Diamond Gang Band Saw Stone Cutting Blades Suppliers
Diamond Gang Band Saw Stone Cutting Blades can be supplied by Eonyx, which is the leading manufacturer of diamond saw blades. Our sophisticated factory can supply 20,000 pieces of saw blades per month. As a professional supplier, we can guarantee competitive wholesale price and stable quality.
Saw Blades Processing Process
We have been focusing on the technical development and production of diamond tools for more than 28 years.
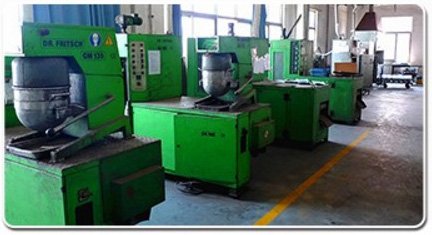
1. Powder Milling
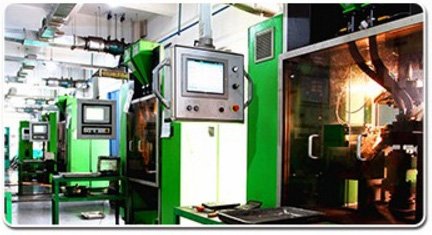
2. Segment Pressing

3. Segment Sintering
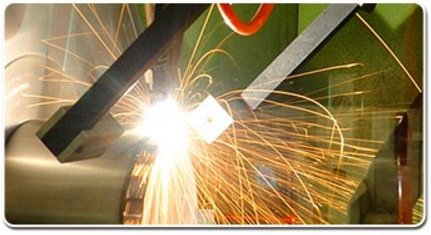
4. Segment Welding
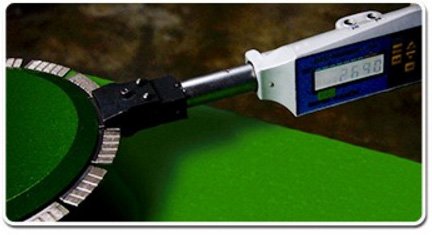
5. Welding Strength Inspection
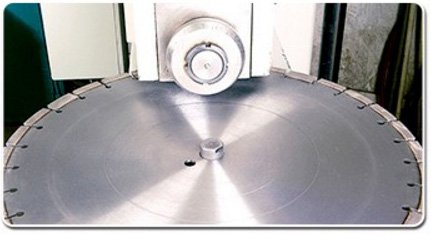
6. Stress Release Rolling
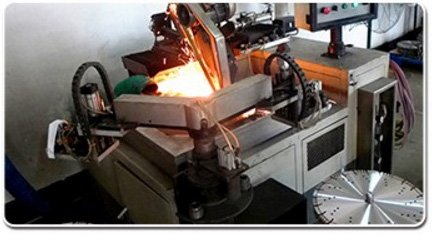
7. Blade Polishing
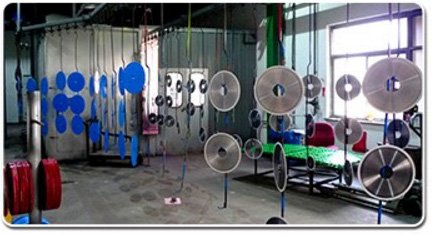
8. Blade Painting
Quality Inspection
Excellent product quality is our commitment to customers as always.
