Best Wet Cutting Diamond Saw Blade for Marble Porcelain Ceramic Tile
Best Wet Cutting Diamond Saw Blade for Marble Porcelain Ceramic Tile can be supplied by Eonyx, which is the leading manufacturer of diamond saw blades. Our sophisticated factory can supply 20,000 pieces of saw blades per month. As a professional supplier, we can guarantee competitive wholesale price and stable quality.
Sizes of Wet Cutting Diamond Saw Blade for Marble Porcelain Ceramic Tile
The regular diameters of diamond saw blades range from 100mm to 3500mm. Among them, the popular sizes are: 2 inch, 3 inch, 3 3/8 inch, 4 inch, 4 3/8 inch, 4 1/2 inch, 5 inch, 5 3/8 inch, 5 1/2 inch, 6 inch, 6 1/2 inch, 7 inch, 7 1/4 inch, 7 1/2 inch, 8 inch, 8 1/4 inch, 9 inch, 10 inch, 12 inch, 14 inch, 16 inch, 18 inch, 20 inch, 24 inch, 26 inch, 30 inch, 36 inch, etc. (110mm, 160mm, 165mm, 255mm, 300mm, 350mm, 400mm, 3m, etc.)
Saw Blades Processing Process
We have been focusing on the technical development and production of diamond tools for more than 28 years.
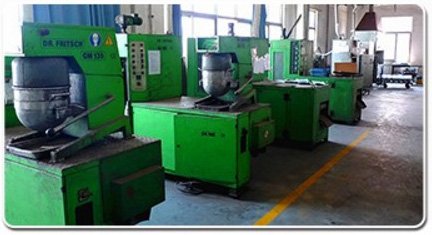
1. Powder Milling
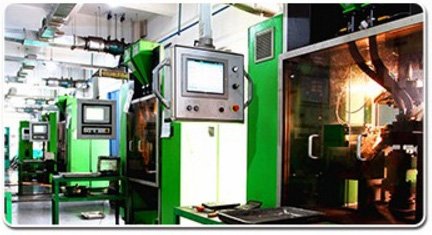
2. Segment Pressing

3. Segment Sintering
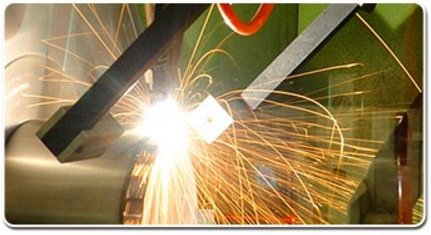
4. Segment Welding
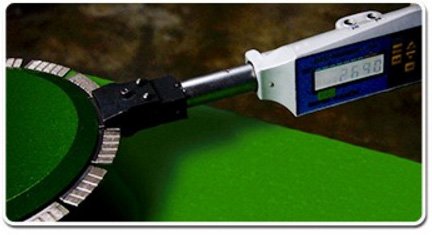
5. Welding Strength Inspection
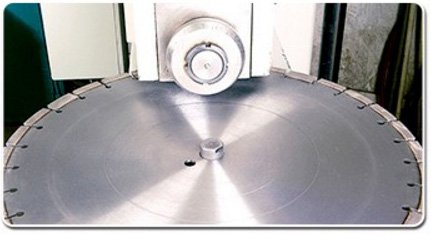
6. Stress Release Rolling
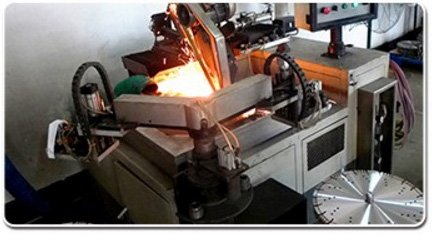
7. Blade Polishing
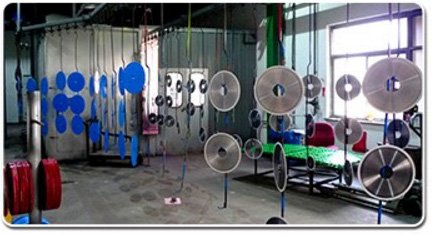
8. Blade Painting
Quality Inspection
Excellent product quality is our commitment to customers as always.
