Best Diamond Circular Saw Ceramic Tile Cutting Blades Disc Manufacturer
Best Diamond Circular Saw Ceramic Tile Cutting Blades Disc can be supplied by Eonyx, which is the leading manufacturer of diamond saw blades. Our sophisticated factory can supply 20,000 pieces of saw blades per month. As a professional supplier, we can guarantee competitive wholesale price and stable quality.
Sizes of Diamond Circular Saw Ceramic Tile Cutting Blades Disc
The regular diameters of diamond saw blades range from 100mm to 3500mm. Among them, the popular sizes are: 2 inch, 3 inch, 3 3/8 inch, 4 inch, 4 3/8 inch, 4 1/2 inch, 5 inch, 5 3/8 inch, 5 1/2 inch, 6 inch, 6 1/2 inch, 7 inch, 7 1/4 inch, 7 1/2 inch, 8 inch, 8 1/4 inch, 9 inch, 10 inch, 12 inch, 14 inch, 16 inch, 18 inch, 20 inch, 24 inch, 26 inch, 30 inch, 36 inch, etc. (110mm, 160mm, 165mm, 255mm, 300mm, 350mm, 400mm, 3m, etc.)
Saw Blades Processing Process
We have been focusing on the technical development and production of diamond tools for more than 28 years.
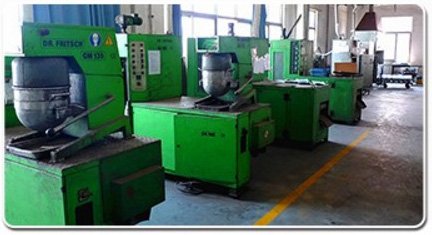
1. Powder Milling
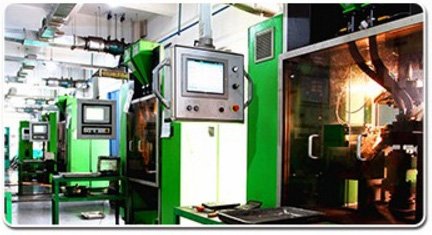
2. Segment Pressing

3. Segment Sintering
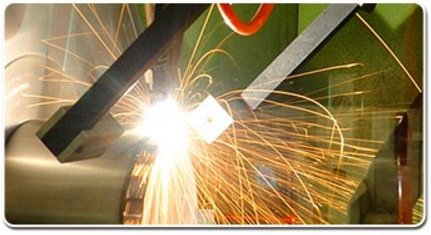
4. Segment Welding
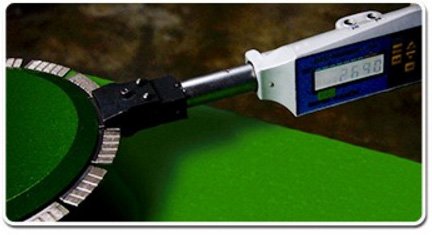
5. Welding Strength Inspection
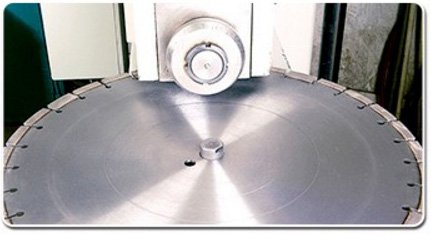
6. Stress Release Rolling
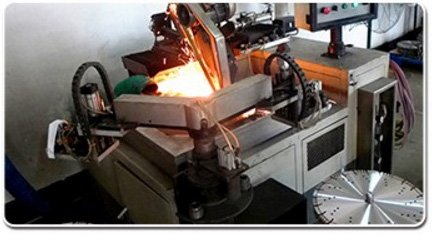
7. Blade Polishing
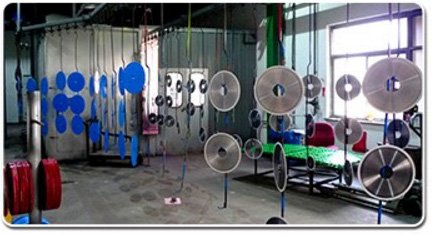
8. Blade Painting
Quality Inspection
Excellent product quality is our commitment to customers as always.
