Best Diamond Circular Saw Blades for Cutting Natural Stone Suppliers
Best Diamond Circular Saw Blades for Cutting Natural Stone can be supplied by Eonyx, which is the leading manufacturer of diamond saw blades. Our sophisticated factory can supply 20,000 pieces of saw blades per month. As a professional supplier, we can guarantee competitive wholesale price and stable quality.
Sizes of Diamond Circular Saw Blades for Cutting Natural Stone
The regular diameters of diamond saw blades range from 100mm to 3500mm. Among them, the popular sizes are: 2 inch, 3 inch, 3 3/8 inch, 4 inch, 4 3/8 inch, 4 1/2 inch, 5 inch, 5 3/8 inch, 5 1/2 inch, 6 inch, 6 1/2 inch, 7 inch, 7 1/4 inch, 7 1/2 inch, 8 inch, 8 1/4 inch, 9 inch, 10 inch, 12 inch, 14 inch, 16 inch, 18 inch, 20 inch, 24 inch, 26 inch, 30 inch, 36 inch, etc. (110mm, 160mm, 165mm, 255mm, 300mm, 350mm, 400mm, 3m, etc.)
Saw Blades Processing Process
We have been focusing on the technical development and production of diamond tools for more than 28 years.
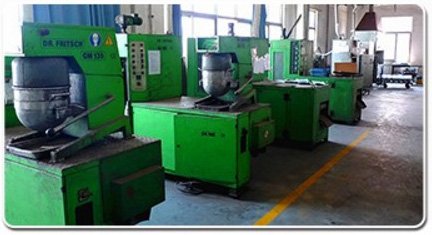
1. Powder Milling
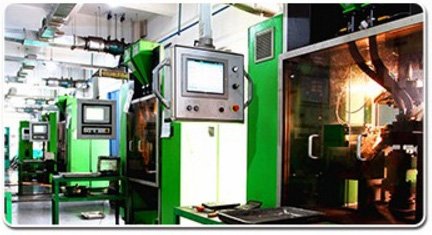
2. Segment Pressing

3. Segment Sintering
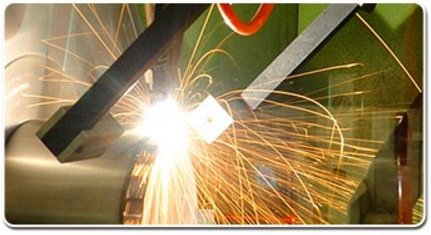
4. Segment Welding
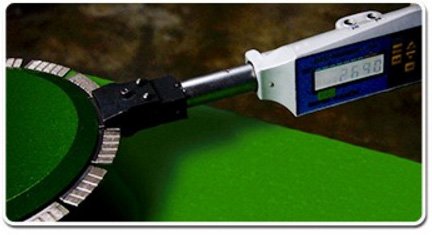
5. Welding Strength Inspection
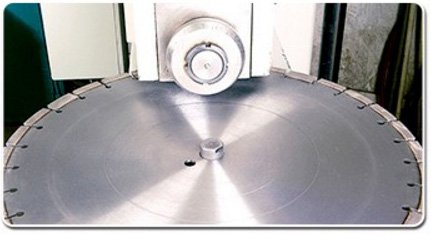
6. Stress Release Rolling
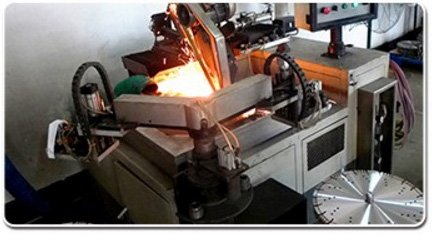
7. Blade Polishing
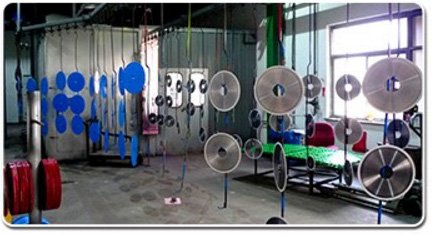
8. Blade Painting
Quality Inspection
Excellent product quality is our commitment to customers as always.
