ensure the safety of use.
The principle of laser welding
The monochromaticity and coherence of the laser ensure that the laser beam energy can be concentrated to a relatively small point through the focusing mirror. When the energy is large enough, the metal in the heating zone will vaporize, thereby forming a small hole in the liquid molten pool. Call it a keyhole. The beam can enter the inside of the keyhole, and through the heat transfer of the keyhole, a larger welding penetration can be obtained. The keyhole phenomenon occurs at the critical point of material melting and vaporization. The vapor pressure generated by the gaseous metal is high enough to overcome the surface tension of the liquid metal and blow the molten metal around, forming a keyhole or cavity. As the metal vapor escapes, a plasma is formed above the workpiece and inside the keyhole, and the thicker plasma shields the human laser. Due to the multiple reflections of the laser in the keyhole, the keyhole can absorb almost all the laser energy, and then transmit it to the surrounding solid metal through the molten metal through the inner wall by heat conduction. When the substrate and segments move relative to the laser beam, the liquid metal flows behind the small hole and gradually solidifies to form a weld. This welding mechanism is called penetration welding, also known as keyhole welding. It is the most commonly used welding method in laser welding.
Advantages of laser welded diamond blades
Laser welding is suitable for welding between metals of the same or different materials and thicknesses. The laser beam can be very finely focused, the spot energy density is very high, almost all materials can be vaporized, and it has a wide range of applicability; the laser power is controllable, and it is easy to realize automation; the laser beam power density is high, and the weld penetration is large , fast speed and high efficiency; laser welding seam is narrow, heat affected zone is small, workpiece deformation is small, and precision welding can be realized; laser welding seam has uniform structure, small grains, few pores, and few inclusion defects. Corrosion resistance and electromagnetic properties are superior to conventional welding methods.
Inventory and Packaging
Sufficient inventory to ensure delivery and professional packaging to ensure safe transportation. Inner packaging: diamond saw blades are covered by anti-rust paint and plastic, then packed in paper box. Outer packaging is according to the shipping method, if by air, we recommend carton which could reduce weight; if by sea, we recommend crate which is seaworthy. Other packaging is also available upon your request.
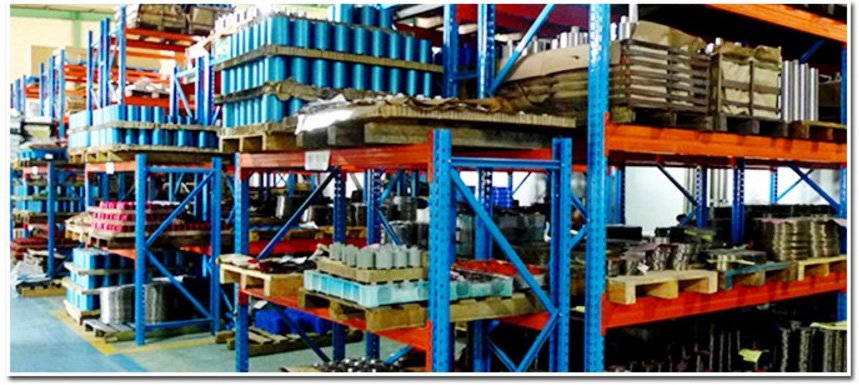
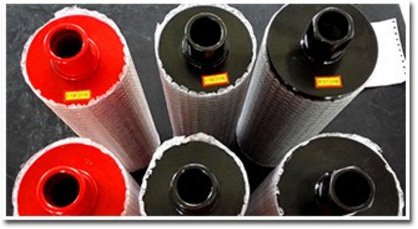
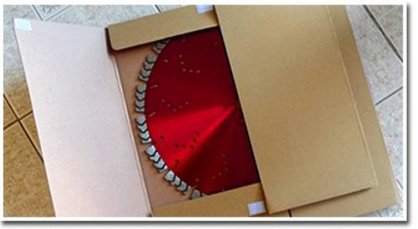
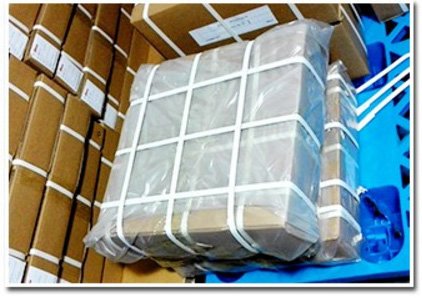
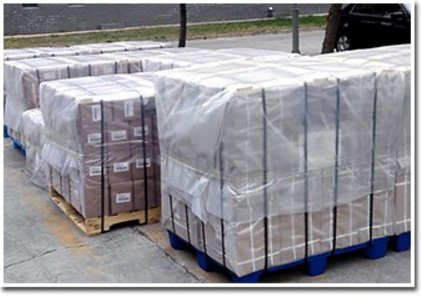
Application of Diamond Cutting Blades
For multi blade cutter, gang saw blade, bridge cutting machine, single arm cutting machine, manual handing machine, able cutting machine, etc. Designed for various hardness stone (soft, medium hard and very hard stones) cutting: granite, marble, sandstone, onyx, limestone, travertine, quartz stone, artificial stone, andesite, volcanic, lava stone, basalt, microcrystal stone, blue stone, dolomite and construction materials (concrete, tile, ceramic, asphalt, floor) to reduce segment cost and increase cutting efficiency.