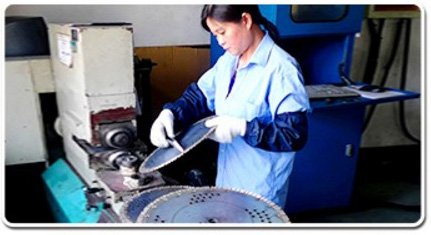
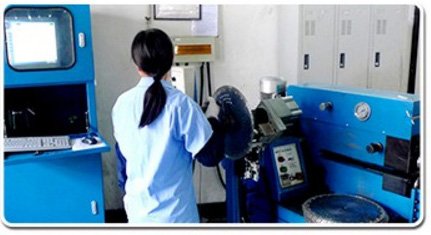
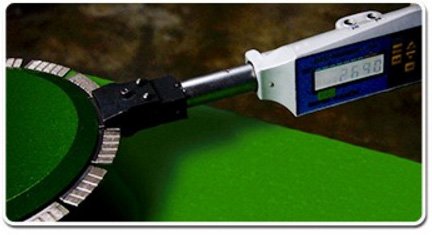
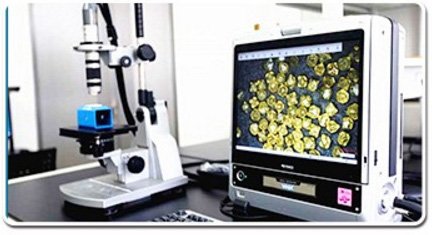
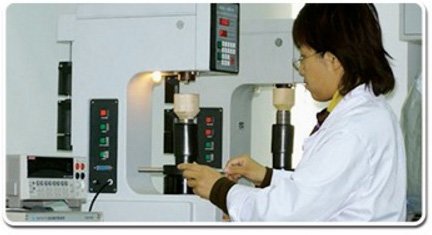
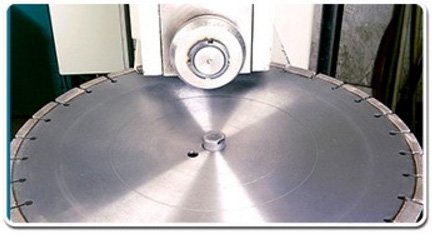
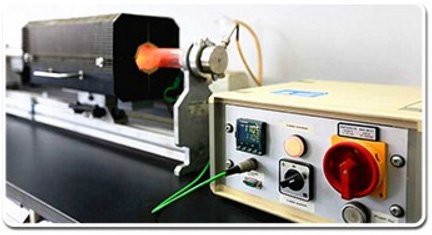
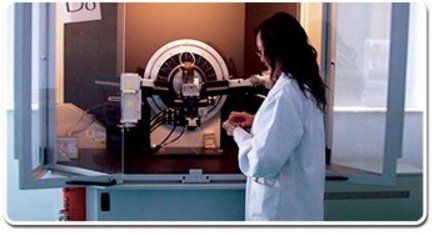
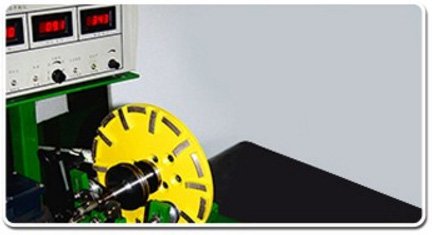
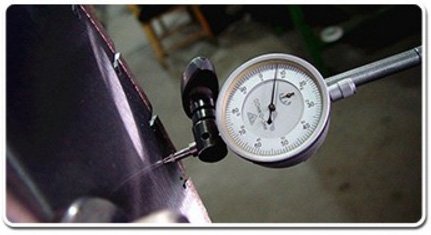
Production process and equipment of diamond circular saw blades for cutting ceramic tiles
The production process of ceramic tile cutting saw blades includes batching, mixing, cold pressing, hot pressing and sintering to finishing. The diamond segments is the main body of the diamond ceramic tile saw blade, and its quality is directly related to the performance of the tool, so the production of the diamond segments is very critical and needs to be controlled. After the powder is prepared in strict accordance with the requirements of the formula, the carcass powder must be uniformly mixed, refined and mechanically meshed through the ball milling process. At present, the most suitable ball milling equipment on the market is a high-energy planetary ball mill, which can achieve good results after 2 hours of ball milling. Do not open the lid immediately after the ball milling, and let it cool to room temperature before discharging to avoid oxidation or accidents. The ball milled powder is generally mixed for 4~6 hours after adding diamond and various additives. These additives include organic substances such as liquid paraffin or acetone, which are convenient for diamond to be dispersed in the powder. Lubricants and binders, and the diamond segmentss that require the weak and brittle carcass are also added with inorganic non-metallic materials such as graphite and silicon carbide. Three-dimensional mixers are generally used for diamond mixtures. During the mixing process, pay attention to the oxidation of the powder. Especially in the hot flash season in the south, it is necessary to use a sealing method during storage and transportation. The oxidation of the powder has a very bad influence on the quality, especially the service life and the welding performance of the diamond segments of the ceramic tile cutting saw blades.
The cold pressing process of the blades for cutting ceramic tiles
