Best Diamond Wire Saw for Quarry
For granite and marble quarrying applications, rubber diamond wire saw is recommended. It can protect the wire saw rope very well and increase the strength of wire cable. Rubber possesses excellent characteristic of temperature resistance, and it can be used under situation of water deficient. The strong flexibility of rubber wire saw can also solve the cut-in-one-side problem in the process of stone quarrying.
Best Diamond Wire Saw for Granite Marble Quarry is for sale at competitive price here at Eonyx, and as a professional diamond tool supplier, we can guarantee the production capacity of 60,000 meters of diamond wire saw every month. Our factory can supply various types and sizes of diamond wire saw to meet the different needs of customers.
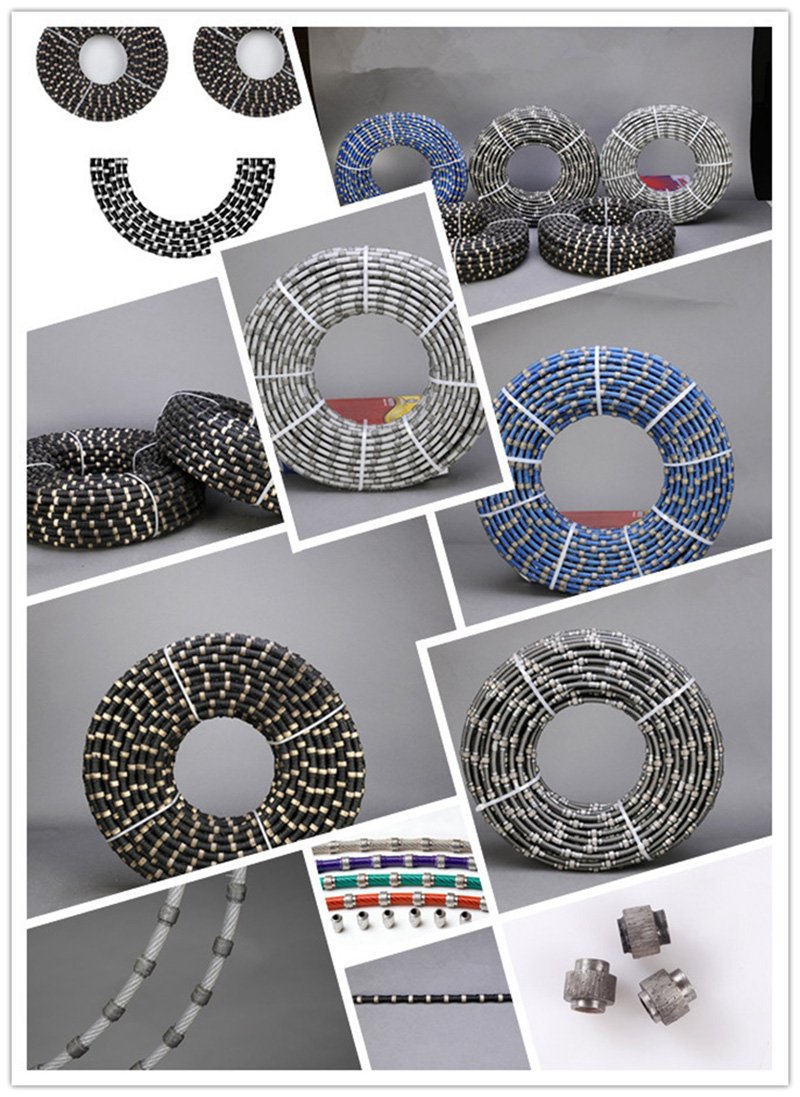
Granite marble quarrying application of diamond wire saw
Diamond wire saws are not only widely used in the quarrying of marble, but also in the separation and cutting of hard rocks such as sandstone and granite. It is not only used for open-pit mining, but also for the mining of narrow underground veins and underground gold mines in South Africa that are at risk of explosion. The main application of diamond wire saw is mining blocks in mines, including all stone mining such as marble and granite. When mining stone with diamond wire saw, it has the advantages of high yield, good processing quality, not easy to damage the blocks, and less pollution during the mining process. It has become an indispensable tool for mining in western economically developed countries. This advanced mining method is increasingly used in many developing countries.
Using the beaded wire saw to mine mines has the advantages of strong adaptability to the mine space and landforms, small slits, fast sawing speed, and large block size, which can completely avoid the waste of resources and noise caused by traditional mining methods such as blasting and flame. , pollution, energy consumption and other shortcomings, to achieve high-efficiency, environmental protection and energy-saving green mining.