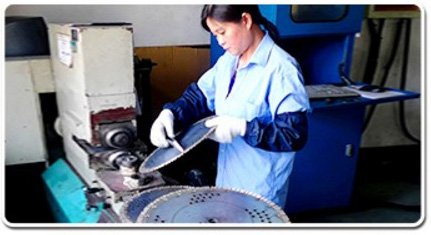
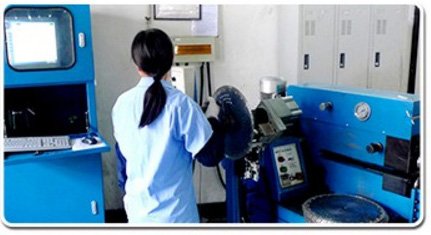
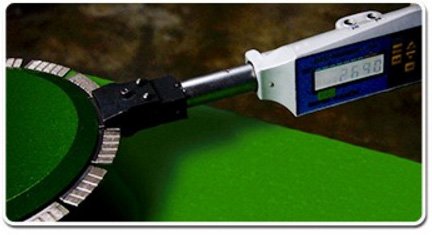
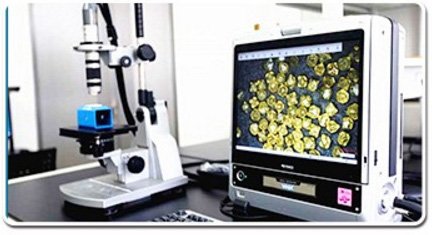
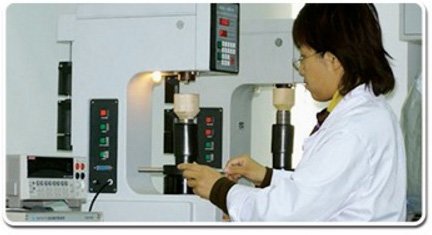
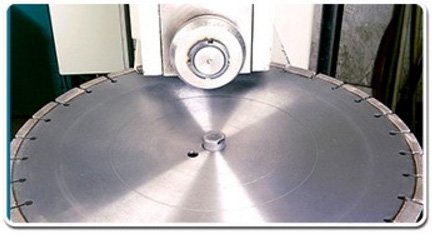
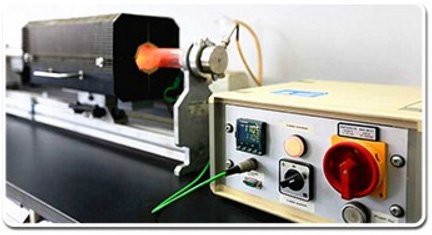
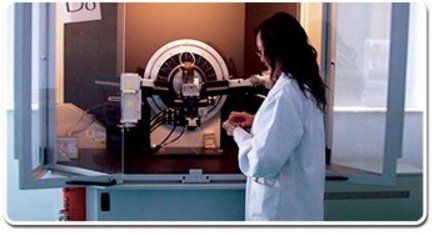
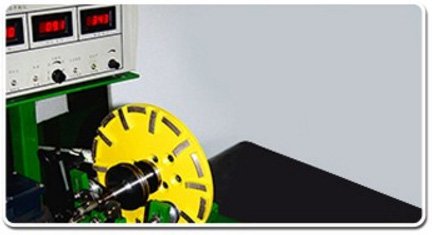
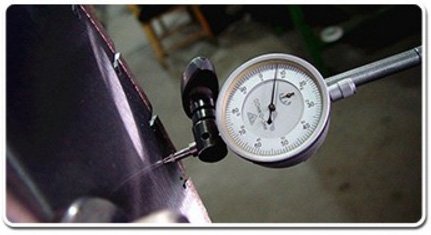
Factors affecting the use of wet cutting diamond saw blades
Factors affecting the efficiency and life of wet cutting diamond circular saw blades include sawing process parameters, diamond segment parameters and marble tile parameters. The parameters of diamond segments include diamond size, diamond concentration and bond hardness. The sawing process parameters include the linear speed of the saw blade, the cutting depth and the feed speed. porcelain tile parameters include marble tile hardness, structure, composition, etc.