The mixed powder can be hot-pressed and sintered after being cold-pressed. The purpose of the cold pressing of the blade segments of the diamond saw blade is mainly to increase the number of single hot pressing, improve the hot pressing efficiency, and save electricity and mold. Because the cold-formed diamond segments die is staggered by the height of the upper and lower indenters to form a hot-pressing die cavity for a single diamond segments, there is no need to use a partition, and the total power-on area of the mold remains unchanged, the number of diamond segmentss per die The sintering time is nearly doubled, while the sintering time is increased by less than 20%, the sintering efficiency is improved, and the mold and power consumption is greatly reduced. The cold pressing of the diamond segments of the ceramic tile saw blade has no significant effect on the final sintering quality of the diamond segments. For the hob diamond segments with strict particle size classification, the addition of the cold pressing process is likely to cause the coarse particles of the fine knife to be mixed.
Powder performance requirements and additives
In order to ensure that the compaction with lower density has a certain strength, there are still certain requirements for the powder compaction performance. Powder morphology, oxide content and powder particle size all affect the compaction properties of the powder. The powder produced by electrolysis or reduction process has irregular shape, and many dendritic or flake particles have good compression performance. On the contrary, the powder produced by atomization has many spherical particles and poor compression performance. The surface oxide content of the powder particles is high, the powder plasticity is poor, and the compaction property is poor. Adding molding agents can improve the compression performance. These molding agents include: (1) zinc stearate, which can reduce the friction between the powder and the inner wall of the mold and the powder, improve the pressure distribution, improve the compactness of the compact, and reduce the cavity wall and pressure during compression. The friction noise of the billet is generally about 0.5%: (2) Liquid paraffin or rubber gasoline solution can form a certain bonding force between the powders and increase the crushing strength.
