Diamond Wire Rope Saw for Cutting Stone Quartzite Marble
Diamond Wire Saw for Stone Block Trimming and Cutting to Slabs, plastic wire saw is recommended. It can be used to trim and cut marble, granite, quartzite and other stones. It could cut the blocks accurately with small inter-space. As for Diamond Wire Saw for Stone Profiling, plastic diamond wire saw is recommended for stone shaping operations, it could provide a huge range of possibilities. It makes smooth surface and accurate sizes with small inter-space. Stone columns and special shape stone material for building industry can be processed in a much more economical way.
Best Diamond Wire Rope Saw for Cutting Stone Quartzite Marble is for sale at competitive price here at Eonyx, and as a professional diamond tool supplier, we can guarantee the production capacity of 60,000 meters of diamond wire saw every month. Our factory can supply various types and sizes of diamond wire saw to meet the different needs of customers.
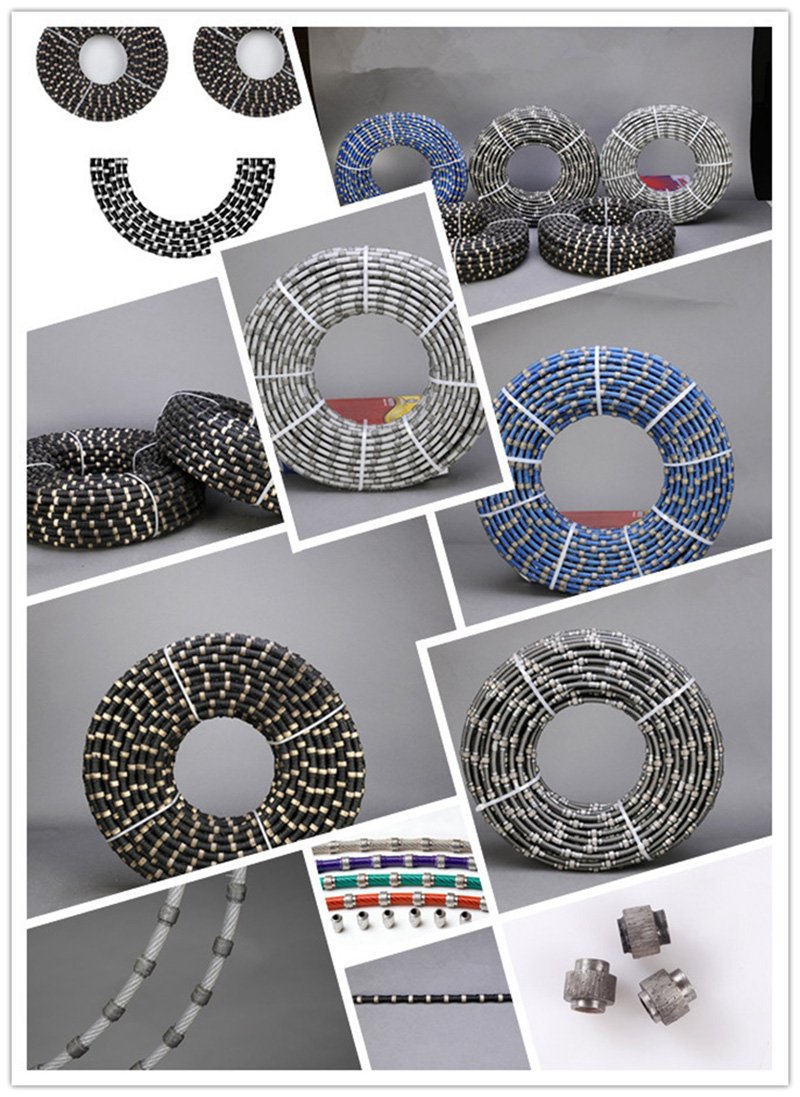
Diamond wire saw for cutting marble
Mining marble electroplating wire saw is 27~33 beads per meter. Because marble is softer, it is mined at a higher rate. The average cutting efficiency is 8~16m/h. With the sintered wire saw, the cutting efficiency is basically stable throughout the process. The life of electroplating beads is generally between 20~30m/h, and the sintered beads can reach 2 times that of electroplating beads. In the process of mining marble, the life of steel wire is not as long as that of beading, and the steel wire needs to be replaced every 7~10m2/m. Marble mine wire saws usually use spring-type beaded ropes. With the reduction of injection molding costs, injection-molded wire saws are also used. Bead types are electroplated and sintered.
Use of diamond wire saws for cutting stone
Wire saw connection
The diamond wire saw must be crimped before installation and use, and the following three points must be paid attention to when connecting:
(1) The diamond wire saw must be pre-wound before crimping the joint, and the winding amount is 15~2 turns per meter.
(2) The joint after crimping should be free of flash and burr, and the joint and the adjacent injection molding layer should be free of gaps.
(3) When installing, note that the working direction of the wire saw must be the same as the direction of the arrow indicated on the surface of the wire saw.