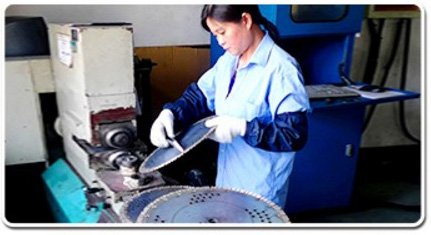
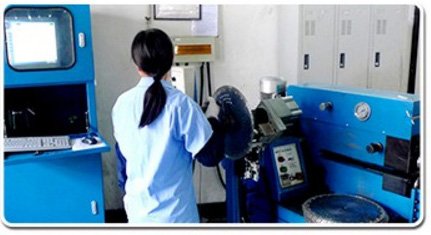
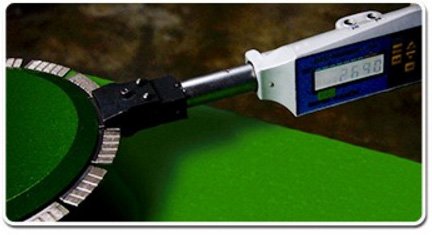
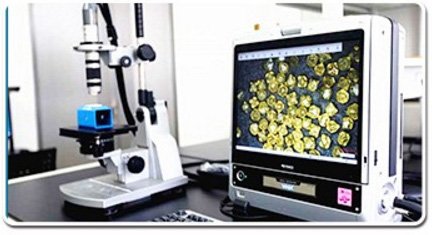
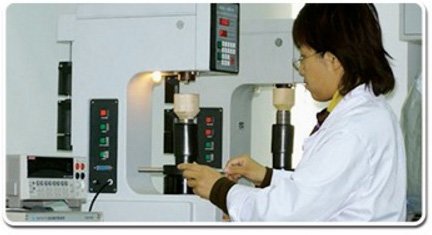
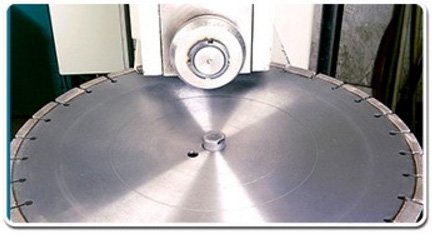
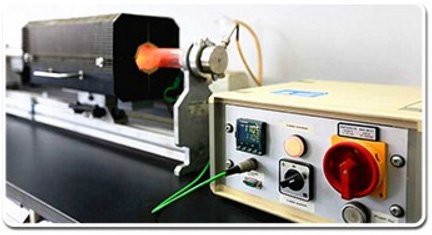
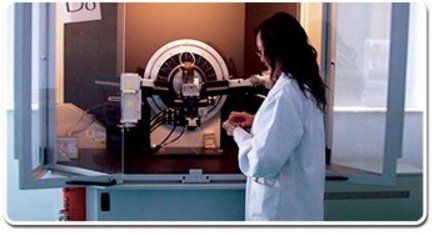
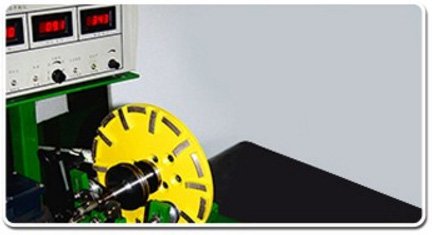
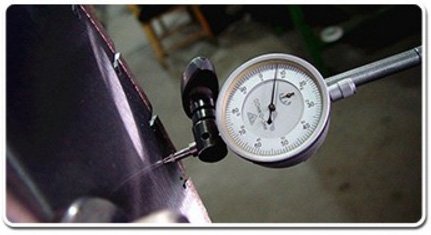
Effect of diamond wear pattern on the performance of saw blade for cutting natural stone
Initial morphology of diamond wear
On the worn surface of the sawtooth, the distribution and orientation of diamond in the matrix are random, because the hardness of diamond is far greater than the hardness of the matrix. In the process of cutting natural stone, the strong friction between the sawtooth and the stone will cause the matrix first Grinding off exposes the new diamond, whose exposed surfaces and edges work as cutting sites. The initial shape is actually the process of new diamonds emerging. Therefore, the percentage of diamond particles in the initial shape to the total number of diamond particles can be used to measure the self-sharpening ability of the tool. The higher the percentage, the more diamonds on the surface of the tool. Strong sharpness. The lower the wear resistance of the diamond-encrusted matrix material, the faster the wear rate of the matrix, and the more diamond particles in the initial form.