Cold pressing mold, equipment and process points for ceramic tile cutting saw blades
The inner mold sleeve and the indenter of the diamond segments of the ceramic tile saw blade are made of 40CrMoV or GCr15 alloy steel, and the hardness is required to be 55~60HRC. In order to improve the strength of the mold, a 8~10mm thick No. 45 steel jacket is usually installed, and other components are cushioned. Plates, washers, and ejector rings are also machined from 45-gauge steel. The edging wheel diamond segments mold generally presses 4 pieces per molding, and the hob presses 2 pieces per molding. The transverse cavity is rectangular, and the inner mold sleeve is circular. In order to reduce stress concentration, the mold cavity should be distributed as evenly as possible, and the four corners should be inverted into RO.5 rounded corners. Due to the problem of stress concentration in the four corners of the mold cavity, it is difficult to design the size of the inner mold sleeve through strength calculation. The empirical value obtained after many times is: in the case of adding a jacket, the minimum distance between the top of the corner and the edge of the inner mold is not less than 15~20mm, which can ensure the strength and life of the mold.
The press generally adopts a small frame type press of 100t level, but in order to ensure the pressing efficiency, the type of rapid pressing and lifting is generally used. Considering the cost of pelletizing, most manufacturers still use manual cold pressing. There are also manufacturers who have begun to design automatic cold presses without granulation, and significant progress has been made.
In fact, the cold pressing of the diamond segments of the diamond ceramic tile saw blade is only for forming, and there is no strict requirement for the compactness and strength of the compact, as long as it is crushed without cracking or broken, because the final density and Strength is achieved by subsequent hot pressing. Therefore, in order to save the mold, two-way pressing is adopted, the pressing pressure is generally controlled below 350MPa, and the density is below 65%. The powder in the cavity before pressing should be flattened. In order to avoid the falling indenter from smashing the diamond segments when the mold is ejected, the ejection-type ejection is generally used.
The hot pressing process and equipment of diamond saw blade for cutting ceramic tile
The sintering of almost all ceramic tile leveling and edging tools is done by hot pressing. The biggest advantage of hot pressing sintering is that full densification can be easily achieved. At present, the blade welding type products of ceramic tile saw blades basically use resistance heating hot presses. The heating power of hot presses is generally 60~90kW, and the maximum use is 120kW. The pressure specification is 15~200kN (20tf). Resistance heating hot presses The advantages of the machine are high sintering efficiency, short single sintering cycle, flexible batch size and variety conversion, good process control and stable quality. The disadvantage is that the mold and power consumption are large. The continuous edging wheel or cylindrical wheel with a diameter of less than 300mm generally uses a bell-type hot pressing sintering furnace, the heating power is 50~60kW, the pressure is 500~600kN (50~60tf), and the furnace cavity size is 500mmx600mm. H or N atmosphere can be used. Protect. Zhongwei type pressing furnace has the advantage of atmosphere protection, good sintering performance and mold saving. The disadvantage is that the efficiency is low, the process is not well controlled, the quality stability is poor, the substrate cannot be recycled, and the processing cost is high. Therefore, the production and usage of continuous edging wheels and cylindrical wheels are gradually decreasing. Except for necessary occasions such as dry grinding and trimming wheels of individual varieties, it is difficult to see continuous edging wheels or cylindrical wheels.
Inventory and Packaging
Sufficient inventory to ensure delivery and professional packaging to ensure safe transportation. Inner packaging: diamond saw blades are covered by anti-rust paint and plastic, then packed in paper box. Outer packaging is according to the shipping method, if by air, we recommend carton which could reduce weight; if by sea, we recommend crate which is seaworthy. Other packaging is also available upon your request.