Tension of Quartzite Stone Wire Saw
When the wire saw is working, the wire saw must have a certain tension. The recommended tensioning force of diamond wire saw for special-shaped processing is 2.5~3.5kN. The recommended tension force of diamond wire saw for open quartzite stone blocks with a diameter of 10mm and a diameter of 11mm is 2~3kN (referring to the tension force of the wire rope, and the tension force of the tension wheel is 1 times the tension force of the wire rope). Too low tension will not only cause the wire saw to vibrate and break easily, or reduce the life of the rubber sleeves of the flywheel and guide wheel, but also affect the machining accuracy. If the tension is too high, the wire rope will be stressed too much, and the wire saw will easily break the rope, which will reduce the life of the wire saw.
Fixing of stone blocks
To prevent the wire saw from cutting through the bottom of the block, the stone block should be placed on a home-made cement stand, not the usual wooden block. Blocks are best fixed with quick-drying cement. During the cutting process, the blocks or plates must not be moved, otherwise the wire saw will be stuck or the beads and the injection layer on the wire saw will be squeezed into a ball, which will expose the inner wire rope, aggravate the breakage of the wire rope, and affect the cutting life of the wire saw. and the accuracy of the plate.
Inspection after installation of diamond wire saw
After starting the equipment, check the deflection of the two large flywheels and the guide wheel, and observe the shaking state of the wire saw. The processing and installation accuracy of the flywheel and the guide wheel is insufficient, which is easy to cause fatigue fracture of the wire saw and directly affects the roughness of the surface of the stone plate.
Edge of the new wire saw
For a new wire saw without a blade, because the surface of the stone blocks is often uneven, the wire saw is prone to stress concentration and breakage when cutting. It is recommended to use manual control at the beginning of cutting and reduce the linear speed of the wire saw by about 20%. And the feed amount, until the wire saw completely enters the block, and then switch to automatic control. If conditions permit, it is best to cut softer stones at the beginning of cutting, so as to facilitate the cutting edge of the diamond. Generally speaking, it is recommended when cutting edge: the linear speed of cutting quartzite stone is 20~21m/s; the linear speed of cutting marble is 26~28m/s.
When cutting the edge, adjust the cutting parameters to the normal cutting state until the surface of the beads feels scratched by hand.
Normal cutting with diamond wire saw
(1) Linear speed. The working line speed of the diamond wire saw needs to be adjusted according to the actual situation such as the type of stone and the size of the block. The harder the stone or the wider the block, the lower the line speed. Too high a line speed will cause the wire saw to become dull, and too low will cause the beads to become oval or tapered.
(2) Cooling. When starting to cut, the arrangement of cooling water nozzles should be evenly arranged above the block, and 4 to 6 cooling water nozzles should be arranged according to the size of the block. During normal cutting, the position of the cooling water nozzle should be arranged above the block, the diamond wire saw should enter the side of the block, and 2~3 cooling water nozzles should be arranged according to the width of 1/3~1/2 of the block. The amount of cooling water can be adjusted according to the noise during cutting and the turbidity of the cooling water. It should be pointed out that the amount of cooling water is not the more the better. Excessive cooling water affects the self-sharpening of the wire saw and makes the wire saw slippery. The position of the cooling water nozzle must be fixed to prevent the knitting saw from working without cooling water due to dry vibration or wind blowing it. Working without cooling water will burn the beads and the injection layer, and in severe cases, the entire wire saw will be scrapped.
Inventory and Packaging
Sufficient inventory to ensure delivery and professional packaging to ensure safe transportation. Inner packaging: diamond wire saw are covered by plastic, then packed in carton; outer packaging is according to shipping method, if by air, we recommend carton which could reduce weight; if by sea, we recommend crate which is seaworthy. Other packaging is also available upon your request.
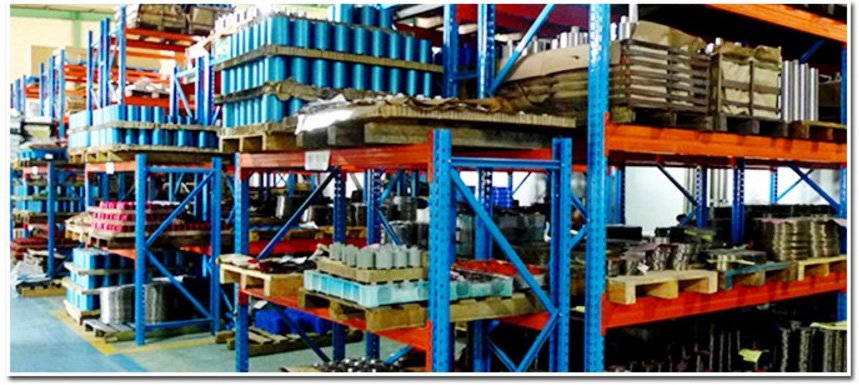
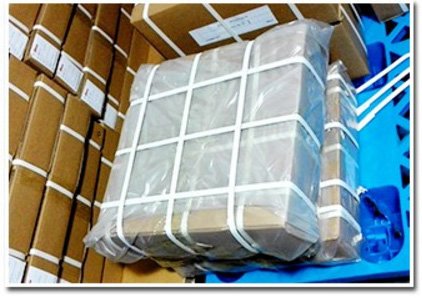
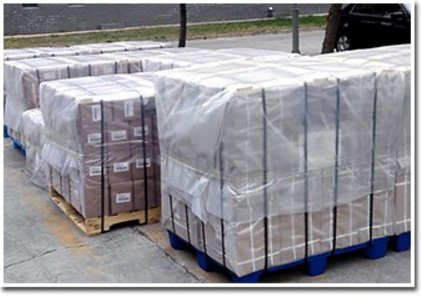
Fixing method of diamond wire saw beads for cutting stone
The diamond wire saw bead fixing technology includes spring fixing method, plastic or rubber injection molding method and spring injection molding method combined with the two.