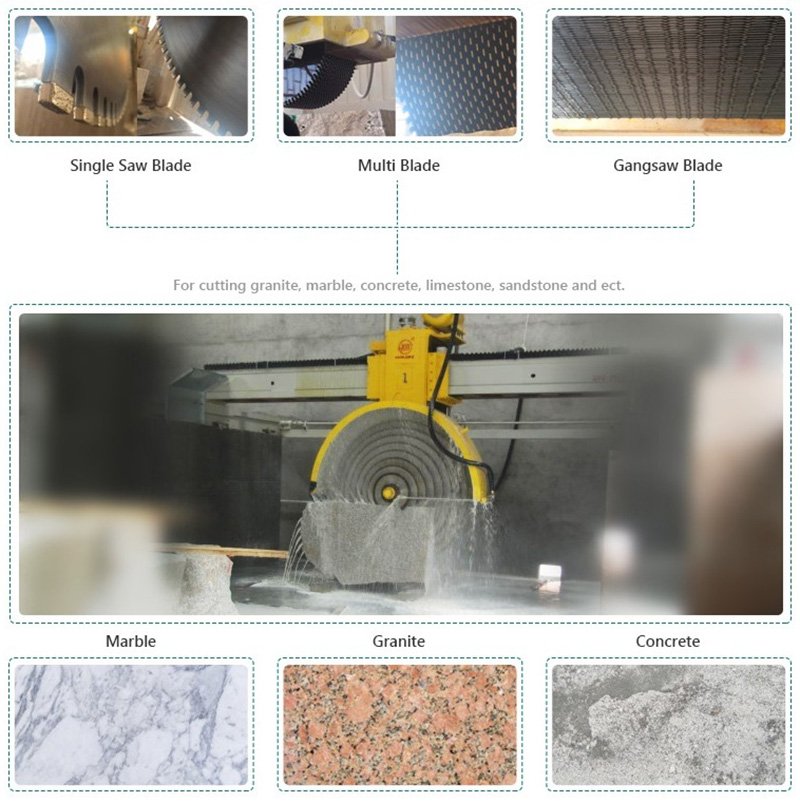
Factors affecting laser welding of diamond saw blades
The laser welding of diamond saw blades belongs to the welding of dissimilar materials with different thicknesses, and there are many factors that affect the welding quality, including substrate material, welding transition layer, laser beam quality, laser power, welding speed, focus position, laser beam offset, laser beam beam incident angle, shielding gas flow, etc.
Blade base material
The use environment of the laser sheet determines that the matrix should be high strength, not easy to deform, and resistant to erosion. At the same time, the cooling rate of laser welding is very fast, and the carbon content of the material becomes a very important factor. If the carbon content is too high, it will affect the embrittlement, microcracks and fatigue strength of the material powder. Therefore, the laser welding matrix generally adopts low carbon steel, and the carbon content w (C) generally does not exceed 0.35%, such as 30CrMo, 28CrMo. If a matrix with a high carbon content is used for welding, such as 65Mn material matrix welding, the laser welding process is equivalent to a heat treatment process, so that a large amount of brittle high-carbon martensite is generated in the high-carbon steel, which is prone to cracks. Increase the toughness of the weld.