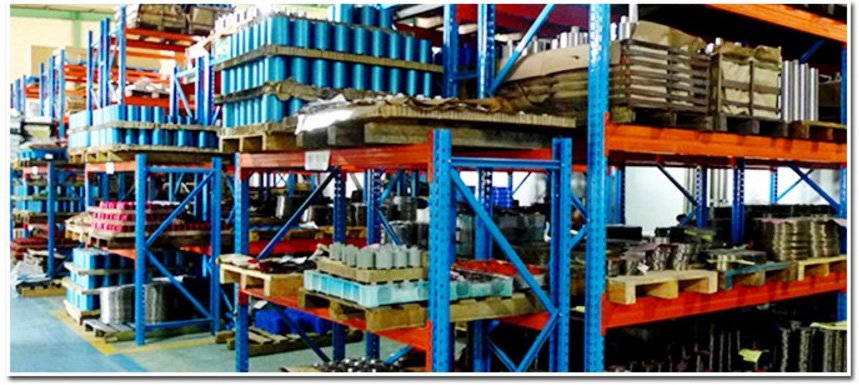
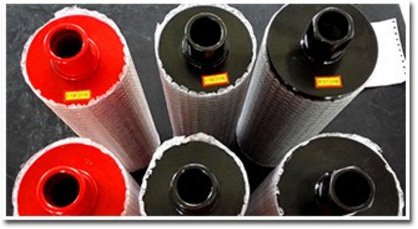
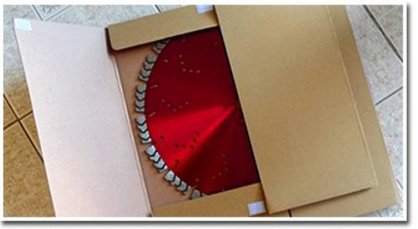
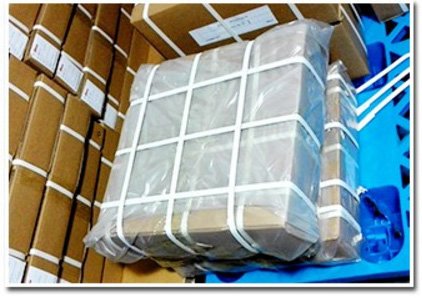
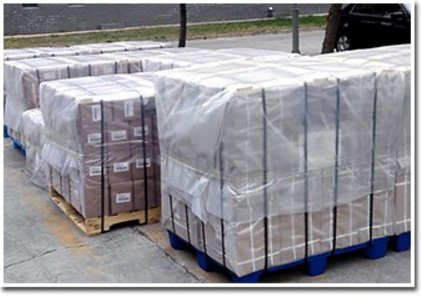
Application of Diamond Cutting Blades
For multi blade cutter, gang saw blade, bridge cutting machine, single arm cutting machine, manual handing machine, able cutting machine, etc. Designed for various hardness stone (soft, medium hard and very hard stones) cutting: granite, marble, sandstone, onyx, limestone, travertine, quartz stone, artificial stone, andesite, volcanic, lava stone, basalt, microcrystal stone, blue stone, dolomite and construction materials (concrete, tile, ceramic, asphalt, floor) to reduce segment cost and increase cutting efficiency.
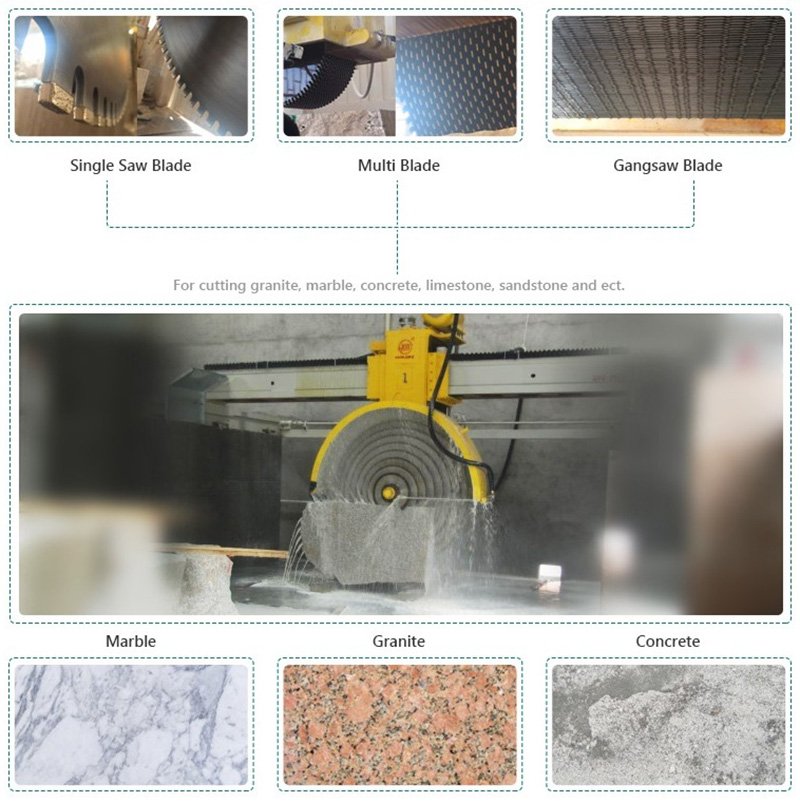
The hot pressing process of the saw blade for cutting ceramic tiles
The sintering of the diamond segments for cutting ceramic tiles generally uses a combined graphite mold. The hot-pressing sintering of the diamond segments is to use the graphite mold itself as an electro-positive element to pass a large current to both ends of the graphite mold, and at the same time press the mold resistance and the resistance of the diamond segments to heat up the hot-pressed powder, which is an internal heat type. . The heating rate is fast, the temperature of each part of the mold cavity is relatively uniform, and the actual temperature in the mold is much higher than the surface temperature of the mold measured by infrared rays, and the difference is initially estimated to be about 100~120℃. Under normal circumstances, there are three main reasons for the scrapping of graphite molds: (1) the carbon powder falls off after the surface is oxidized and the size changes and is scrapped; (2) knocking damage when disassembling the mold; (3) serious adhesion due to the loss of liquid phase of the diamond segments, Damage the indenter or the surface of the partition when removing the diamond segments for cutting ceramic tiles or cleaning metal oxide deposits. In order to avoid man-made damage to the mold, the force when disassembling and assembling the mold should be light, and try not to hit the mold with hard objects. Generally, a rubber hammer is used to hit the indenter. In order to improve the heating efficiency and service life of graphite molds, graphite materials with good degree of graphitization, high resistivity, and high purity, density and strength should be selected. The higher the density, the lower the porosity, the less impurity content, and the better the oxidation resistance; the graphite mold is not dense enough, and the sintered liquid phase is easy to fill the voids, resulting in damage to the mold and the diamond segments adhesion and demoulding; so the graphite density is average It is required to be above 18g/cm. The graphite strength requires that the compressive strength is greater than 30MPa when heated to a temperature of 800~1000℃.
