Best Diamond Granite Cutting Wire Saw
Best Diamond Granite Cutting Wire Saw is for sale at competitive price here at Eonyx, and as a professional diamond tool supplier, we can guarantee the production capacity of 60,000 meters of diamond wire saw every month. Our factory can supply various types and sizes of diamond wire saw to meet the different needs of customers.
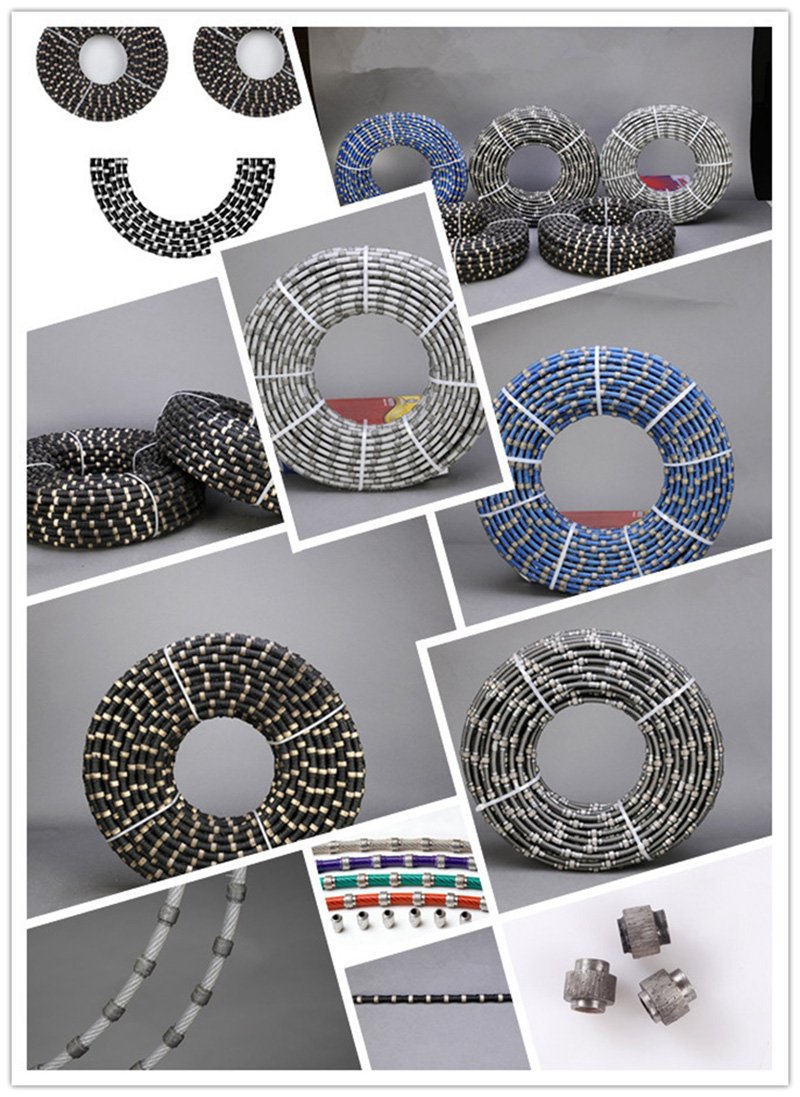
Technical parameters of granite cutting wire saw
The linear speed of the diamond wire saw is adjusted according to the different hardness of the stone type. The linear speed of cutting soft granite is generally 25~30m/s. The linear speed of cutting medium hard granite is generally 22~26m/s. The linear speed of cutting hard granite is generally 20~24m/s. The linear speed of cutting marble is generally 30~35m/s. The linear speed of cutting abrasive rock is generally 30~35m/s. In the initial cutting stage of the new wire saw, its linear speed should be reduced by 2~3m/s compared with the above-mentioned standard, so as to facilitate the diamond edge.