Cutting parameters for diamond blades
(1) The linear speed of the saw blade. In practical work, the linear speed of the wet cutting diamond circular saw blade is limited by the equipment conditions, the quality of the saw blade and the nature of the marble tile being sawed. From the perspective of the best saw blade service life and sawing efficiency, the linear speed of the saw blade should be selected according to the properties of different ceramic tiles. When sawing granite, the linear speed of the saw blade can be selected within the range of 25~35m/s. For granite with high quartz content that is difficult to saw, the lower limit of the linear speed of the saw blade is appropriate. When producing granite tiles, the diameter of the wet cutting diamond circular saw blade used is small, and the linear speed can reach 35m/s.
(2) sawing depth. The sawing depth is an important parameter involving diamond wear, effective sawing, force on the saw blade and the properties of the sawed porcelain tile. Generally speaking, when the linear speed of the wet cutting diamond circular saw blade is high, a small cutting depth should be selected. From the current technology, the cutting depth of diamond can be selected between 1~10mm. Generally, when cutting marble blocks with large diameter saw blades, the cutting depth can be controlled between 1 and 2 mm, and the feed speed should be reduced at the same time. When the linear speed of the wet cutting diamond circular saw blade is large, a large depth of cut should be selected. However, when the performance of the saw machine and the strength of the tool allow, the cutting concentration should be taken as large as possible to improve the cutting efficiency. When there is a requirement for processing porcelain tile, small depth cutting should be used.
(3) Feeding speed. The feed speed is the feed speed of the sawed ceramic tile. Its size affects the cutting rate, the force on the saw blade, and the heat dissipation in the sawing area. Its value should be selected according to the nature of the sawed marble tile. Generally speaking, when sawing soft marble tile, such as porcelain tile, the feed speed can be appropriately increased. If the feed speed is too low, it is more conducive to improve the sawing rate. When sawing fine-grained and relatively homogeneous granite, the feed speed can be appropriately increased. If the feed speed is too low, the diamond blade will be easily flattened. However, when sawing granite with a coarse-grained structure and uneven hardness and softness, the feed speed should be reduced, otherwise it will cause the saw blade to vibrate and cause the diamond to break and reduce the sawing rate. The feed speed of sawing granite is generally selected in the range of 9~12m/min.
Segments parameters for wet cutting diamond saw blades
(1) Diamond particle size. The commonly used diamond particle size is in the range of 30/35~60/80 mesh. The harder the ceramic tile is, the finer the particle size should be. Because under the same pressure conditions, the finer the diamond, the sharper it is, which is conducive to cutting into hard marble tile. In addition, generally large-diameter saw blades require high sawing efficiency, and a coarser particle size, such as 30/4040/50 mesh, should be selected; small-diameter saw blades have low sawing efficiency and require smooth porcelain tile sawing sections. Finer particle size, such as 50/6060/80 mesh.
(2) segment concentration. The so-called diamond concentration refers to the density of diamonds distributed in the working layer matrix (ie the weight of diamonds contained in a unit area). The “norm” states that the concentration of 44 carats of diamond per cubic centimeter of working matrix is 100%, and that of 3.3 carats of diamond is 75%. The volume concentration indicates how much the diamond occupies in the segment, and stipulates that the concentration is 100% when the volume of diamond accounts for 1/4 of the total volume. Increasing the diamond concentration is expected to prolong the life of the saw blade because increasing the concentration reduces the average cutting force per diamond. However, increasing the depth will inevitably increase the cost of the saw blade, so there is a most economical concentration, and the concentration increases with the increase of the sawing rate.
(3) The hardness of the segment binder. Generally speaking, the higher the hardness of the bond, the stronger its wear resistance. Therefore, when sawing ceramic tile with high abrasiveness, the hardness of the binder should be high; when sawing marble tile with soft material, the hardness of the binder should be low; when sawing porcelain tile with high abrasiveness and hardness, the hardness of the binder should be moderate. .
Characteristics of the marble tile being sawn
The higher the hardness of the marble tile, the greater the cutting force experienced by the wet cutting diamond saw blade when cutting. The higher the surface temperature of the wet cutting diamond saw blade, the more serious the wear of the diamond segments.