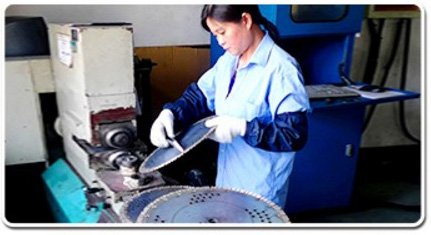
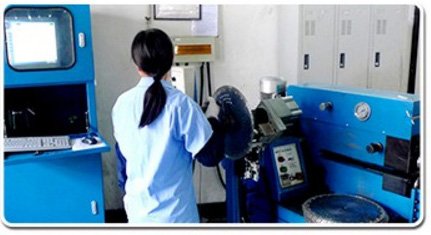
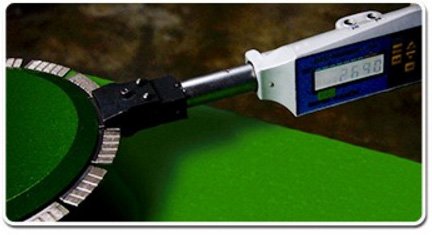
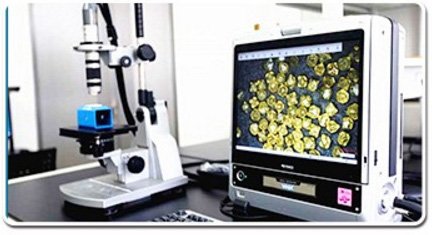
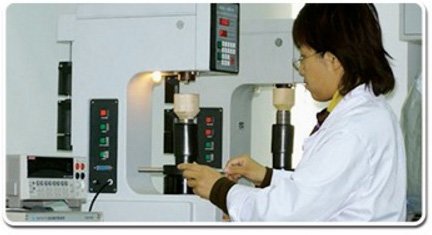
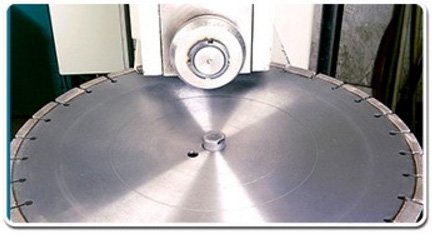
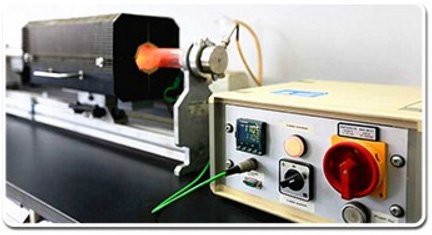
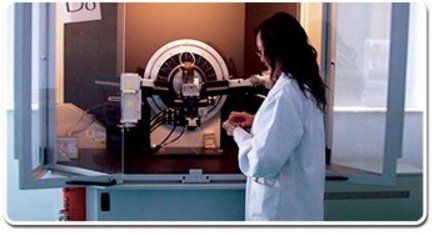
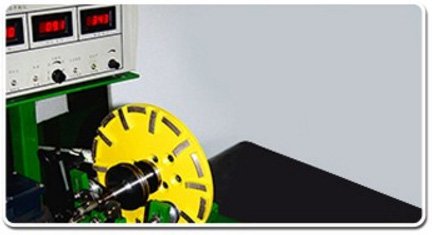
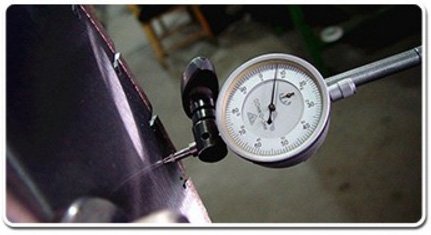
Advantages of Diamond gang saw blades
The advantage of Diamond gang saw blades is that they can process large-sized plates, which can improve stone processing specifications (large-sized plates), quality, efficiency and yield, and may replace traditional circular saws (small-dry circular saws that can process large-scale plates). Radius) and diamond sand saw (the surface quality of the processing plate is poor, the efficiency is low, the yield is low, and it is not environmentally friendly).
Stone cutting band saw blades are mainly used for large slab processing of marble and medium and soft granite. Its main advantages are: (1) high output, the cutting efficiency is 5~10 times higher than that of the sand saw, and 10m more rough board per cubic meter than the diamond circular saw blade; (2) the surface of the processed flat plate The roughness value is low, and rough grinding can be omitted in the subsequent surface processing process, and only fine grinding, polishing or direct polishing is required; (3) energy is saved, and the energy consumption per unit output is greatly reduced. Therefore, its comprehensive production cost is low, and it gradually replaces the sanding saw.