Polished (ground) form
In the process of sawing natural stone, the impact of alternating thermal load promotes the continuous graphite transformation on the surface of diamond, and the hardness of its outer layer decreases, even lower than the hardness of the matrix, and the impact of alternating mechanical load makes the graphitized The outer layer is gradually ground off, and the diamond is in a polished and flat state. Due to the dull edges and corners of polished diamonds and the lack of sharp edges, it is difficult to carve into the stone. If the number of diamonds is large, the sharpness of the saw blade will be poor, and the saw blade will show low cutting speed and self-sharpening ability. The higher the wear resistance of the carcass, the lower the wear rate of the carcass, and the more difficult the exposure of new diamonds, resulting in excessive support of the carcass around the diamond particles in the saw blade and low edge height. Under the same processing conditions, The impact force of diamonds decreases, the ratio of micro-broken diamonds decreases, and diamonds in polished form increase, so that the performance of the saw blade will gradually passivate.
Partially broken form
The impact of alternating thermal stress and mechanical stress caused by the periodic severe extrusion and friction between diamond and natural stone causes the diamond to appear fatigue cracks and partially break, revealing many tiny cutting edges. In fact, the local fracture and wear form is the normal working form of the diamond particles. During the process of cutting the stone by the saw blade, the diamond is also gradually worn away, and this local fragmentation makes the diamond constantly change the position and direction of the cutting edge. Maintain the normal cutting ability of the diamond without being blunted or flattened. When the wear performance of the matrix material matches the wear performance of the cutting object, and the matrix has sufficient holding force on the diamond, the height of the diamond’s cutting edge is 1/3~1/2 of the diameter of the diamond. Such a high cutting edge can be carved into The depth of the rock is very large, and the impact force it bears is relatively large, which leads to the increase of diamonds in broken form, that is, the cutting efficiency and self-sharpening ability of the saw blade are improved, and its comprehensive performance is also high.
Diamond large area or overall broken shape
This form is the final wear form caused by the gradual development of local fragmentation. The continuous local wear of the diamond causes its cutting area to decrease continuously, the tail of the matrix is constantly worn off, and its shear resistance is continuously reduced. As the diamond gradually breaks down locally, the overall cutting force on the cutting part will also increase. As a result of the combined action of the two, local fragmentation will develop into large-scale fragmentation. The internal defects of diamond can reduce the shear resistance of diamond. Make the diamond easy to be polished or broken as a whole. There are many diamonds in this wear form, indicating that the diamonds in the saw blade are brittle, have many cracks, and are not fully effective. However, the large area or the overall broken shape is the inevitable result of the normal use of the diamond, and it is also a necessary condition for the saw blade to maintain self-sharpening. Strictly speaking, there is no clear standard for distinguishing the local broken shape of diamond from the large-scale or overall broken shape, and it is not easy to distinguish it during analysis and observation, so it can also be roughly classified into one category.
Diamond exfoliation form
As the matrix material is gradually worn away, the alternating thermal shock softens the matrix material and reduces the holding force on the diamond. At the same time, the large area or overall crushing destroys its crystal structure, making the cutting part passivated as a whole, losing the ability to cut stone, and the cutting force is converted into extrusion force and friction force. When the pressing force and frictional force acting on the diamond surface are greater than the holding force of the matrix, the diamond will fall off. The shedding of diamonds is closely related to the ability of the matrix to be inlaid with diamonds and its wear resistance. The weak inlaid ability or too low wear resistance of the matrix will lead to premature and excessive shedding of diamonds.
It can be seen from this that to improve the performance of the saw blade cutting stone, it is necessary to ensure that the working surface of the saw blade maintains a large number of diamonds in the form of new edges and micro-broken wear, and reduces the diamonds in the form of grinding and polishing. Of course, it is necessary to maintain a high diamond cutting edge height. The cutting height of diamond is affected by many process parameters, such as the bonding strength of the matrix to the diamond, the mechanical properties of the matrix itself (hardness, strength, elastic modulus, etc.), diamond parameters (grain size, grade, concentration, etc.), cutting The influence of process parameters and the properties of the cut stone, etc. Using a diamond circular saw blade with a diameter of 400mm (diamond concentration of 45%) to saw granite under water cooling conditions, the proportional parameters of various diamond wear patterns will also change with different cutting efficiencies. It can be seen that with the increase of cutting efficiency, the shedding and overall broken diamonds increase, and the intact and partially broken diamonds decrease.