Influence of impurities on ceramic tile cutting saw blades
Since the diamond segmentss of various ceramic tile circular saw blades are relatively strict in distinguishing the diamond particle size, once the coarse particles are doped in the diamond segments, the quality of the diamond saw blade is fatal, especially the fine hob and cylindrical wheel, which often cause The whole polishing line is shut down due to the problem of knife marks. Therefore, special attention should be paid to the cleanliness of the working surface and the storage of materials during the weighing and moulding process of the hot pressing process. Do not work at the same time as other particle sizes.
The sintering temperature is the most important parameter of the hot pressing process. If the sintering temperature is too low, the density and alloying degree of the carcass is insufficient, and the mechanical properties such as hardness and strength are lower than the formula design standards, which will have fatal effects on the quality of the tool. influences. However, if the temperature is too high, the liquid phase will be lost too much, the formula performance will change, and the density will decrease, which will also affect the quality of use. The proper temperature is usually obtained by optimizing the design through experiments, but after many experiments, it has been proved that the lowest temperature when the diamond segments of the diamond saw blade can be pressed to the design size is the optimal sintering temperature. If it is limited pressing, the indenter is just flattened. temperature. The optimum temperature allowable fluctuation range should not be less than ±10°C, and the liquid loss of the diamond segments is 2%~6% within this temperature range. Therefore, to obtain stable carcass performance, on the one hand, process control is very important, and on the other hand, the process stability of the formula is also critical. As far as the current temperature control level of domestic equipment is concerned, the formula that maintains the basic stability of the carcass performance within the fluctuation range of 10~20 °C can ensure the stable quality of mass production and is a formula with process stability.