Classification of Diamond band saw blade for stone
Diamond band saw blade for stone can be divided into small diamond gang saw blades according to the number of diamond saw blades installed. Medium-sized diamond gang saw blades are installed with between 10 and 40 saw blades. Large diamond gang saw blades are installed with more than 40 to 120 saw blades.
According to the structure and movement mode of stone cutting band saw blades, it can be divided into: the block material is fixed, the saw frame is reciprocating horizontal and linear motion, and the traditional translation type stone cutting band saw blades are cut by descending feed; Modern translation stone cutting band saw blades for material lifting and feeding cutting; vertical reciprocating linear motion of saw blades, vertical diamond gang saw blades for horizontal moving and feeding of blocks, etc.
There are generally two types of diamond frame saws: one is a horizontal saw, the diamond gang saw blades are installed horizontally, and are generally used for marble cutting. Each saw machine is equipped with 40~100 saw blades: the other is a vertical saw machine. The row saw blades are installed vertically up and down, which is generally used for granite cutting. Each saw machine is equipped with 6~25 row saw blades. The biggest advantage of the vertical frame saw is that the cutting product – rock powder can be easily discharged from the saw gap, which reduces the consumption of diamonds, so it is more suitable for processing granite with strong abrasiveness.
Diamond gang saw blades structure
Diamond gang saw blades consist of a gang saw base and diamond segments. At present, we can supply high quality base for stone cutting band saw blades. The requirements for the steel base of stone cutting band saw blades are: (1) high speed, stable and durable under the reciprocating action of the gang saw; (2) high fatigue strength, and not easy to deform and fail. Its tensile strength should be (1400±80)MPa, and its hardness reaches 42~44HRC during bright quenching; (3) it has effective thermal conductivity, which can reduce the possibility of martensite formation due to dry overheating when welding the diamond segments (4) Perfect segments edge treatment to ensure strong combination of diamond segments and matrix.
Diamond gang saw blades manufacturing process
The manufacturing process of diamond gang saw blades is basically the same as the manufacturing process of the aforementioned diamond welding saw blades, including metal powder, diamond calculation, weighing, mixing, hot and cold pressing of saw segments, welding surface grinding, preparation, cleaning and Final welding of Diamond Segments and other processes.
Manufacture of segments of stone cutting band saw blades
The selection of raw materials includes the following three parts.
(1) Selection of metal powder. The same as the above-mentioned technical conditions for the metal powder used in the manufacture of diamond saw blades.
(2) The choice of diamond. Because the working condition of the diamond gang saw is different from that of the diamond circular saw, it reciprocates with the saw. Therefore, the force of the row saw diamond particles is different from that of circular saw blade cutting. The action surface (edge) of the diamond particles is on the front and rear surfaces of the movement direction, unlike the circular saw blade with a matrix behind the diamond particle cutting surface. The protrusions firmly inlay the diamond, so in addition to the matrix with a strong holding force, the diamond is also required to have high strength. Otherwise, the diamond particles are easy to be broken when the cutting force is applied, which reduces the cutting force. However, high-strength diamonds have high crystal integrity, smooth and flat surfaces, and are difficult to remain in the matrix for a long time, so diamonds with high-strength and rough surfaces need to be used.
(3) Selection of hacksaw blades. When installing the steel belt of the gang saw blade, a tension force needs to be applied, and its average size is 8~12T/piece. Under such a large tension force, the steel belt saw blade is required to have a certain rigidity and strength, and the tensile strength of the steel The strength is (1340±80)MPa, the hardness is 40~44HRC, and the material is generally 65Mn steel.
Diamond Segments Design
(1) Diamond segments specifications and dimensions. The length of the segments of the gang saw is short, usually 20mm, mainly to make the segments of the diamond band saw blades have a larger unit pressure to ensure a certain sawing efficiency. The serration height is generally 7mm. The Diamond Segments should not be too high. The cutting force of the excessively high Diamond Segments will have a large torque on the welding surface of the Diamond Segments during sawing, which will affect the welding strength of the Diamond Segments.