Quarry block shaping
More regular stone blocks or slabs have higher value. Because the beaded wire saw has the characteristics of being able to process irregular stones that are difficult to process with conventional tools. Therefore, it is widely used in the plastic processing of stone processing plants. Compared with frame saws and diamond circular saw blades, this technology has higher cutting efficiency and larger cutting area, and has low noise and no vibration. It can also perform curved surface modification and obtain a smooth cutting surface.
The shaping of stone blocks is usually done in mines or processing plants. Large blocks can be shaped with a beaded wire saw. However, considering the performance and processing cost of the beaded wire saw, it is currently mainly used for the shaping of marble mine blocks. For granite blocks, beaded wire saws are less often used for shaping.
Shaped granite and marble cutting
The diamond beaded wire saw used in the processing of special-shaped stone has the characteristics of stable cutting, high efficiency, smooth cutting surface, precise contour of the processing surface, standard size, small slit, and high yield. The diamond wire saw can also process various specifications of stone arcs, special-shaped products, etc. The processing of special-shaped stone by wire saw is one of the CNC stone processing technologies with the highest technical content at present. Although it has only a development history of more than ten years, it has become the main equipment for processing high-value-added special-shaped stone products.
Beads on a diamond wire saw
The main production methods of diamond beads can be divided into two categories according to the manufacturing method: electroplating molding and powder metallurgy sintering molding. And the latter dominates. Brazed diamond beads have also been successfully fabricated by brazing methods, but they have not been used on a large scale yet.
Introduction to sintered beads
The sintered beads can adjust the wear speed of the carcass and the wear speed of the diamond abrasives by adjusting the proportion of the metal components in the carcass or selecting diamond abrasives of different grades, particle sizes and concentrations, so as to produce beads with different cutting heights and spaces. In order to adapt to the cutting of different materials. Sintered diamond beads have high wear resistance and long service life. At the same time, due to their self-sharpening properties, they can always maintain sharp cutting performance. Beads produced by sintering are the mainstream of wire saws and can be used in almost all occasions.
Characteristics of electroplated diamond beads
Compared with hot-pressed sintered beads, the production process of electroplated diamond beads is relatively simple. In the diamond beads formed by electroplating, Co and Ni are used as electroplating materials, and the diamond is plated on the metal substrate to become the working layer. The diamond is completely embedded in the matrix by mechanical means, and the thickness of the coating is usually 70% to 80% of the height of the diamond itself, which is more conducive to the small diameter of the beads. Due to the thin diamond coating and poor wear resistance of the matrix, its coating metal has limited holding force on the diamond abrasive grains, and the diamond abrasive grains are easy to fall off in advance, so the overall performance is not as good as that of sintered beads, which is not suitable for cutting granite. For cutting softer materials such as marble.
Brazed diamond beads
Brazed beading is a new type of beading that is being researched and promoted in recent years. It uses high-temperature brazing technology to achieve chemical metallurgical bonding between gold mesh, solder and matrix. Therefore, the brazing alloy has a good ability to hold the diamond, and at the same time, the diamond has a high abrasive grain height, which can reach 2/3 of the abrasive grain diameter, which greatly improves its sharpness and diamond use efficiency. At present, brazing beads have not yet achieved large-scale engineering applications.
Inventory and Packaging
Sufficient inventory to ensure delivery and professional packaging to ensure safe transportation. Inner packaging: diamond wire saw are covered by plastic, then packed in carton; outer packaging is according to shipping method, if by air, we recommend carton which could reduce weight; if by sea, we recommend crate which is seaworthy. Other packaging is also available upon your request.