Inventory and Packaging
Sufficient inventory to ensure delivery and professional packaging to ensure safe transportation. Inner packaging: diamond saw blades are covered by anti-rust paint and plastic, then packed in paper box. Outer packaging is according to the shipping method, if by air, we recommend carton which could reduce weight; if by sea, we recommend crate which is seaworthy. Other packaging is also available upon your request.
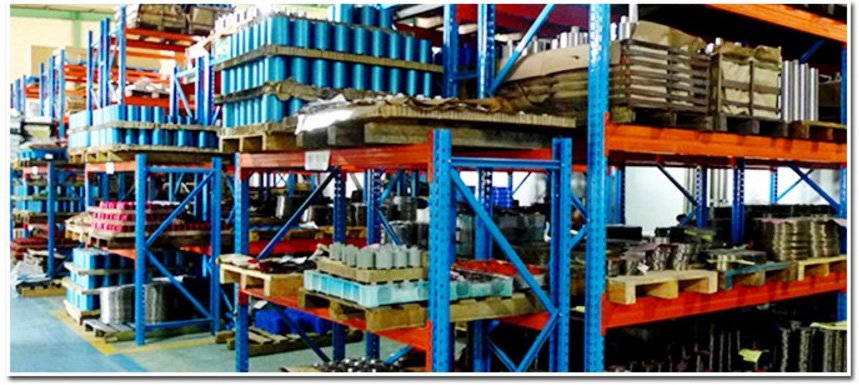
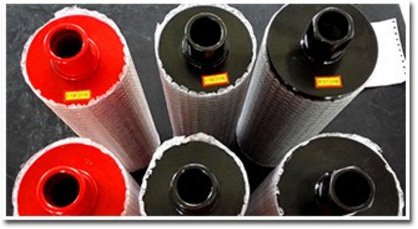
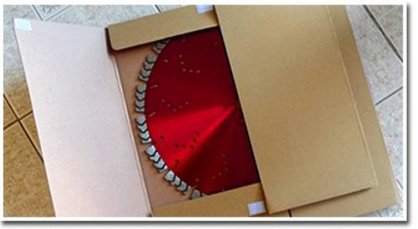
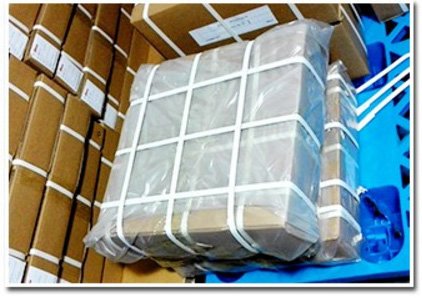
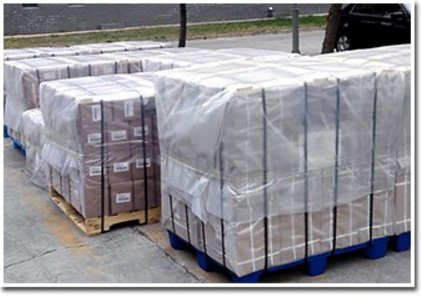
Application of Diamond Cutting Blades
For multi blade cutter, gang saw blade, bridge cutting machine, single arm cutting machine, manual handing machine, able cutting machine, etc. Designed for various hardness stone (soft, medium hard and very hard stones) cutting: granite, marble, sandstone, onyx, limestone, travertine, quartz stone, artificial stone, andesite, volcanic, lava stone, basalt, microcrystal stone, blue stone, dolomite and construction materials (concrete, tile, ceramic, asphalt, floor) to reduce segment cost and increase cutting efficiency.