(2) The geometry of the Diamond Segments. In order to reduce the contact surface between the diamond Diamond Segments and the cut rock, reduce the cutting lateral force and
Friction, the two sides of the diamond segments should be made into a trapezoid, and the front side should be in a groove shape after grinding. During the cutting process, only the front side of the diamond segments and the edges on both sides of the front side are in contact with the rock, which reduces the friction force. There is a groove shape on the front of the diamond segments, which improves the lateral extrusion of the diamond segments, improves the cutting efficiency and cutting quality, prevents cutting deviation, and can also improve the service life.
(3) Serrated carcass. The basic task of the matrix is to firmly hold the diamond abrasive grains, but during the cutting process, the matrix should be worn continuously so that the diamonds can be better exposed, and without the wear of the matrix, it is impossible to produce cutting. However, the wear rate of the carcass should be adapted to the nature of the cut stone. If the carcass wears too fast, the diamond will fall off prematurely without fully functioning, resulting in a decrease in the life of the saw segments; on the contrary, if the carcass wears too slowly, the diamond will emerge If it is too low, it will affect the cutting efficiency of the Diamond Segments, and at the same time consume too much power, waste power, and cause the motor to burn out prematurely in severe cases. The low cutting efficiency of the Diamond Segments will also cause the saw machine to vibrate too much during the cutting process, which will cause the saw blade to deviate, resulting in a decrease in the quality of the cut sheet. Since the properties and abrasiveness of various types of stone materials vary greatly, a suitable balance must be found between maintaining the firmness of the diamond and the wear resistance of the matrix.
(4) The concentration and particle size of diamond. The diamond concentration used in gang saw blades is usually between 6% and 20%. In principle, when using high-quality and high-grade diamond, the concentration can be chosen to be lower, and vice versa. When manufacturing diamond band saw blades, considering that the speed of the gantry line is very low, the processing process is mainly grinding, so the diamond grain size is generally 50/60 mesh, 60/70 mesh, 70/80 mesh, etc.