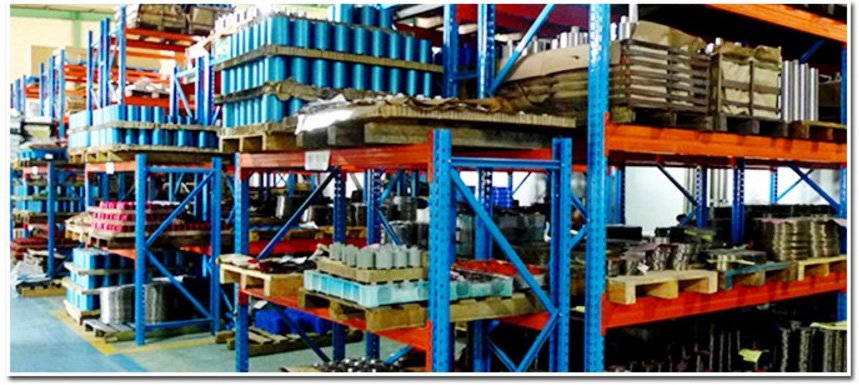
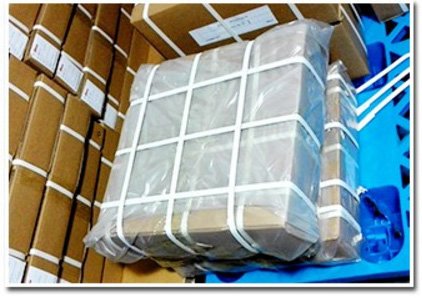
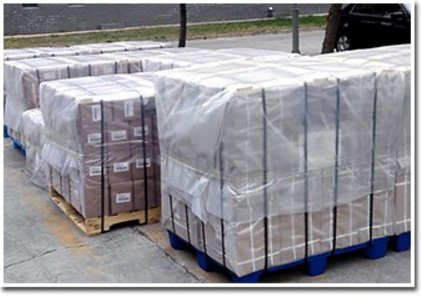
Key points of sintering production of wire saw beads
Sintered diamond beads are manufactured using the principles and methods of powder metallurgy. The most important process in the preparation of beads is the sintering of the matrix powder. Sintering is to crush the powder or powder in an appropriate atmosphere (sometimes under a certain pressure), heat it to a temperature above the melting point of the basic component, and keep it at this temperature for a certain period of time, so that the powder particles are bonded to each other and In the process of improving its performance, the essence of sintering is that the contact between points or surfaces of powder particles gradually becomes crystal bonding, that is, sintering necks are formed through processes such as nucleation and growth. Then the sintering neck grows, the distance between particles shrinks, the gap between particles decreases, or even disappears, the grain grows, the sintered body shrinks significantly, and the density increases, forming a sintered body with a certain strength. Therefore, the quality of sintering is good or bad. , will directly affect the performance of the tool (beads).
Compared with ordinary diamond tool sintering, the sintering of diamond beads is much more difficult. The main problems are:
(1) The beading wall is thin, the size of the mold is also thin, and the hot pressing pressure is high. If the mold material is slightly poor, the mold will be easily broken.
(2) The conductive cross section is small, the heating efficiency is slow, and it is not easy to be uniform.
(3) It is very difficult to remove the mold with an ordinary integral sintering mold. The use of ordinary single-layer molds is difficult to achieve because the height of the mold is too small and the strength of the mold is limited. However, if the mold is increased, the cost of the mold is relatively high.
(4) The aperture deviation has a great influence on the quality of the finished beaded bead. For example, a 9*6mm beaded bead with a diameter larger than 0.1mm will be 0.26mm shorter in the height direction under the same density.
Sintering method of diamond beads
There are three main methods for sintering diamond beads: pressureless sintering, hot pressing sintering, and hot isostatic pressing sintering.
Pressureless sintering of beads
This method can be classified as liquid phase sintering. It is to cold-press the powder into a circular shape and then put it into the steel matrix in its inner hole. In order to form a bond with the steel matrix, thin circular Ring-shaped brazing material is then sintered in a furnace or sintered in an atmosphere or other furnace. In this method, the sintering density is low, the average relative density is only about 95%, and the bonding strength between the carcass and the steel matrix is also low, which cannot meet the needs of cutting hard rocks.
Hot press sintering of beads
Hot-pressing sintering is a process of cold-pressing the loose powder and the steel matrix at one time, putting it into a combined multi-layer floating sintering mold, and sintering it on a vacuum hot-pressing machine. The beads prepared by this method can obtain a high relative density (≥ 98%), the bond strength between the carcass and the steel matrix is good. The hot-pressing sintering process has obvious effects on the relative density, dimensional accuracy, sawing performance and bonding performance of the matrix and the steel matrix of the diamond beads. Bead sintering requires high precision, and its mold design, assembly, pressing and other requirements are also very high. And for beads, due to their small size, assembly and pressing are very difficult, production efficiency is low, and the entire sintering cost is high. Therefore, it is very important to design a suitable hot pressing mold and cooperate with the corresponding sintering process.
Hot isostatic pressing of beads
This method is that the powder can be directly subjected to isostatic pressing after cold pressing and sintered by vacuum hot pressing after cold pressing to a certain density (about 90%), and then hot isostatic pressing sintering. Two methods. Both of these two methods can obtain the ideal density of the beaded carcass, but the investment in hot isostatic pressing equipment is high, the process is complicated and the preparation cost is high.
Contact Us
If you’re interested in Diamond Wire Saw for Granite Marble Quarry, please feel free to contact us, (E-mail: [email protected] Phone/WhatsApp: 0086-15805032000 or filling out the form below) we will keep providing quality products and excellent service for you.