The composition of the granite cutting wire saw
Granite quarrying and block cutting mainly use rubber or plastic wire saws, and the bead type is sintered. This is because the use of rubber or plastic fixation can prevent the quartz and feldspar particles in the cuttings from entering between the beads and the wire rope, causing corrosion and damage to the wire rope. Therefore, rubber or plastic fixed wire saws can be used for cutting hard stones such as granite.
Application of diamond wire saw in granite processing
Granite slab processing
Traditional granite slabs are cut with a sand saw. The process efficiency is low, and the cutting varies greatly depending on the variety of stone. Its circulating water treatment and pollution treatment systems are complex, and the initial investment in equipment is large. The beaded rope saw cutting can effectively solve these problems. At present, there has been a trend in the world to use the beaded rope saw to cut large boards.
The beaded wire saw is not only used to mine blocks, but also can process various specifications of stone arcs, special shapes, cornerstones, etc. , and is equipped with two kinds of microcomputer control and profiling. For a long time, sand saws have been used for sawing granite and other hard stone slabs, resulting in large pollution and low efficiency, and a large amount of waste is generated during sawing. The emergence of multi-wire wire saws has greatly improved the competitiveness of beaded wire saw processing in this field, and has the advantages of high processing efficiency, small footprint, low energy consumption, and less waste. Although the processing cost is about 20% higher than that of sand saws, due to the continuous development of wire saw sawing technology, its cost has been decreasing, and coupled with the advantages of energy saving and environmental protection, it is believed that sand saws will be replaced in the near future, occupying hard The huge application market of stone slab processing.
Processing of shaped and curved stone
Special-shaped curved stone products have shown outstanding value in recent years, the market demand is growing, and its processing technology and equipment have also developed greatly. A CNC special-shaped stone processing machine produced in Italy, the specifications of the largest workpiece can be: Length 2.5mx width 15mx height 15m, equipped with numerical control device, can control 5 degrees of freedom positions, with high cutting speed, low labor requirements, flexible adjustment, automatic tension and other advantages. The special-shaped stone processing machine takes full advantage of the flexibility of wire cutting. Move the tool or work through the x, y and z axes to achieve curve cutting, which can excellently complete many processing processes that cannot be achieved by conventional tools, such as the “hollowing out” of handicrafts, and can also process various curved surfaces, drum-shaped surfaces and stone pillars. decorative material. Different types and specifications of diamond beaded ropes have different application fields. Therefore, it is necessary to select the appropriate diamond beaded rope and determine the processing parameters according to the type of material to be processed, hardness and other factors.
Inventory and Packaging
Sufficient inventory to ensure delivery and professional packaging to ensure safe transportation. Inner packaging: diamond wire saw are covered by plastic, then packed in carton; outer packaging is according to shipping method, if by air, we recommend carton which could reduce weight; if by sea, we recommend crate which is seaworthy. Other packaging is also available upon your request.
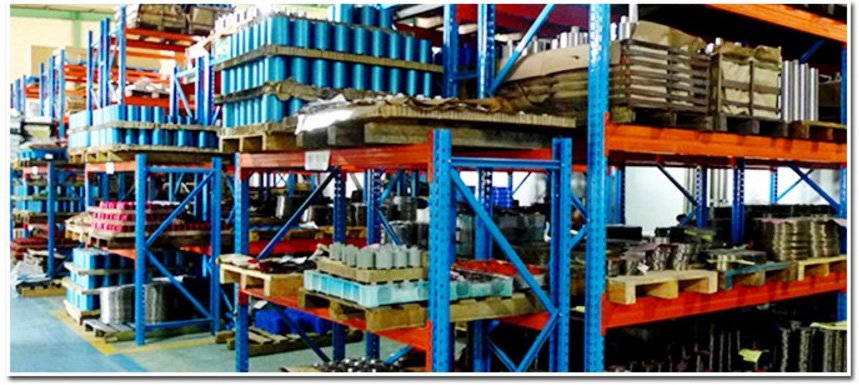
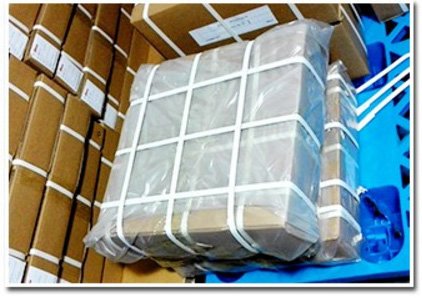
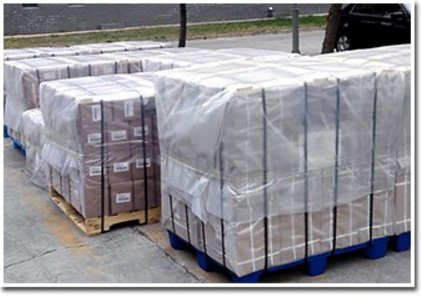
Basic principles of diamond wire sawing
Basic principles of granite wire saw cutting