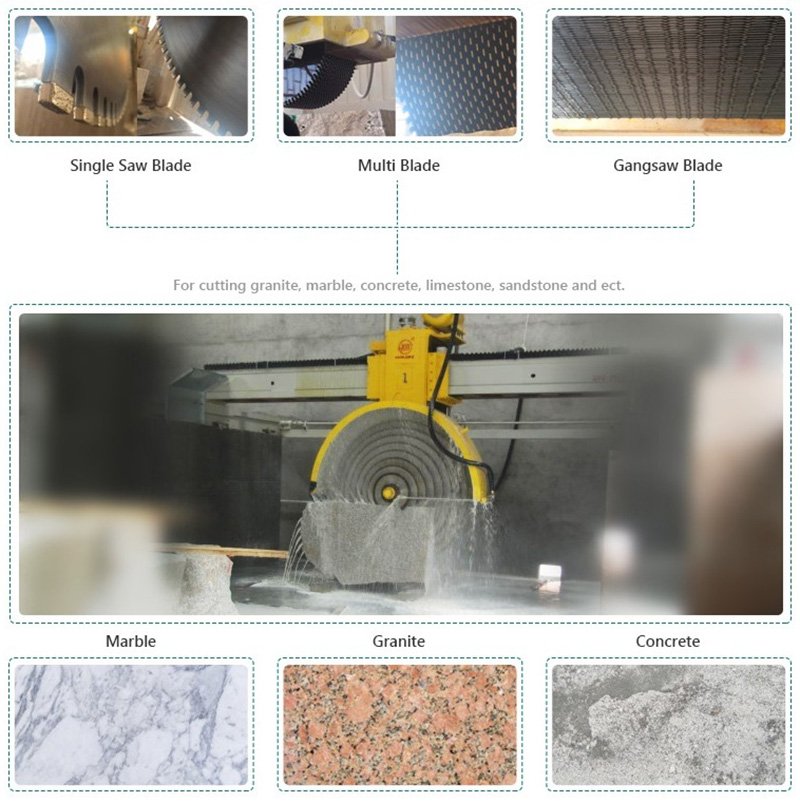
Force effect, temperature effect and wear damage of wet cutting diamond saw blade
In the process of cutting ceramic tile, the wet cutting diamond circular saw blade will be subjected to alternating loads such as centrifugal force, sawing force, and sawing heat, which will cause the wet cutting diamond circular saw blade to be damaged by grinding.
Force effect of diamond saw blade
In the process of sawing porcelain tile, the wet cutting diamond saw blade is subjected to the action of axial force and tangential force. Due to the presence of forces in the circumferential and radial directions, the saw blade is wavy in the axial direction and disc-shaped in the radial direction. These two kinds of deformation will cause uneven marble tile cutting surface, more ceramic tile waste, loud noise and increased vibration during sawing, resulting in early damage of diamond segments and reduced saw blade life.
Temperature effects during cutting
The traditional theory holds that the influence of temperature on the process of wet cutting diamond saw blade is mainly manifested in two aspects: one is to cause the stoneization of diamond in the segments. Second, the thermal stress between the diamond and the matrix causes the diamond particles to fall off prematurely. New research shows that the heat generated in the process of cutting porcelain tile is mainly transferred to the segments. The temperature of the arc zone is not high, generally between 40 and 120 °C. The abrasive grinding point temperature is relatively high, generally between 250 ~ 700 ℃. The coolant only reduces the average temperature of the arc zone, but has little effect on the temperature of the abrasive particles. Such a temperature will not cause carbonization of graphite, but will change the friction properties between the abrasive particles and the workpiece, and cause thermal stress between the diamond and the additive, resulting in fundamental bending of the failure mechanism of the diamond. Studies have shown that the temperature effect is the biggest factor affecting the breakage of wet cutting diamond saw blades.
wet cutting diamond saw blade wear and tear
Due to the force effect and temperature effect, the wet cutting diamond saw blade tends to be worn and damaged after a period of use. The main forms of abrasion damage are as follows: abrasive wear, local crushing, large-scale crushing, falling off, and mechanical abrasion of the binder in the direction of the sawing speed. Abrasive wear: The diamond particles are constantly rubbed against the marble tile, the edges are passivated into a flat surface, the cutting performance is lost, and the friction is increased; the heat of sawing will cause a graphitized thin layer on the surface of the diamond particles, which greatly reduces the hardness and aggravates the wear. Local breakage: The surface of diamond particles is subjected to alternating thermal stress and alternating cutting stress, and fatigue cracks will appear and local breakage will reveal sharp new edges, which is an ideal wear pattern. Large area crushing: The diamond particles are subjected to impact load when cutting in and out, and the more prominent particles and grains are consumed prematurely. Falling off: The alternating cutting force causes the diamond particles to be continuously shaken in the bond to loosen. At the same time, the abrasion of the binder itself and the heat of sawing during the process of sawing ceramic tile soften the binder. This reduces the holding force of the bond, and when the cutting force on the particles is greater than the holding force, the diamond particles will fall off. Either type of wear is closely related to the load and temperature to which the diamond particles are subjected. Both of these depend on the sawing process and cooling and lubrication conditions.