Welding transition layer
Since the segments are manufactured by powder metallurgy, the segments that are hot-pressed and sintered with formula powder and diamond are not conducive to laser welding. Direct welding often produces a large number of pores and cracks. Not only the appearance of the weld is unqualified, but its strength cannot meet the requirements at all. . Therefore, in order to ensure the weldability of the segments and the substrate, it is necessary to add a welding transition layer of 1~2mm to the welding part of the segments. According to the requirements of laser welding saw blade performance and production process, the transition layer of laser welding segments must meet the following requirements: sufficiently high welding strength, good appearance quality of weld seam, optimal cold pressing and sintering process matched with the working layer, At the same time, reasonable economic requirements must be taken into account.
The solder transition layer cannot contain low melting point metals, such as tin, because the element is easy to evaporate and vaporize to generate pores. The formulation of the transition layer can be composed of single elements Co, Ni, dual elements FeCo, FeNiCoNi, FeCu, etc., and can also be composed of three components of FeCoNi. Single cobalt powder has good weldability, but due to its high price, a mixture of cobalt powder and other iron powder and nickel powder or pre-alloyed powder is generally used as the transition layer formulation for laser welding. In addition, if the compactness of the segment transition layer after sintering is not enough, it is easy to generate pores during welding and reduce the welding strength. Therefore, the density and compactness of the segments and the hardness of the welded transition layer should be ensured during the manufacturing process of the segments.
Arc of diamond segments
The diamond segments to be welded should be processed by arc grinding to ensure that the radian of the segments matches the radian of the matrix. Generally, there are two ways of grinding the arc with abrasive belt and grinding with grinding wheel. After grinding the segments, the radian must be consistent with the radian of the substrate or its radian can be slightly smaller than the radian of the substrate, and the radian is slightly smaller. There is a small gap between the segments and the substrate. It is convenient for the flow and filling of molten metal during welding, which ensures the welding strength and makes the welding seam more beautiful. However, the gap in the middle should not be too large (generally no more than 01mm), otherwise the beam will leak through the welding interface and the welding effect will not be achieved.
Quality of the laser beam
At present, the lasers used for laser welding diamond saw blades are mainly CO lasers of 1000~5000W. The modes are mostly fundamental mode, quasi-fundamental mode or low-order mode. The evaluation of beam quality is usually characterized by the beam mode. The higher the beam mode and the larger the divergence angle, the worse the beam quality. As far as welding is concerned, beam quality mainly affects weld penetration and shape, with different patterns under the same conditions. Then the welding depth is significantly different; the beam pattern also has an effect on the shape of the weld. In high-order mode welding, the weld is wide and uneven, which is caused by the uneven distribution of beam energy in the high-order mode; in low-order mode welding, the weld is thin and straight and uniform. Therefore, the basic mode or low-order mode should be used to weld the diamond saw blade. If the mode is too high, it is difficult to meet the requirements of welding quality.
In addition, due to the long-term use of the equipment, the quality of the general beam will be degraded, and the laser mode will not be as perfect as when it leaves the factory. Therefore, the welding process needs to be adjusted according to the different states of different equipment during saw blade welding. At the same time, it is necessary to regularly check the quality of the laser beam, and if necessary, check whether the mode of the laser is correct.
Power when welding saw blades
Laser power is the most important factor affecting welding. A certain power corresponds to a certain power density. The greater the power, the greater the welding penetration. During welding, the appropriate welding power should be selected according to the thickness of the segments to be welded and the thickness of the saw blade substrate. When the welding power is insufficient , the effect of penetration welding cannot be achieved, the segments and the matrix cannot be completely melted, and the welding cannot be penetrated. When the welding power is too large, the melting will be too strong, resulting in too strong metal vaporization and volatilization, and pores will be formed in the welding seam, which will affect the welding strength.