The basic principle of diamond wire saw processing is shown in the figure. The process of material removal with high-speed moving diamond beads can be regarded as a grinding process. There are three main stages in the point-cutting action of a single diamond grit. At the beginning of the grinding process, the cutting edge of the abrasive particles strikes the workpiece surface, and in the first contact zone, the material deforms elastically. In the contact zone, the friction between the workpiece and the diamond grains increases and the temperature increases. In addition to zone 1, zone 2 also undergoes plastic deformation as the diamond grit cuts further into the material. The next step is the increase of the force. The friction force and deformation energy introduced by the cutting action cause the temperature of the workpiece surface to further increase, and then the elastic limit of the material decreases, the plastic deformation intensifies, and the surface morphology of the material changes significantly, that is, the material is deformed. The main part of the grinding process is in zone 3, the grinding process generates wear debris, and during the formation of the abrasive debris, heat is generated due to shearing. During this time, the plastic displacement of the material occurs simultaneously with the formation of wear debris.
Working process of diamond wire saw
The high-speed movement of diamond beads fixed at equal intervals by plastic (or spring) on the steel wire is used to realize the cutting process of the stone. Taking the processing of special-shaped stone as an example, a diamond wire saw of a certain length (usually 13~25m), after bypassing the main and passive wheels, the two ends are crimped and connected to form a closed loop, and the main and passive wheels installed on both sides of the gantry can be used. Move in the horizontal direction to realize the tension of the wire saw, so that the wire saw can generate a certain pre-tightening force (generally 2~3kN). There is a guide wheel on both sides of the stone to be sawed and above the wire saw to press the wire saw downward, so that the wire saw can apply a certain positive pressure to the stone to be processed when sawing. The high-speed movement of the wire saw is realized by the high-speed rotation of the driving wheel (line speed 20~40m/s). When the main and passive wheels are installed, the planes of the two wheels have a certain dislocation, so that the wire saw can generate a certain rotation when it is in motion, so as to achieve uniform cutting and wear of the beaded circumferential surface.
The process of sawing stone with diamond wire saw is actually a process in which the diamond abrasive particles in the matrix of the gold-stone beaded working layer continuously grind the rock under the action of high-speed movement and positive pressure. During this process, the matrix will produce mechanical wear and thermal Physical and chemical phenomena such as wear and micro-fracture. In the process of grinding rocks, the diamonds will wear and become dull, and some of them will be ground. With the wear of the matrix, some of the diamonds will fall off, and the new diamonds with sharper edges and corners will be exposed and participate in grinding. This cycle is repeated until most of the working layer is consumed and the wire saw loses its working capacity. Here, in addition to supporting and fixing the beads to make them work normally, the plastic fixation also plays the role of water storage (which can cool the working layer) and chip storage due to the equally spaced and concave structure. This is the foundation for the continuous cutting of diamond beads.
Contact Us
If you’re interested in Diamond Granite Cutting Wire Saw, please feel free to contact us, (E-mail: [email protected] Phone/WhatsApp: 0086-15805032000 or filling out the form below) we will keep providing quality products and excellent service for you.