Inventory and Packaging
Sufficient inventory to ensure delivery and professional packaging to ensure safe transportation. Inner packaging: diamond saw blades are covered by anti-rust paint and plastic, then packed in paper box. Outer packaging is according to the shipping method, if by air, we recommend carton which could reduce weight; if by sea, we recommend crate which is seaworthy. Other packaging is also available upon your request.
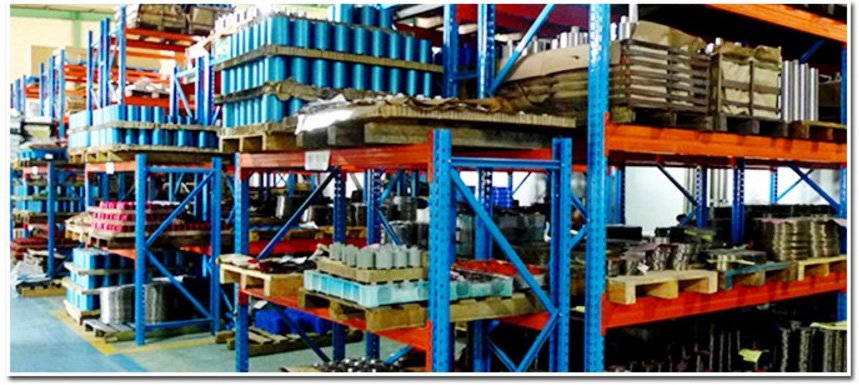
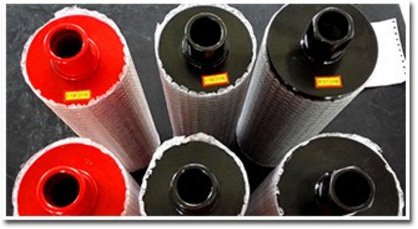
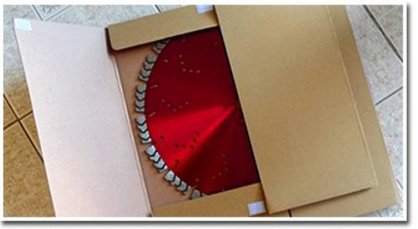
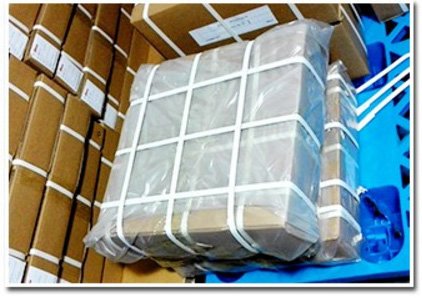
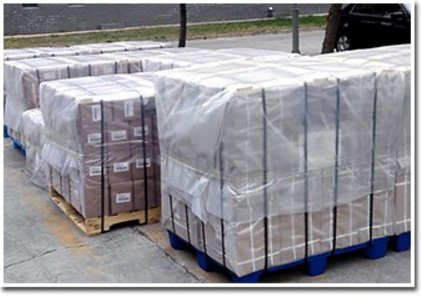
Application of Diamond Cutting Blades
For multi blade cutter, gang saw blade, bridge cutting machine, single arm cutting machine, manual handing machine, able cutting machine, etc. Designed for various hardness stone (soft, medium hard and very hard stones) cutting: granite, marble, sandstone, onyx, limestone, travertine, quartz stone, artificial stone, andesite, volcanic, lava stone, basalt, microcrystal stone, blue stone, dolomite and construction materials (concrete, tile, ceramic, asphalt, floor) to reduce segment cost and increase cutting efficiency.