Welding speed
In laser deep penetration welding, the welding speed is limited by the pinhole effect. When the laser power is constant, the welding speed determines the welding depth, which in turn affects the welding strength. The welding speed is too fast, on the one hand, the penetration depth is shallow, and on the other hand, the gas in the molten pool cannot escape in time, and there are a large number of pores in the weld, the effective bearing area is reduced, and the welding strength is reduced. The welding speed is too slow, and on the one hand, the transition layer is burned out On the other hand, the heat-affected zone increases, the structure coarsens seriously, which also reduces the joint strength, and when the welding speed is too low, the welding seam will collapse.
Welding saw blade angle
Because the diamond segments are thicker than the substrate of the saw blade, and the segments are not completely dense powder metallurgy materials, in order to avoid the laser beam being blocked by the raised transition layer when the laser beam is vertically shot, the laser must be formed during the welding process. Weld at a certain angle. When the beam is shot at a certain inclination angle, it will increase the spot area on the surface of the workpiece, reduce the power density per unit welding area, thereby reducing the welding penetration depth, but it can increase the welding melting range and increase the metallurgical bonding strength. Generally suitable The welding angle is 3°~15°.
Beam offset of the laser
During welding, the welding offset should be properly adjusted according to the arc grinding of the diamond segments and the quality of the weld during welding. Therefore, the laser beam is required to be deviated to the side of the substrate and maintain a certain offset. Appropriate welding offset can make the appearance and strength of the weld meet the standard, especially can effectively control the generation of pores during the welding process. Generally, the offset of the laser beam is 01~03mm on one side of the substrate. When the laser is too close to the side of the saw blade base, the weld seam is often black, and it can be seen that the saw blade base is welded too much, and the sound during welding is not so crisp, and the light is blue. The strength of the pull teeth can not meet the welding strength requirements, especially in some cases, the welder will tend to be more dry to the substrate in order to achieve a better weld, so sometimes the weld is beautiful, but the actual segment side is not completely melted. For virtual welding. When the laser is too close to the segments, the sparks tend to be relatively large, and it can be seen that the segments are too fused, the appearance quality of the welds is not good, and the strength requirements of the pull teeth are also not met.
Defocus amount
The focal spot size is proportional to the focal length, so the resulting energy density is inversely proportional to the square of the focal length. Higher energy density can be achieved with a short focal length, but the application range is narrow due to the smaller depth of focus, that is, the shorter working depth. In addition, if the spatter is large during welding, it will contaminate the lens with a short focal length.
The focal spot power density of the laser beam is not equal to the spot power density acting on the workpiece, which also depends on the relative position (defocus amount) of the focal spot plane and the workpiece surface, which has a significant impact on the laser welding process. The amount of defocusing seriously affects the welding penetration of diamond saw blades. A large number of research results show that when laser welding diamond saw blades, negative defocusing is generally used, and the daily defocusing amount is about 1/3 of the thickness of the plate, and the maximum penetration depth is obtained at this time. Since the laser welding diamond saw blade belongs to the small hole effect welding mechanism, and the formation of small holes is often accompanied by obvious sound and light characteristics, if no small holes are formed, the welding flame is orange-red or white; if small holes are formed, the welding The flame is blue and accompanied by an explosion sound, so the defocus amount is often determined and adjusted accordingly.
Inert shielding gas
When laser welding diamond saw blades, it is necessary to use inert gas as a protective gas. Its functions are: to avoid oxidation of the weldment; to protect the focusing lens, so that the focusing lens is prevented from being contaminated by metal vapor and sputtering of molten welding slag; blowing away the laser welding process. possible plasma. The inert protective gas involves three issues: the selection of protective gas types, the control of flow rate and the way of blowing. According to the requirements of welding quality and gas cost, argon is generally used. The control of the gas flow is related to the nozzle diameter and the distance between the nozzle and the workpiece. The air flow is too small to protect the weld, and the weld is severely oxidized and brittle; if the air flow is too large, on the one hand, the surrounding air is wrapped into the welding pool, and the weld is still seriously oxidized. The flow will blow over the welding pool, which will destroy the stability of the welding process, poor weld formability, and reduced welding strength. In practice, the method of side blowing argon is often used to blow away the plasma.
Contact Us
If you’re interested in Laser Welded Diamond Blades, please feel free to contact us, (E-mail: [email protected] Phone/WhatsApp: 0086-15805032000 or filling out the form below) we will keep providing quality products and excellent service for you.