Recipe for diamond ceramic tile cutting blades
Most of the ceramic tile cutting saw blades use iron-nickel (cobalt)-bronze-based formula, the sintering temperature is 750~860℃, most of the Cu-Sn is in liquid phase in the final temperature holding stage, and all Ni and a small amount of Fe (below 8%) are dissolved in Cu -Sn liquid phase completes alloying very quickly, and liquid phase fills pores rapidly through flow to achieve densification. It belongs to the typical liquid phase hot pressing sintering process, so the sintering process can be completed in a very short time, generally the final temperature holding time is 2~3min. The design of the pressure is based on the liquid content, and the general design pressure is 18~25MPa. After sintering, the pressure relief should not be too fast, otherwise the molten matrix will release the external force in an instant, and the internal stress generated by cooling will cause its shape to change or crack, and the internal stress of the matrix to the diamond will also be reduced. The pressure relief temperature should be 150°C lower than the sintering temperature. In the production process, the pressure relief temperature is often neglected and the quality of the diamond segments is degraded.
Pressing and sintering process of continuous ceramic tile cutting saw blades
Integral sintered ceramic tile saw blades are cold-pressed before hot-pressing. The main purpose of forming is to facilitate hot-pressing, reduce the thickness of the mold, and increase the number of single pressings. The cutter teeth are generally continuous and directly cold-pressed on the substrate. In order to increase the bonding strength between the carcass and the substrate, the joint part between the substrate and the carcass is processed into a groove type. The mold sleeve, core mold and indenter of the cold-pressing mold are made of GCr15, T10 or 9CrSi and other heat treatment hardness of 52~55HRC, and the rest of the mold release sleeve, gasket and pressure pad are made of No. 45 steel, and the press adopts a 300T four-column press.
Hot-pressing sintering is carried out in a bell-type hot-pressing machine, protected by a hydrogen atmosphere. The mold is generally made of stone black mold, and a d300 edging wheel can press about 13 pieces in one furnace. The bell furnace hot press is different from the diamond segments hot press. It is heated by the nickel-chromium resistance wire on the outer wall of the inner cover. Moreover, due to the large sintering volume, the temperature homogenization of the workpiece is completely dependent on thermal radiation, convection and self-heat transfer, so the final temperature holding stage is required to require a temperature equalization process, so the general holding time is about 30~45min. The principle of temperature determination is the same as The hot pressing of diamond saw blades for cutting ceramic tiles is similar, and the pressure is slightly lower than that of ceramic tile saw blades, generally 15~18MPa. The height of the matrix of the qualified sintered diamond circular saw blade should be the same as the design height, the hardness should meet the design requirements, and the percussion matrix is crisp and pleasant, not stuffy.
In fact, the diamond segments of the welded ceramic tile saw blade is made into a fan type, which is spliced in place during welding, which can fully achieve the appearance and use effect of the continuous ceramic tile saw blade. The only advantage of integral sintering is that the sharpness of the formula of the ceramic tile saw blade can reach the highest level, without considering the problem of the decrease in welding strength caused by the weakening of the matrix strength, but the process is cumbersome, the production cycle is long, and the manufacturing cost is high; It is thick and cannot be reused, and the cost of raw materials is high; the process control is difficult and the quality stability is poor. Therefore, unless special occasions or products are required, the monolithic sintering process is generally used to produce ceramic cutting saw blades.
Contact Us
If you’re interested in Best Diamond Circular Saw Ceramic Tile Cutting Blades Disc, please feel free to contact us, (E-mail: [email protected] Phone/WhatsApp: 0086-15805032000 or filling out the form below) we will keep providing quality products and excellent service for you.