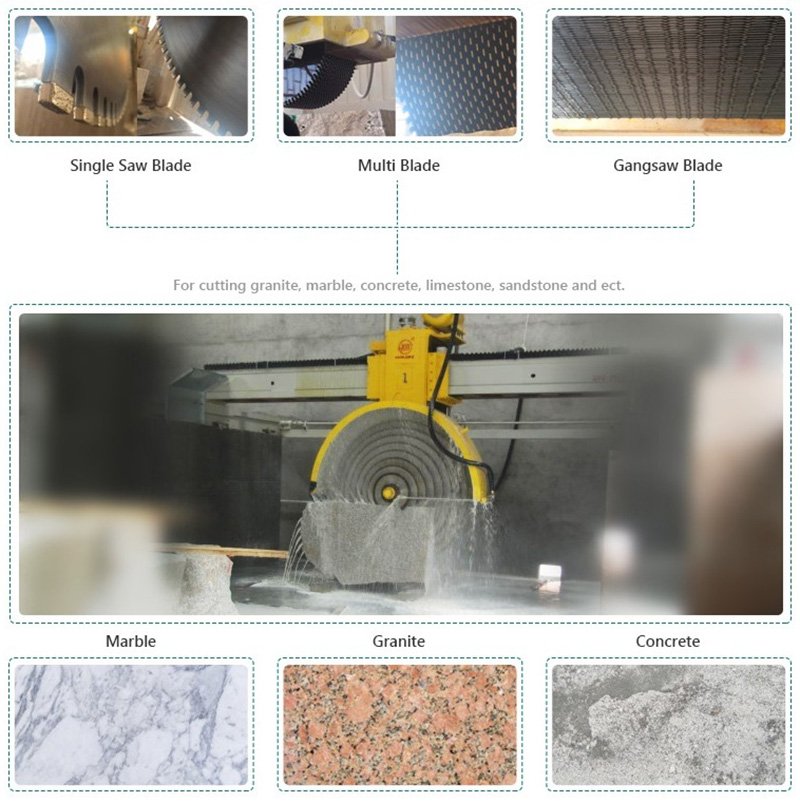
New technology and direction of diamond circular saw blades for cutting natural stone
At present, the development of diamond circular saw blades mainly has the following characteristics: (1) to produce high-efficiency and high-quality stone saw blades, and to develop special diamonds for saw blades; (2) to pay more attention to the research of powder, matrix and sintering process; (3) to pay more attention to Research on sawability and sawing mechanism of stone materials; (4) Development of laser welding saw blades; (5) Development of ultra-large diamond circular saw blades.
With the improvement of market demand, the application of diamond circular saw blades is becoming more and more extensive. The future development direction of diamond circular saw blades is to improve sawing efficiency, saw blade life, reduce production costs, and reduce noise and environmental protection. In order to achieve the above purpose, it is necessary to improve the material, structure and size. First of all, in terms of materials, various manufacturers pay more attention to the research of matrix and matrix formula, and strive to improve the life and efficiency of saw blade cutting stone on the basis of considering economy. Secondly, in terms of structure, the purpose of reducing noise and improving machining accuracy is achieved by changing the structure of the diamond circular saw blade. At present, the research and development of low-noise saw blades generally follow two approaches: one is to change the structure of the substrate, process specific grooves on the substrate, and fill the grooves with Yangni material; the other is to divide the substrate into three layers and combine them. The middle layer adopts damping material. Again, in terms of size, the diameter of diamond circular saw blades for cutting stone is getting larger and larger, and the ratio of thickness to diameter is getting smaller and smaller. The diameter of the largest diamond circular saw blade in the world has reached 5m. The best use effect is achieved by shaping, correcting, stressing, and heat treating the saw blade.
Application of pre-alloyed powder in diamond circular saw blade matrix material
Pre-alloyed powders are fairly uniform in composition because each powder particle contains the various metal elements that make up the alloy. Since the eutectic point is much lower than the melting point of the individual elements in the alloy, the sintering temperature required for the pre-alloyed powder is low. At present, most diamond tools such as diamond saw blades and core drills for stone cutting use a considerable proportion of pre-alloyed powder in the manufacturing process, and the application range of pre-alloyed powder is constantly expanding.
Advantages of using pre-alloyed powders in carcass materials
(1) Greatly improve the performance of diamond saw blades for cutting stone. Because the pre-alloyed powder is more evenly distributed than the mechanically mixed powder. The segregation of components is fundamentally avoided, so that the structure of the carcass is uniform and the performance tends to be consistent; the pre-alloyed powder is fully alloyed, so that the carcass has high hardness and high impact strength, which can greatly improve the compressive and bending strength of sintered products. Improve the holding force of the diamond, increase the sharpness of the diamond saw blade, and prolong the service life of the saw blade.