How to get the best cutting results with wet cutting diamond saw blades
When the wet cutting diamond saw blade cuts workpieces such as marble tile, concrete and ceramics, the diamond particles acting as a blade on the surface of the wet cutting diamond saw blade are firmly embedded in the matrix, and the diamond exposed on the surface of the saw blade continuously grinds the cutting surface of the workpiece so as to achieve high machining efficiency. Purpose. The surface diamond used for cutting will continue to wear during processing, and at the same time the wear of the matrix allows new diamond particles to be gradually exposed. In order to obtain the best cutting process conditions, the balance between tool life and cutting speed needs to be improved. Generally, for difficult-to-cut workpieces, high-strength diamond should be selected, and at the same time, the wear of the matrix should be coordinated with the wear of the diamond, so that the tool can be effectively cut and worn normally. For the diamond tool matrix, improper selection of diamond type, size and concentration can lead to abnormal tool wear or loss of cutting function.
Factors affecting the cutting performance of wet cutting diamond saw blades
In addition to diamond and matrix selection, there are several other factors that can have a very large impact on the sawing performance of the saw blade, including: ① the manufacturing method and process parameters of the segments or cutting edges; ② the performance of the workpiece; ③ sawing conditions ; ④ cooling efficiency; ⑤ bonding quality of segments and metal matrix; 6 structure and tension of metal matrix;
Wear of diamond blades
In order to facilitate the removal of chips, the cutting process parameters must be adapted to the performance of the cutting edge and the machined workpiece, so that the suspension is kept within a certain thickness, so as to avoid the substrate from being exposed to harsh wear conditions. The change of the cutting direction will also affect the performance of the tool, which should be properly adjusted according to the movement direction, saw blade specifications and technical parameters. The effect of the adjustment is twofold.
First, during the up and down cutting process, the relative direction of the resultant cutting force is different from that of the supporting frame. In the upward or downward cutting mode, when the resultant force deviates too much from the direction of maximum hardness, an unstable cutting state will occur, resulting in harmful vibrations in the process of cutting porcelain tile. If the spindle support force is in the vertical direction, increasing the ratio of the tangential force to the normal force will result in lower stability when cutting ceramic tile upwards, and the opposite effect when cutting marble tile downwards.
Second, when the blade rotates in the opposite direction, the diamond loading conditions will vary greatly. Under the condition that the porcelain tile is cut down, when the diamond is in contact with the ceramic tile, it will be pressed into the marble tile with the maximum depth. Subsequently, the diamond particles gradually stand out along the surface layer of the worn workpiece, and finally separate from the workpiece. Contrary to the downward cut, the diamond penetration depth gradually increases during the upward cut, and finally reaches a maximum value when it leaves the groove. It can be seen that when the saw blade is turned downward, it is easy to cause diamond chipping.
Experiments show that the wear pattern on the circumference of the wet cutting diamond saw blade also depends on the cutting method. When cutting upwards, the entire diamond segment is subject to wear at the same speed, while when cutting downwards, the wear speed of a single diamond segment varies, which tends to make the worn parts tend to the periphery of the wet cutting diamond saw blade, which is opposite to the direction of rotation. Due to the influence of the above reasons, the additional load of cutting diamond particles causes the cutting amount of the material to continuously increase in the orderly incisions, thereby forming a spiral wear process, which makes the following diamonds unable to participate in the cutting work.
Contact Us
If you’re interested in Best Wet Cutting Diamond Saw Blade for Marble Porcelain Ceramic Tile, please feel free to contact us, (E-mail: [email protected] Phone/WhatsApp: 0086-15805032000 or filling out the form below) we will keep providing quality products and excellent service for you.