Sintering process of diamond gang saw blades
The sintering process is the same as the general welding saw blade tip. After the Diamond Segments is hot-pressed, there are some burrs. In order to facilitate welding, it should first be rolled in a rolling polishing machine for 3~5 minutes to remove the burrs, and then the welding surface is ground on the grinding wheel to expose the fresh carcass layer on the welding surface. Keep it smooth.
Inventory and Packaging
Sufficient inventory to ensure delivery and professional packaging to ensure safe transportation. Inner packaging: diamond saw blades are covered by anti-rust paint and plastic, then packed in paper box. Outer packaging is according to the shipping method, if by air, we recommend carton which could reduce weight; if by sea, we recommend crate which is seaworthy. Other packaging is also available upon your request.
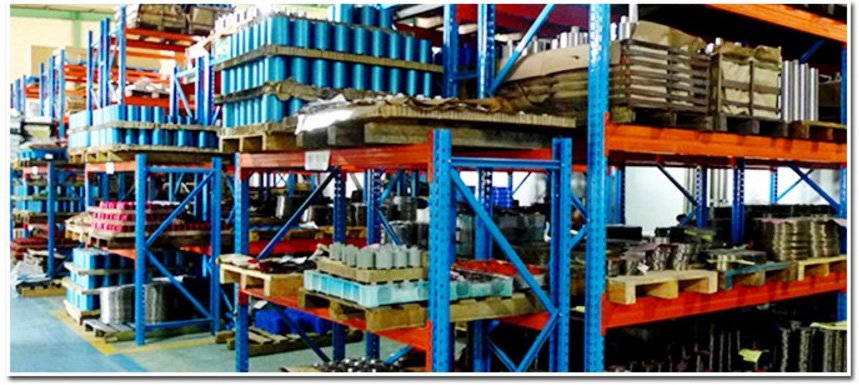
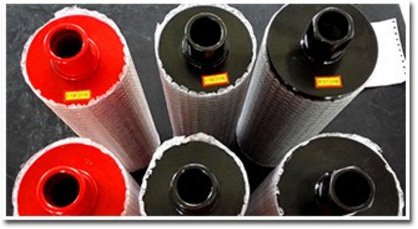
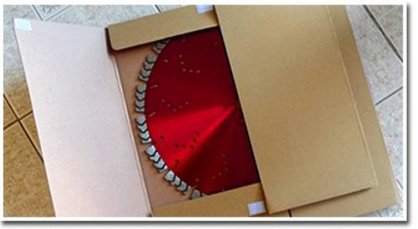
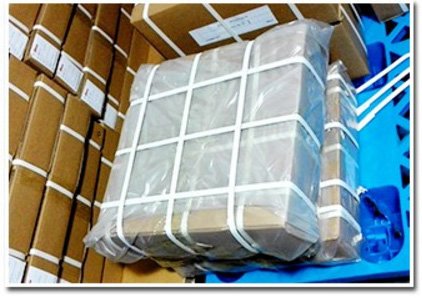
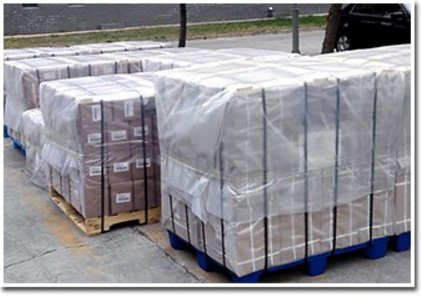
Application of Diamond Cutting Blades
For multi blade cutter, gang saw blade, bridge cutting machine, single arm cutting machine, manual handing machine, able cutting machine, etc. Designed for various hardness stone (soft, medium hard and very hard stones) cutting: granite, marble, sandstone, onyx, limestone, travertine, quartz stone, artificial stone, andesite, volcanic, lava stone, basalt, microcrystal stone, blue stone, dolomite and construction materials (concrete, tile, ceramic, asphalt, floor) to reduce segment cost and increase cutting efficiency.
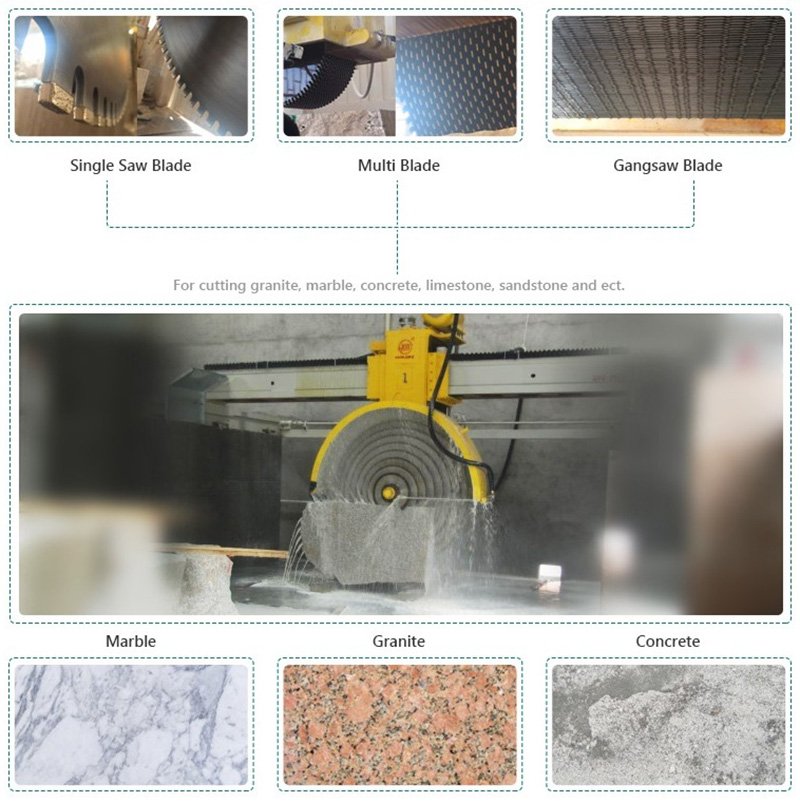
Welding of gang saw blades
The specific welding method is as follows: prepare the base of the diamond band saw blades and fix it on a special frame, measure the effective length of the saw blade, and mark the position of the welding segments with a marker. Check the welding part for rust, if rust needs to be cleaned with a file, so as not to affect the welding strength. Use alcohol or the like to remove the oil on the welding part and start welding. In the welding process, like the diamond circular saw blade, in order to prevent the substrate from being deformed by heat, it can be welded at intervals.