Spring method
The spring fixing method is adopted, that is, the beads are fixed on the wire rope through springs and washers. The biggest disadvantage of this fixing method is the lack of protection of the wire rope. The coolant directly corrodes the wire, and the rock debris enters the spring or even the beaded matrix, which will directly wear the wire rope, greatly shorten the life of the wire rope, and easily lead to the breakage of the saw wire. . Therefore, the spring fixing method is mostly used to fix the electroplated beads with short life, and it is used in open mines to avoid casualties caused by the rupture of the beaded rope.
Plastic or rubber injection molding
Plastic or rubber injection molding is the most common method of securing beaded rope. After casting, the entire beaded rope is completely covered by plastic or rubber, including the gap between the inner hole of the beaded bead and the wire rope, which is filled with casting material, so that the wire rope is well protected from being corroded by coolant and by cuttings. Abrasion increases the service life of the wire rope. In addition, each bead is cast and connected to the wire rope. Even if the wire rope breaks, the bead is not easy to fly out at a high speed and cause an accident. Therefore, it can be used for indoor processing and demolition of buildings in public places. To match this, most of the beads are sintered beads with longer service life.
Spring injection method
Fix with springs, then cast plastic. This method has better use effect, but the manufacturing process is more complicated and the cost is correspondingly increased.
Fixed structure
Structure of the steel matrix of the wire saw
Under normal circumstances, plastic and steel materials cannot be bonded together. In order to fix the beads and prevent them from producing axial displacement and rotating around the wire rope, the steel base is designed as a mechanical clamping structure. In the design of this clip-inlay structure, in addition to ensuring sufficient clip-inlay strength, the appropriate clearance between the bead and the wire rope must also be considered. In order to ensure the concentricity of the beads and the wire rope during the injection molding process, otherwise the wire saw will be eccentric in use, which will seriously affect the use of the wire saw.
Plastic (rubber) fixing structure
An important role of the plastic (rubber) fixed structure is to contain chips, store water, slow down the impact and protect the wire rope. There are two main types of plastic fixed structural forms: one is a wrapping structure, that is, the exposed substrate is completely wrapped, and the other is a straight structure with the substrate. There are several other forms of wrapped structure, such as platform type, inclined surface type and platform plus inclined surface or groove type (inner diameter positioning). In order to ensure the concentricity of the beads and the wire rope, the outer diameter of the beads is mainly used for the positioning of the outer diameter of the beads in the wrap-type injection molding, and the outer diameter of the base is used for the flat type. The test results of several fixed structure forms show that the wrapped structure has the advantages of good waterproof performance and tighter wrapping, and the inclined surface also has a certain effect of reducing impact, but the two have a greater effect on chip removal space and chip removal. Especially in the later period of use of the wire saw, when the steps are close to the working level, due to the small space for chip removal, the frictional resistance increases, and the cutting efficiency will decrease (about 10%~20%); the straight fixed structure has a structure Simple, accurate positioning, less difficulty in mold processing, relatively large chip removal space, and high efficiency in wire saw cutting, but the waterproof protection of wire rope is significantly lower than that of stepped wrapping and fixing. break, thus affecting the use of the wire saw. Generally speaking, for special-shaped processing, a straight type or a small step-wrapped plastic fixed structure can be used, but in the case of harsh working conditions such as mining, or where the coolant is corrosive to the wire rope, it must be used. Step wrapping, and the wrapping thickness is relatively large.
Wire rope in diamond wire saw for cutting stone
During the use of the wire saw, the wire rope often breaks due to fatigue wear, abrasion, chemical corrosion, etc., especially when the area of the cut stone reaches a certain amount, the wire breakage is more frequent. Broken rope not only affects production, but also brings safety hazards such as throwing beads and hurting people. Therefore, the performance of steel wire ropes is very important for the use of beaded ropes. In addition to the performance of the steel wire itself, the life of the steel wire rope is also related to the pre-tightening tension in the processing process, the minimum curvature of each guide wheel, the axial load of the beads during the processing process, and the impact load. Therefore, the products of professional steel wire rope manufacturers should be selected. And use should refer to the relevant instructions of the wire rope.
Contact Us
If you’re interested in Diamond Wire Rope Saw Stone Quartzite Marble Cutting, please feel free to contact us, (E-mail: [email protected] Phone/WhatsApp: 0086-15805032000 or filling out the form below) we will keep providing quality products and excellent service for you.