(2) Significantly reduce the cost of diamond saw blades. Since the pre-alloying greatly reduces the activation energy required for the diffusion of metal atoms during the sintering process, the sintering performance is good, the sintering temperature is low, and the sintering time is shortened. and power consumption. In the case of the same cutting performance, the use of pre-alloyed powder can reduce the diamond concentration by 15% to 20%, significantly reducing the cost of diamond saw blades.
(3) It is convenient for product quality control. Since the composition of each element of the pre-alloyed powder is fixed, the occurrence of various problems in the compounding process is fundamentally avoided, and conditions are provided for the stability of the product quality.
Preparation method and characteristics of pre-alloyed powder for diamond saw blade
At present, the common methods for preparing pre-alloyed powder mainly include the following.
Atomization
The high-pressure atomization method of pre-alloyed powder is to pre-melt the metals of various components into alloys according to the designed carcass ratio before sintering, and then atomize the powder to obtain the carcass powder of the required particle size. The atomization method can be divided into water atomization and gas neutralization according to the atomization medium, and the gas neutralization port uses air, nitrogen or xenon and other gases. The gas-customized cooling rate is fast, the yield of powder grain and fine powder is high, and the cost is low. Water atomization is especially suitable for metals and alloys with higher melting points due to the higher viscosity of water than gas and its strong cooling ability. At present, the pre-alloyed powder of the saw blade for cutting stone is mostly prepared by the atomization method, and the pre-alloyed powder produced by this method has the advantages of low sintering temperature and high degree of alloying. The disadvantage is that the atomization method requires high equipment, it is not easy to adjust the composition of the carcass, and the powder has high oxygen content, high cost, and the powder is nearly spherical, which is not conducive to pressing and granulation.
Coprecipitation
The co-precipitation method is to add a precipitant and a surface modifier to a solution containing two or more metal ions, and by strengthening the process conditions, the various metal ions are precipitated almost simultaneously to obtain a precipitate with uniform composition. The method of finally obtaining the desired powder after the precipitate is processed by thermal decomposition, reduction, crushing, sieving, etc. Studies have shown that iron-based pre-alloyed powder can be prepared by precipitating oxalate mixture and decomposing the precipitate.
Co-precipitation is an important method for preparing composite powders containing two or more metal elements. Since the components of the chemical co-precipitation method can achieve uniform mixing between molecules in the solution in advance, the composition of the product is uniform and stable, and other parameters (such as particle size, particle shape, etc.) are also easy to control. The prepared powder has the advantages of fine particle size, narrow particle size distribution range, uniform composition distribution, high purity and good sintering activity.
Mechanical Alloying
The mechanical alloying method is also called high-energy ball milling, which is to load different metal powders or dispersion-strengthened powders into a high-energy ball mill, and perform long-term ball milling in a protective atmosphere according to a certain ratio of balls to material and ball size. Under the action of mechanical driving force, the powder undergoes repeated extrusion, cold welding and pulverization processes, so that different raw material powders can be tightly combined at the atomic level. If the raw materials contain hard particles such as metals or ceramics that are immiscible in solid state, The hard particles are uniformly dispersed in the softer metal particles to produce a composite powder.
A remarkable feature of the mechanical alloying method is that it can synthesize materials that usually require high temperature processing at low temperature, and can obtain materials such as amorphous alloys and supersaturated solid solutions that are difficult to obtain by conventional methods. However, the mechanical alloying method is easy to bring impurities into the powder during the ball milling process, which reduces the purity of the product, and the repeated extrusion causes a large internal stress inside the powder, which affects the compaction and sintering properties of the powder.
There are many other pre-alloyed powder preparation methods, such as vapor evaporation method, ultrasonic chemical method, amorphous crystallization method, microemulsion method, etc. With the deepening of research, new preparation methods are constantly emerging, but as an industrial preparation method for the purpose of application, it is not yet mature.
Contact Us
If you’re interested in Best Diamond Circular Saw Blades for Cutting Natural Stone, please feel free to contact us, (E-mail: [email protected] Phone/WhatsApp: 0086-15805032000 or filling out the form below) we will keep providing quality products and excellent service for you.