Segments number and distribution
The spacing of the segments on the saw blade is unequal and can be arranged regularly or irregularly. Generally, the Diamond Segments distribution in the middle is denser, and the two sides are sparser. The segments are alternately distributed with long and short intervals on the steel belt, so that the vibration frequencies of the adjacent two segments are different. This is to avoid harmful resonance during the sawing process and reduce the vibration of the entire saw blade. The spacing of the diamond segments depends on the number of segments on the contact surface of the stone. The spacing has a certain range, and each segments must have a sufficient pressure. If the spacing of the segments is too small, the rigidity of the saw blade base and the entire mechanical equipment will not be enough to reach each segments. The required pressure reduces the cutting efficiency; on the contrary, if the spacing between the segments is too wide, the load on the segments is too large, so that the exposed ganglia is prone to fragmentation.
The number of segments on the saw blade is calculated from the distance between the segments and the length of the segments on the saw blade. For the frame gang saw with horizontal movement, when sawing soft stone, the segments spacing is about 70~110mm, and when sawing hard stone, the segments spacing is 95~115mm.
Technical measures to improve the quality of diamond gang saw blades
In order to improve the quality of diamond band saw blades, you can start from the following aspects:
(1) Different from the circular saw. When the gang saw blade is working, it moves back and forth. The matrix has no tadpole support for the diamond, and the stress conditions are harsh. In addition, there are a large number of saw blades assembled on the saw frame. The spacing, parallelism, perpendicularity and tension of the saw blades must be adjusted. Therefore, there are many influencing factors, and the production process must be optimized to ensure the quality and efficiency of the diamond band saw blades work.
(2) Diamond plating. The diamond coated metal layer is beneficial to improve the holding force with the carcass. Production and application practice shows that diamond titanium plating or diamond cladding plating (TiC+Ti-Cr+Ni) can form a chemical bond with the metal matrix, reduce the shedding of diamonds, increase the height of the blade, improve the sawing efficiency, and prolong the service life.
(3) The cold-pressed diamond segments is subjected to reduction treatment before vacuum hot-pressing sintering. The reduction temperature and time are determined according to different matrix formulations, so as to reduce the oxygen content, create conditions for activation sintering, and improve the bonding force between diamond and matrix.
(4) The sandwich multi-blade structure diamond segments can effectively break the rock and create multiple free surfaces to improve the sawing efficiency. At the same time, the multi-blade structure is conducive to the high-speed balanced sawing of the diamond segments, and it is not easy to produce deflection and yaw.
(5) The diamond segments adopts a trapezoidal structure and an inclined bottom water tank to reduce the friction between the diamond segments and the stone surface, which is beneficial to cooling, slag holding and slag discharge.
(6) The use of thin substrate and thin gang saw blade reduces the width of the saw seam, which is beneficial to improve the sawing efficiency and the rate of board ejection.
(7) Pay attention to the on-site service of the diamond band saw blades. When installing the gang saw blades, attention should be paid to controlling and adjusting the verticality, parallelism of the saw blade, the concave curvature of the saw blade, and adjusting the tensile stress. Ensure the normal operation of the saw blade, and prevent the discovery of problems such as partial board, poor flatness of the board surface, and abnormal wear of the diamond segments.
Contact Us
If you’re interested in Diamond Gang Band Saw Stone Cutting Blades, please feel free to contact us, (E-mail: [email protected] Phone/WhatsApp: 0086-15805032000 or filling out the form below) we will keep providing quality products and excellent service for you.